Post by bobby1 on Jan 26, 2014 1:17:06 GMT -5
As many of you are aware I use a 12" carpet covered wheel for polishing nearly all my cabs from the smallest (1/8") to the largest (6"). After about 5 years of significant use the carpet cover wears out.
Example of the wear.
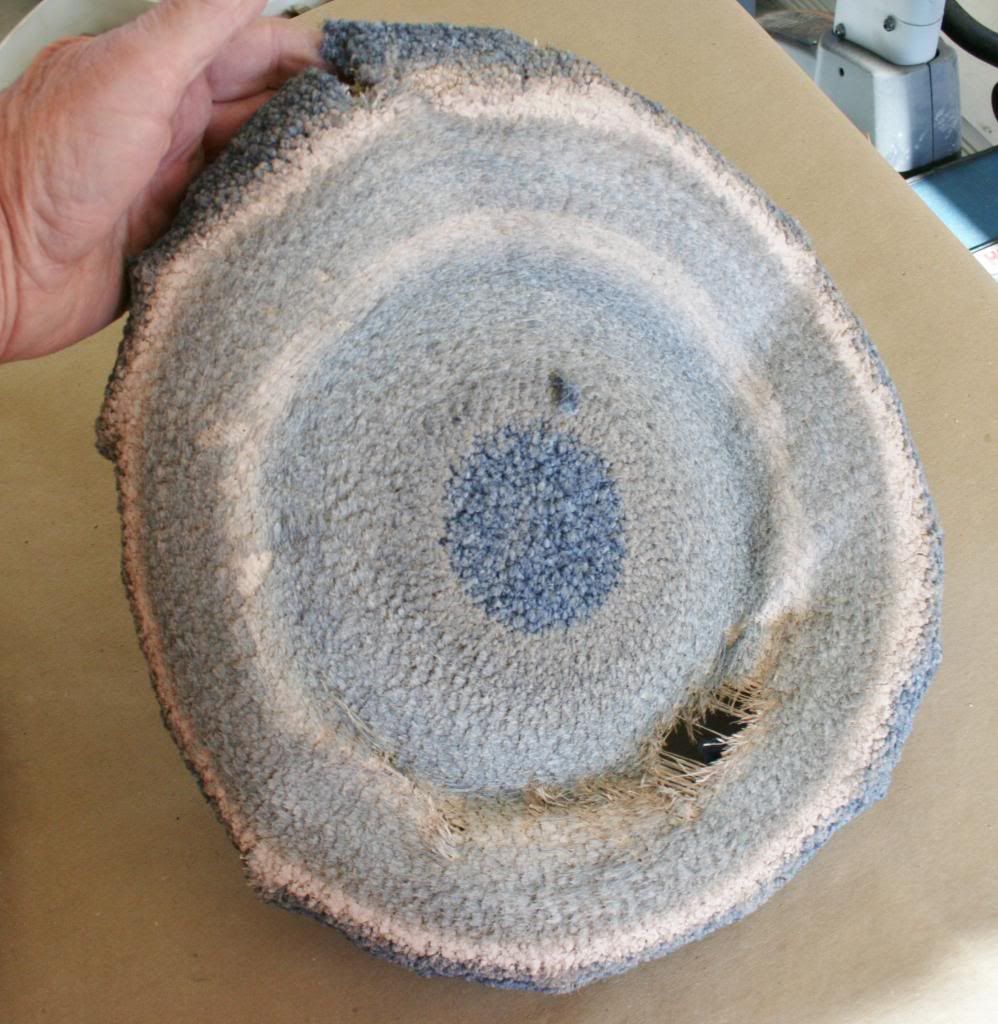
The wheel has a 3/16" foam rubber cover.
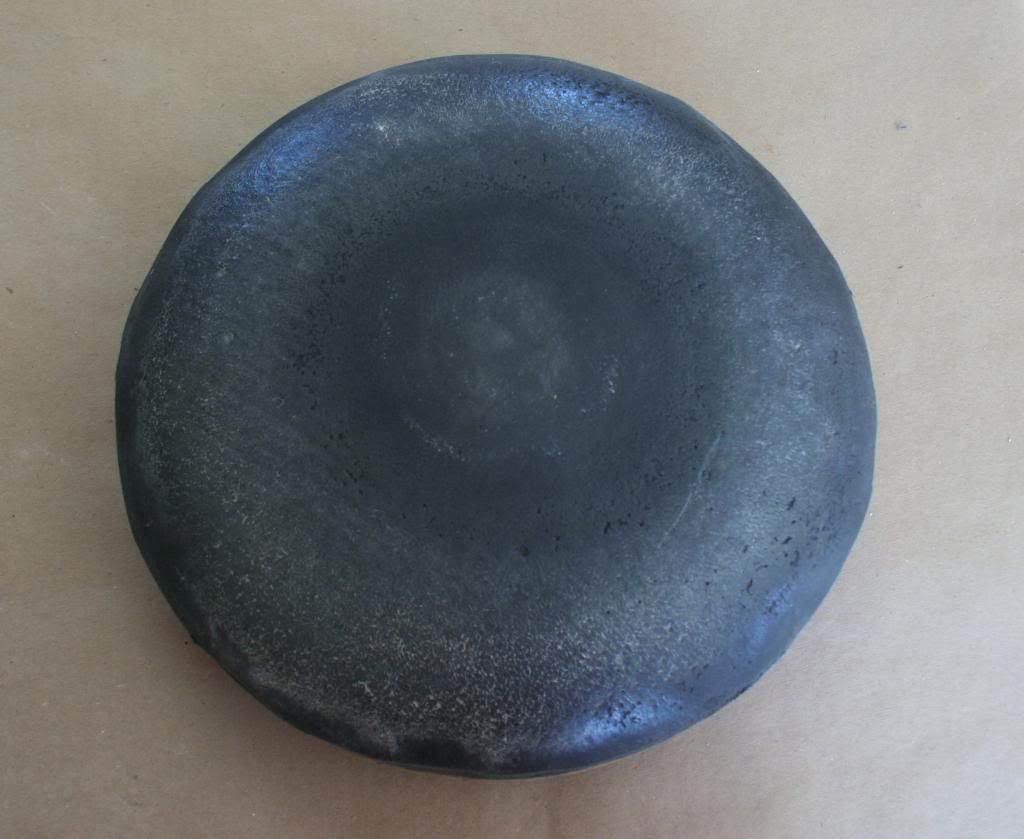
Over which there is a left over leather cover from when I used to use leather for the polishing.
I cover the leather with my carpet. It is a standard office carpet that is 1/4" thick.
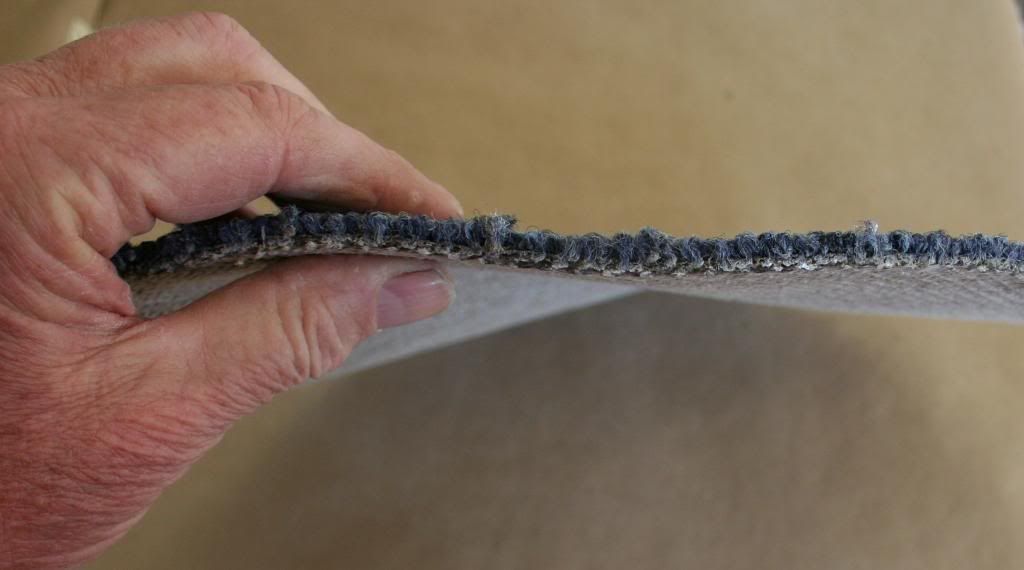
A view of the back of the carpet.
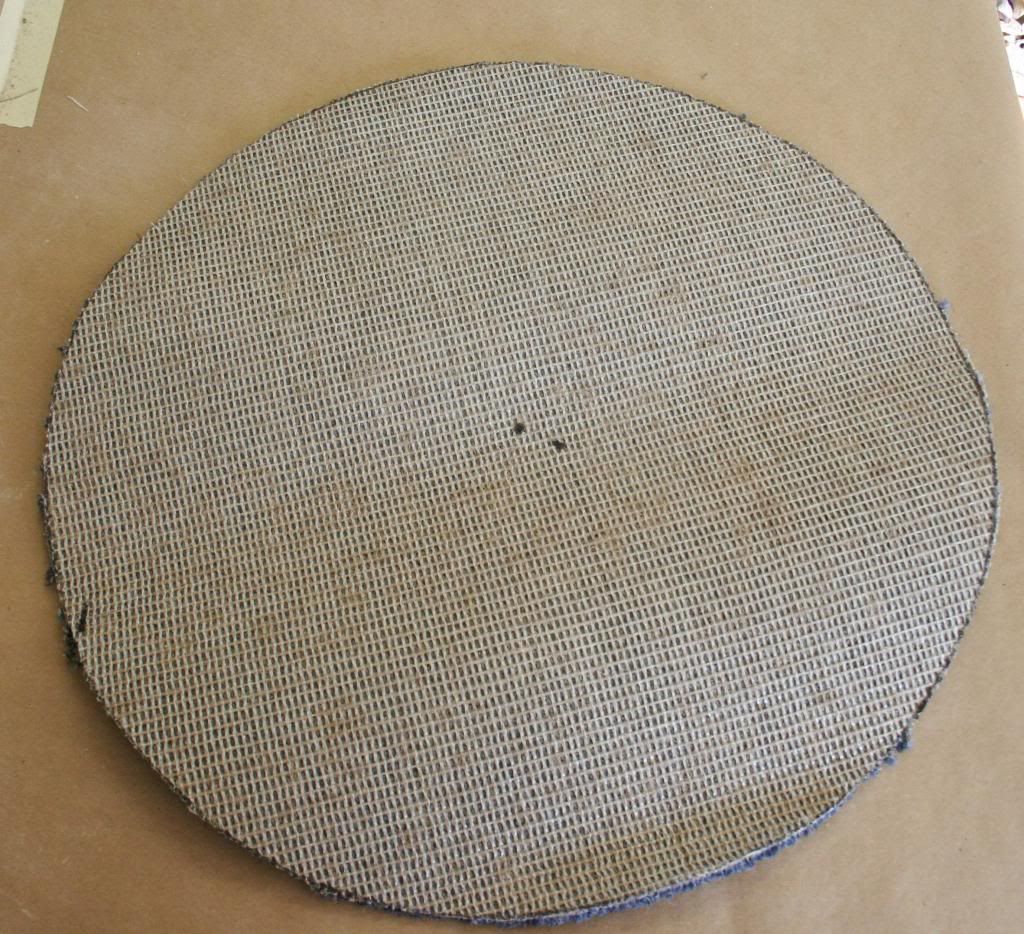
I soak the carpet in water for a couple hours so it will be more pliant to shape over the wheel. I then place the wheel on the carpet and start making "V" shaped gussets around the edge so I can shape it over the edge without it puckering from the excess material.
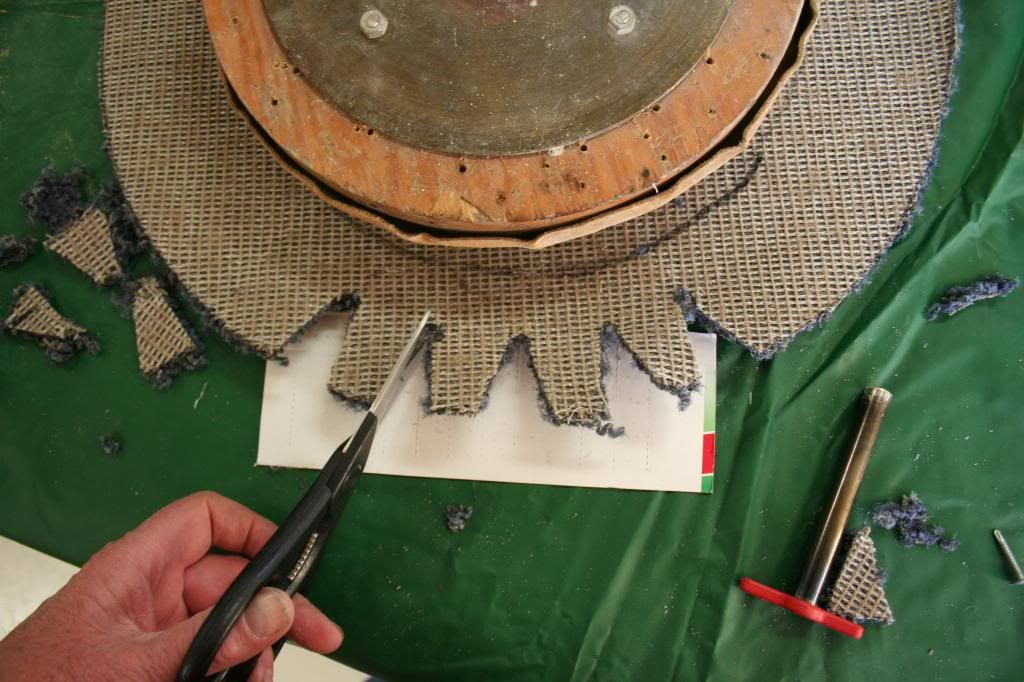
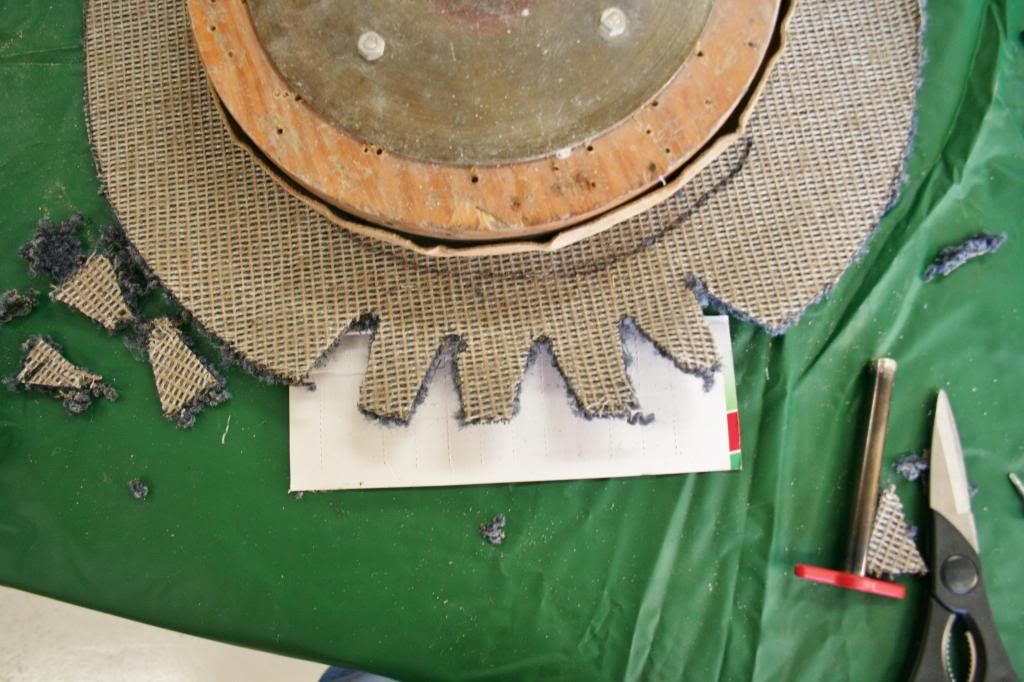
After I make the "V" shaped cuts I use a hole punch in the tip of the "V" to again remove material to prevent the pucker.
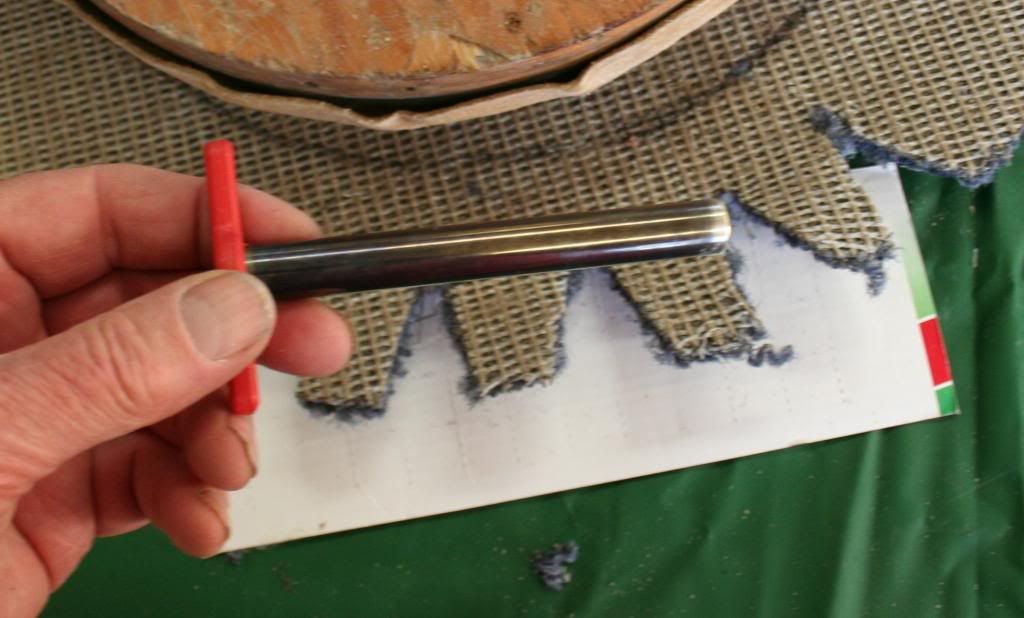
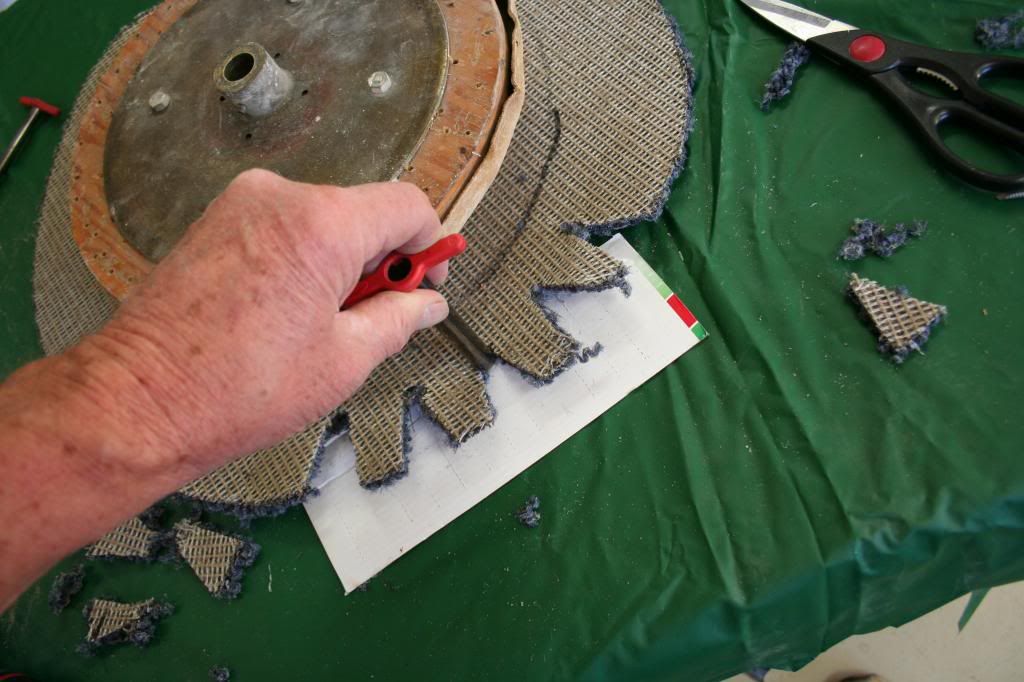
Then I start wrapping the material over the edge and anchoring the section with truss head 1" self drilling screws
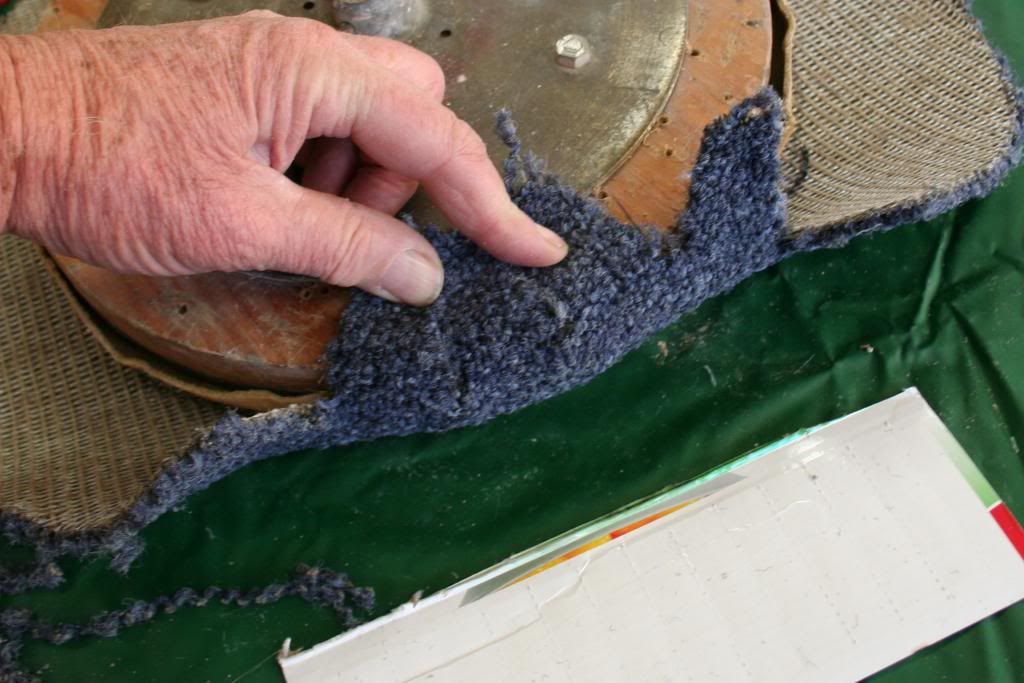
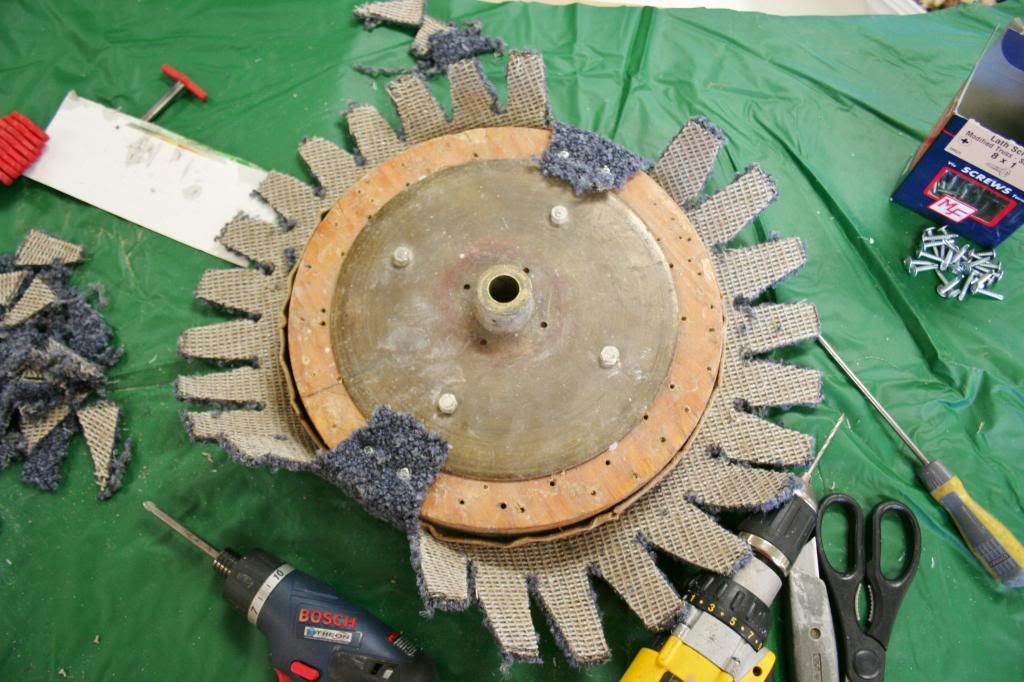
I do two tabs and then go to the opposite side so that the wheel doesn't slip over when I'm working on it.
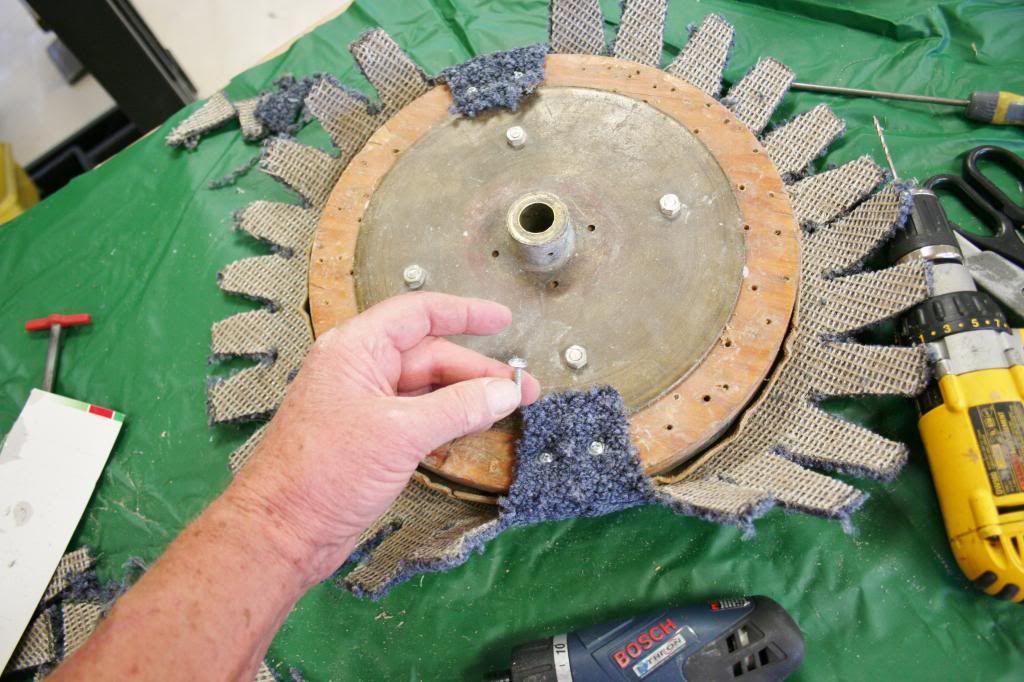
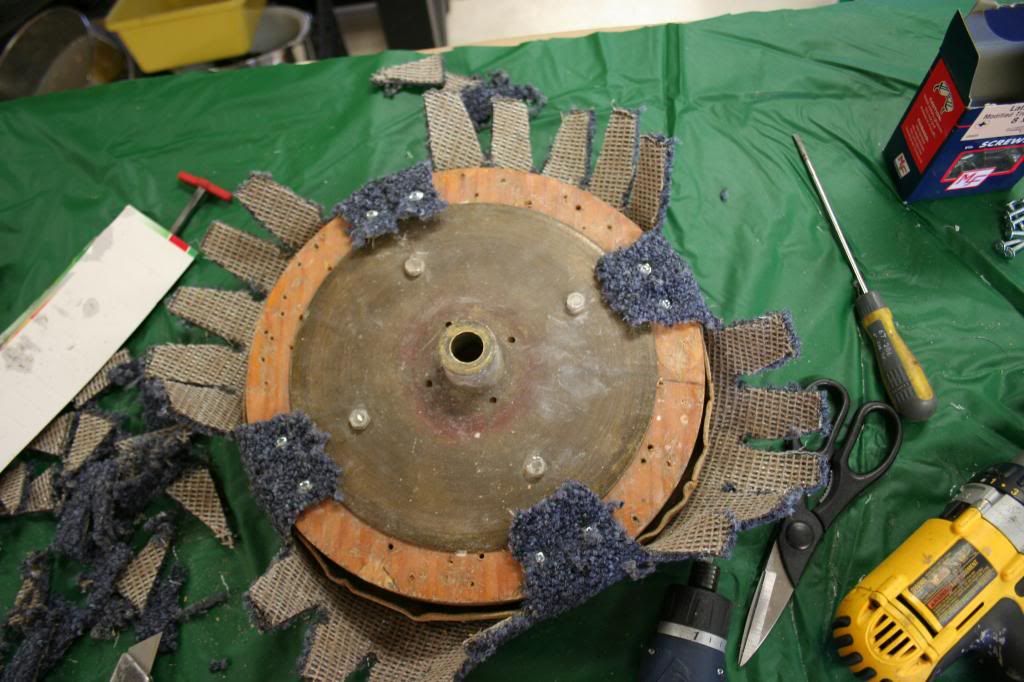
Front view of the completed wheel
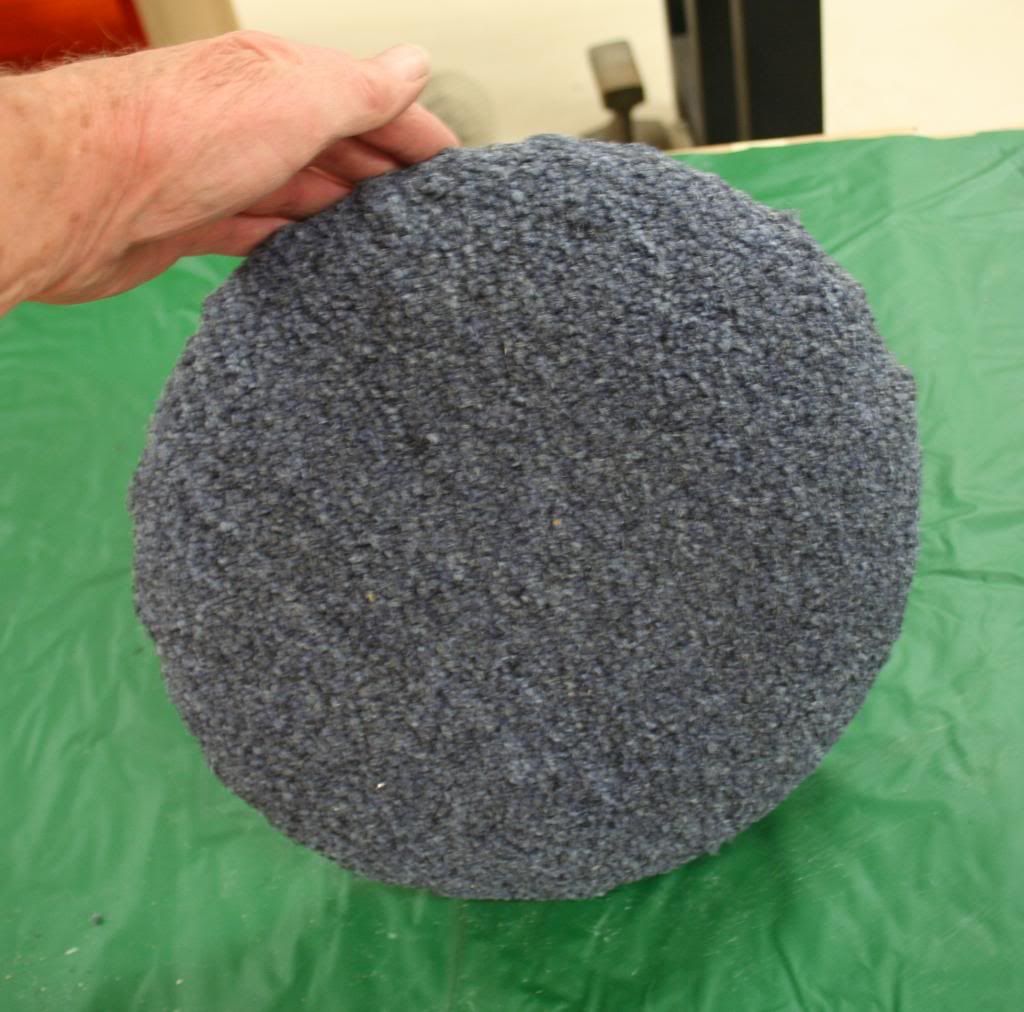
Side views.
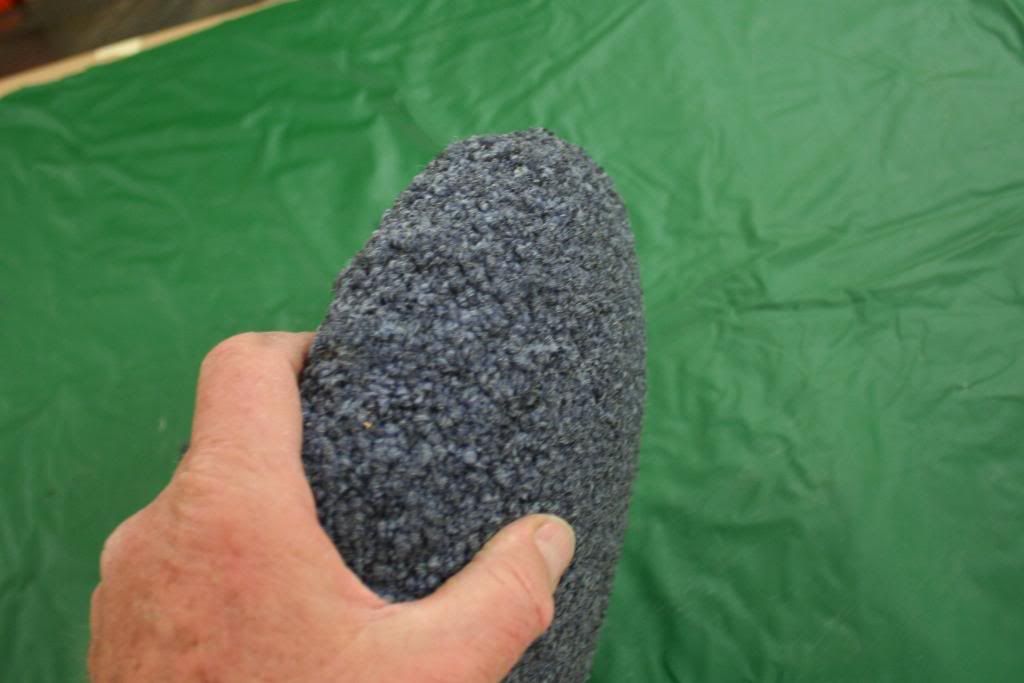
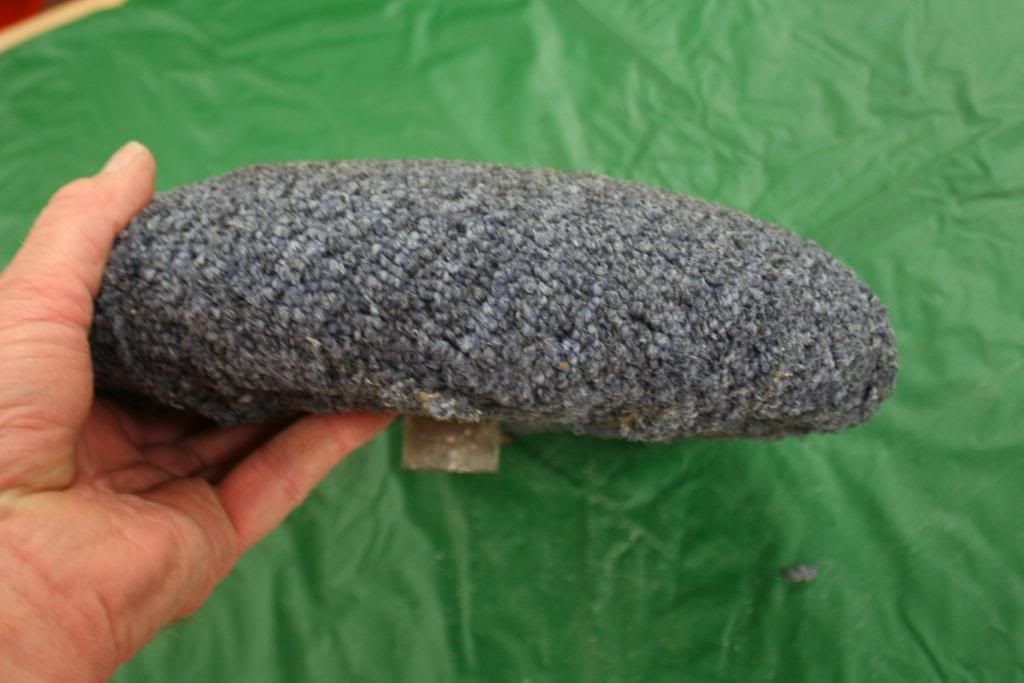
As you may have noticed the wheel has a significant dome in the middle and rounded outer edges. I made it this way so I can readily reach the center of the large cabs (or slabs) and the rounded outer edge allows me to polish the inner curves on a concave sided freeform cab. Here is a photo of it mounted on my (messy) machine.
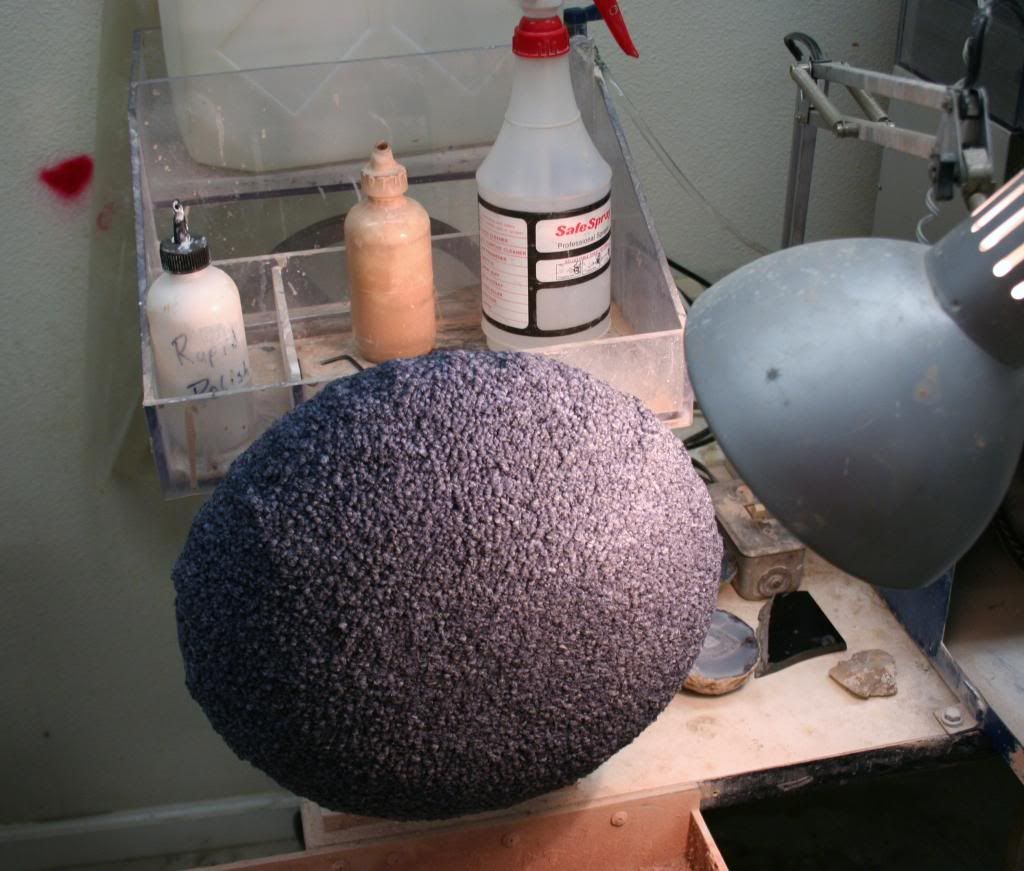
The wheel turns at about 275 rpm and I use cerium oxide for a polish. By using carpet for the cover I can get a significant amount of polish embedded in the knap as well as it holding considerable moisture. This allows me to polish a lot longer before needing to add water or polishing compound.
Sorry if I bored you with so much detail.
Bob
Example of the wear.
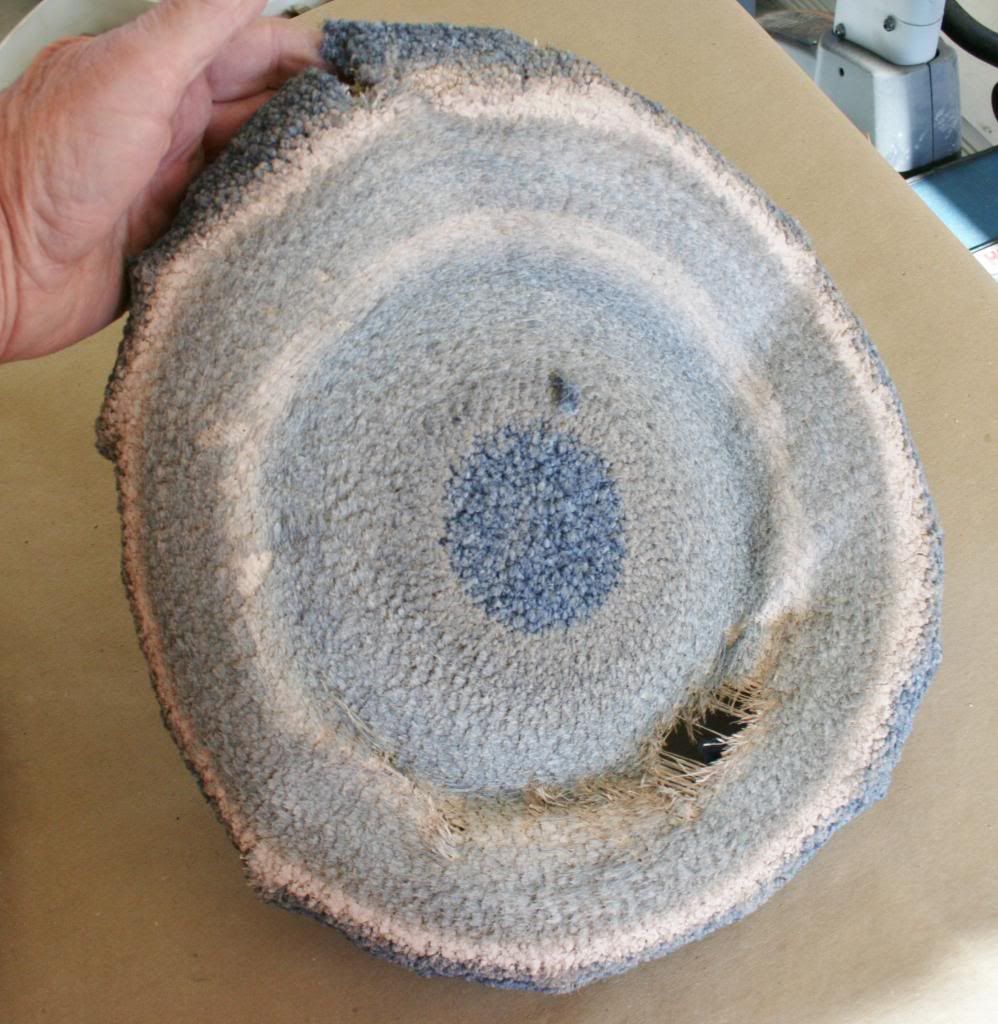
The wheel has a 3/16" foam rubber cover.
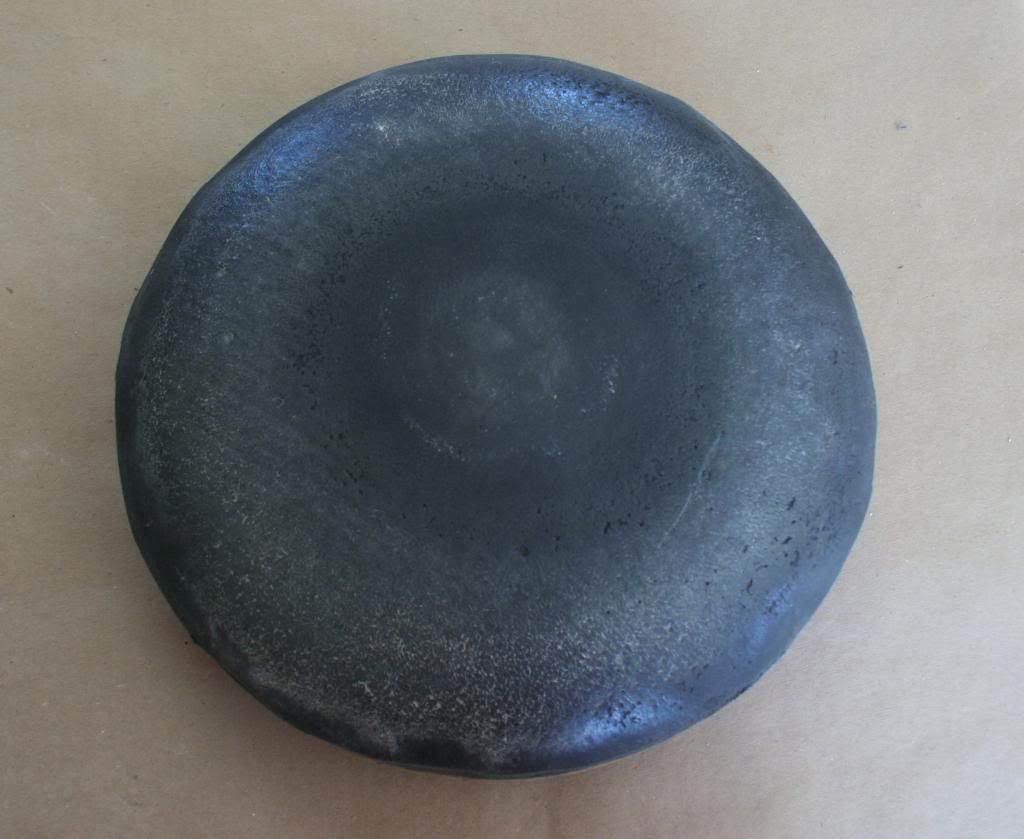
Over which there is a left over leather cover from when I used to use leather for the polishing.
I cover the leather with my carpet. It is a standard office carpet that is 1/4" thick.
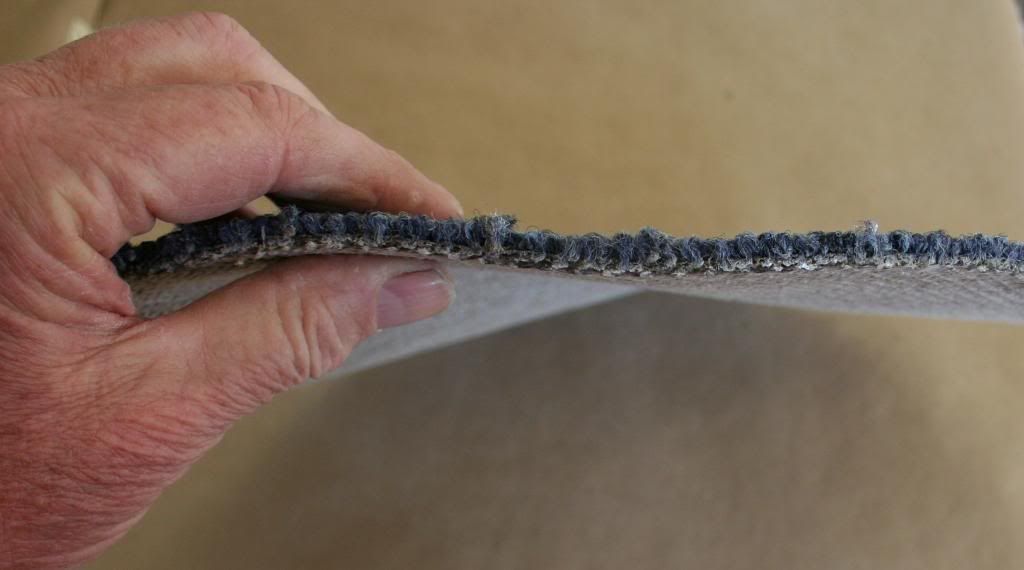
A view of the back of the carpet.
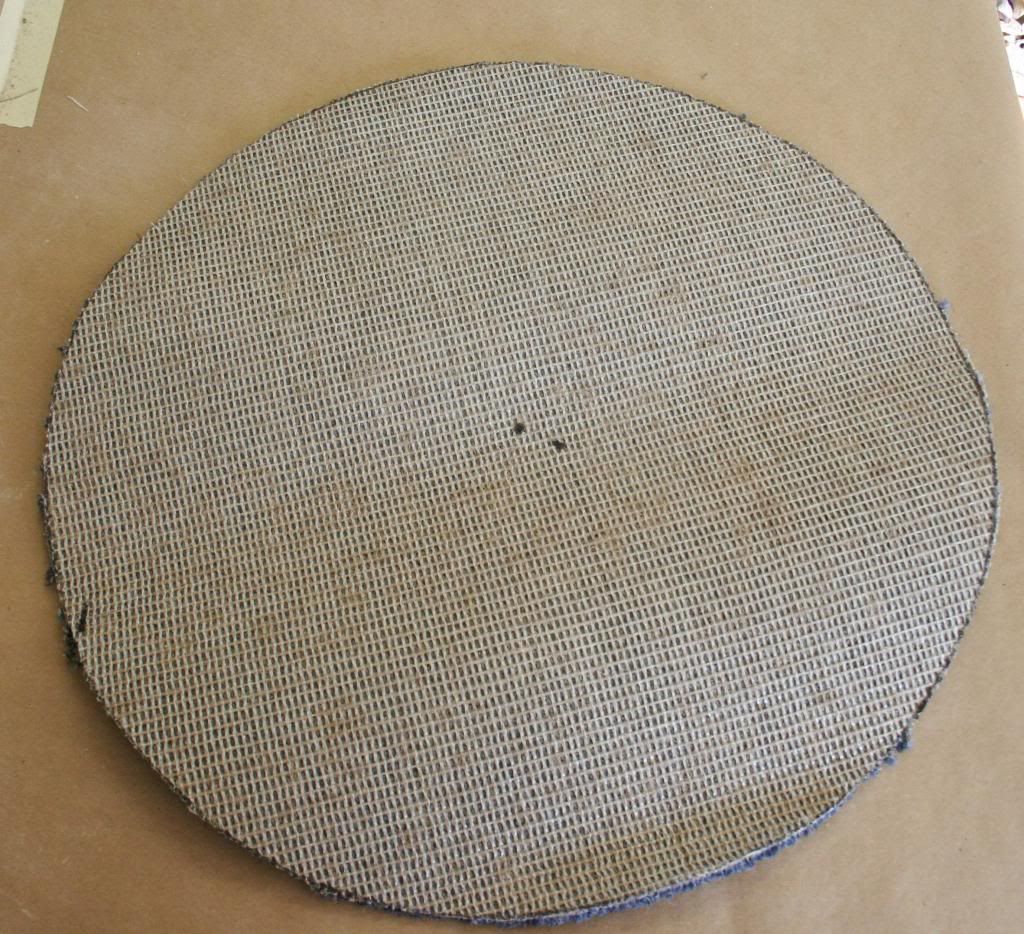
I soak the carpet in water for a couple hours so it will be more pliant to shape over the wheel. I then place the wheel on the carpet and start making "V" shaped gussets around the edge so I can shape it over the edge without it puckering from the excess material.
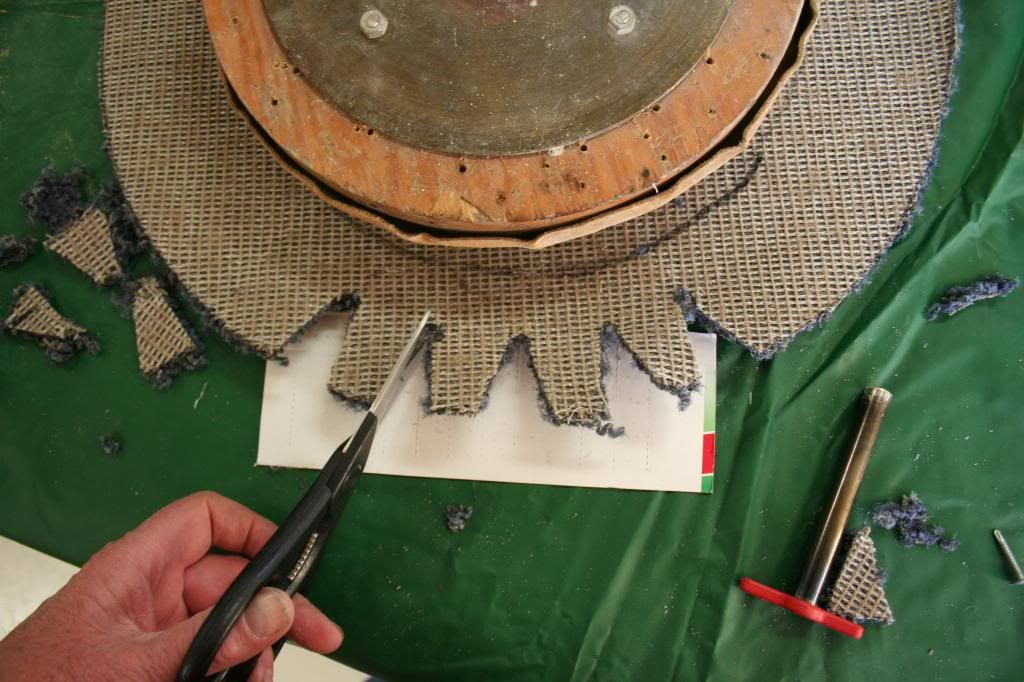
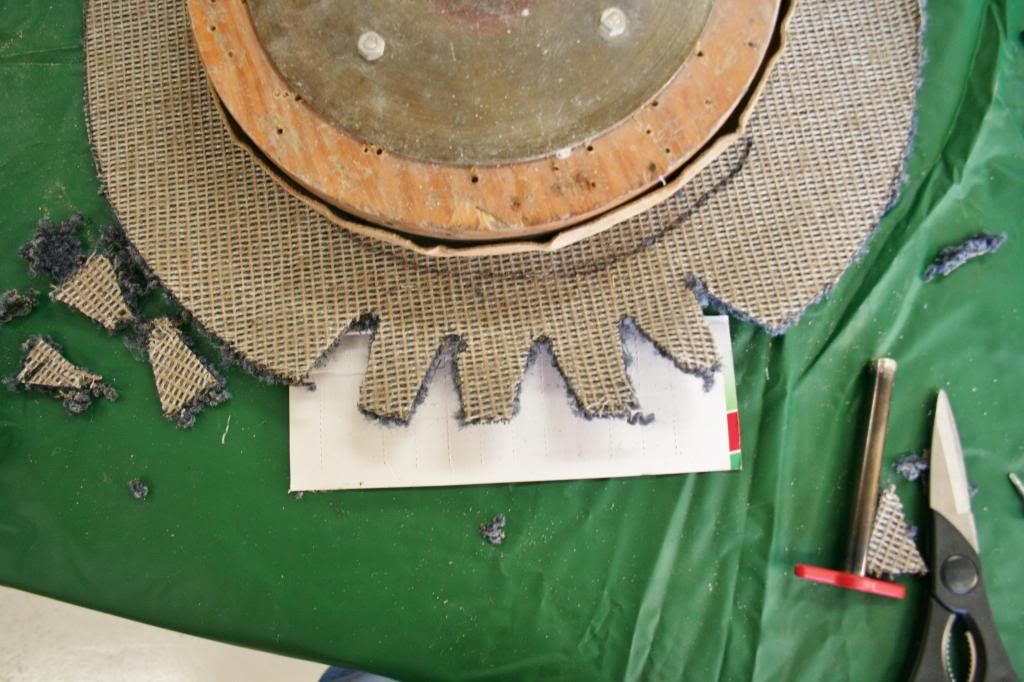
After I make the "V" shaped cuts I use a hole punch in the tip of the "V" to again remove material to prevent the pucker.
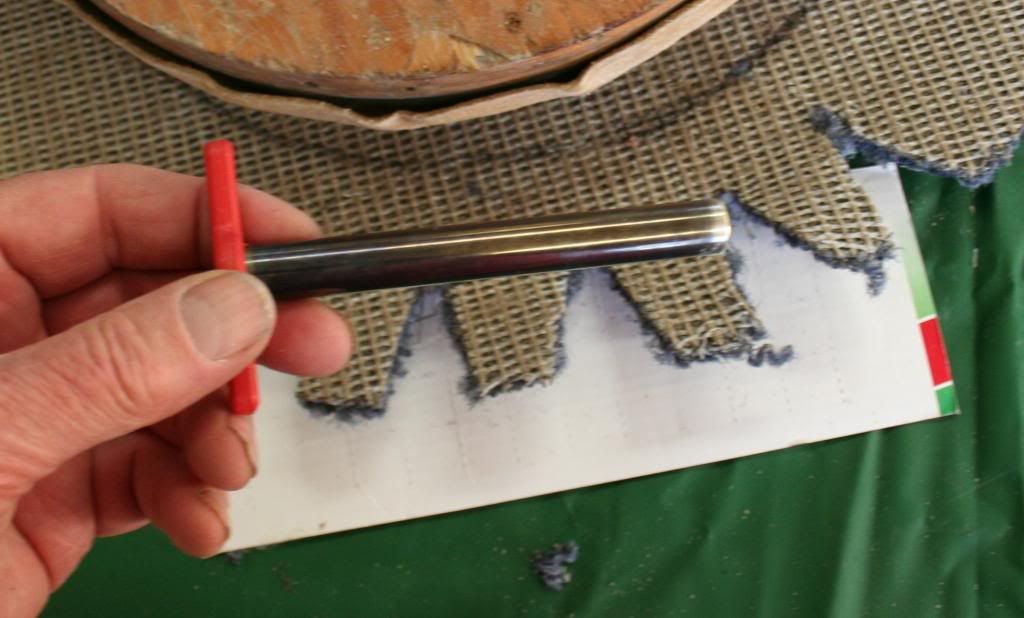
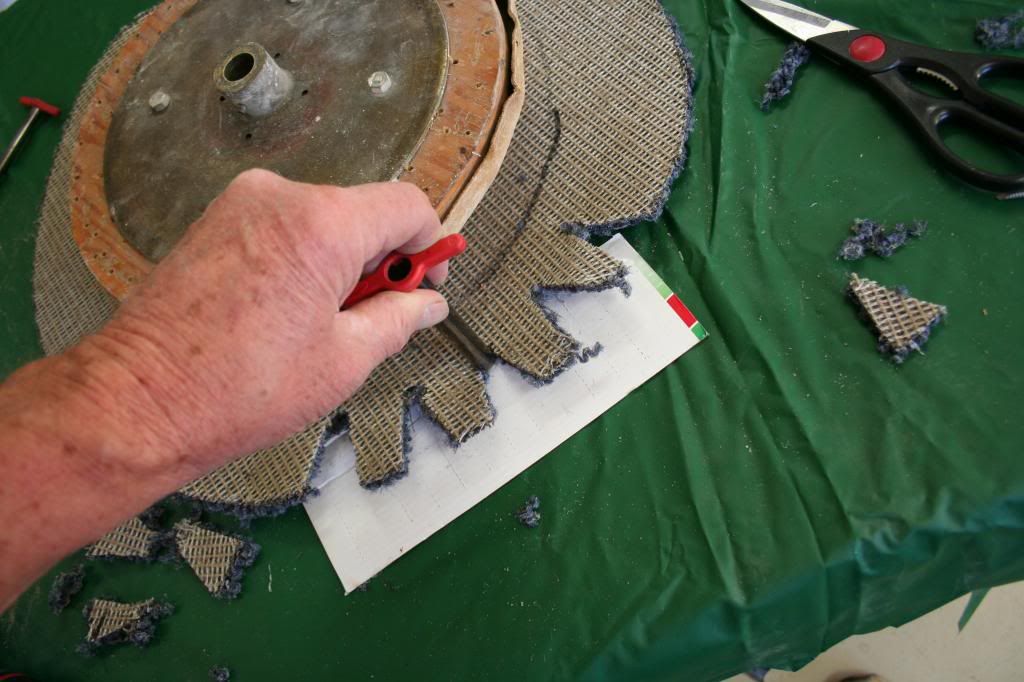
Then I start wrapping the material over the edge and anchoring the section with truss head 1" self drilling screws
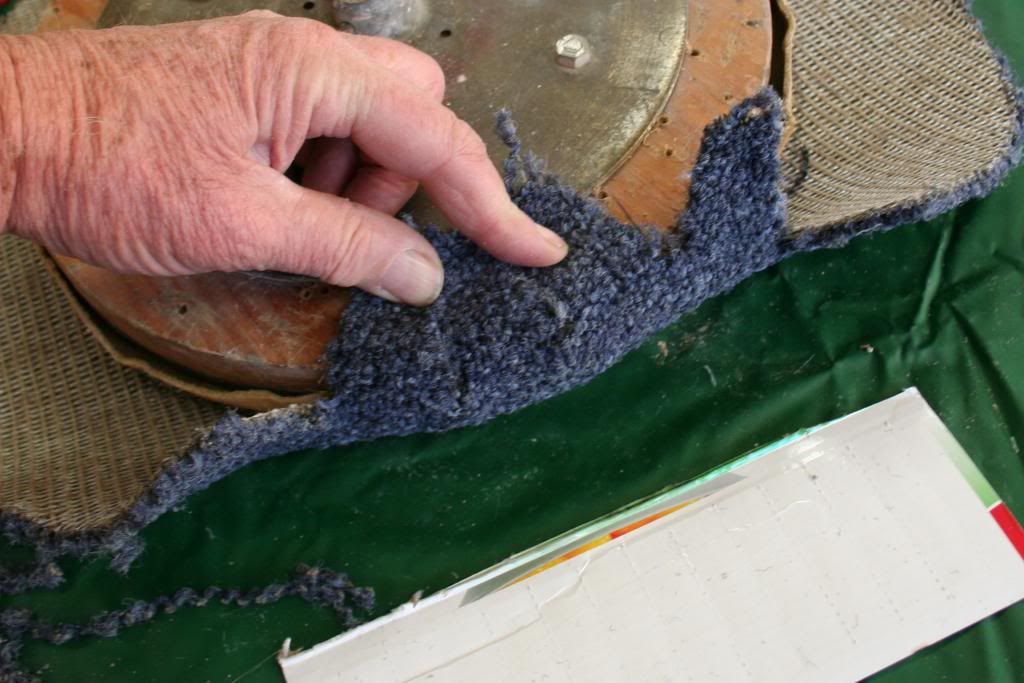
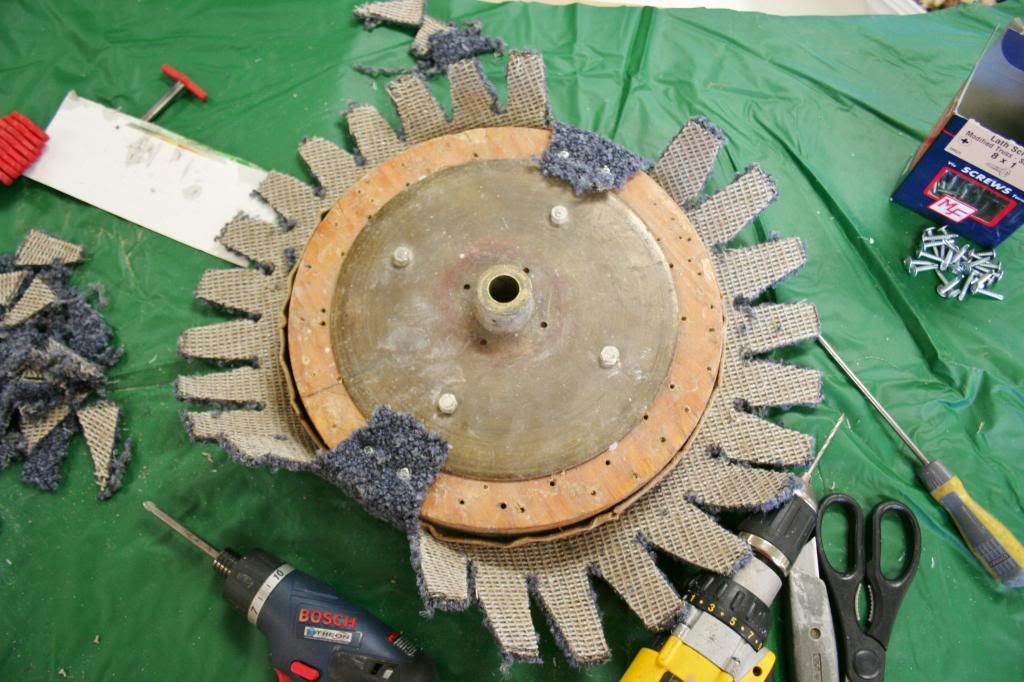
I do two tabs and then go to the opposite side so that the wheel doesn't slip over when I'm working on it.
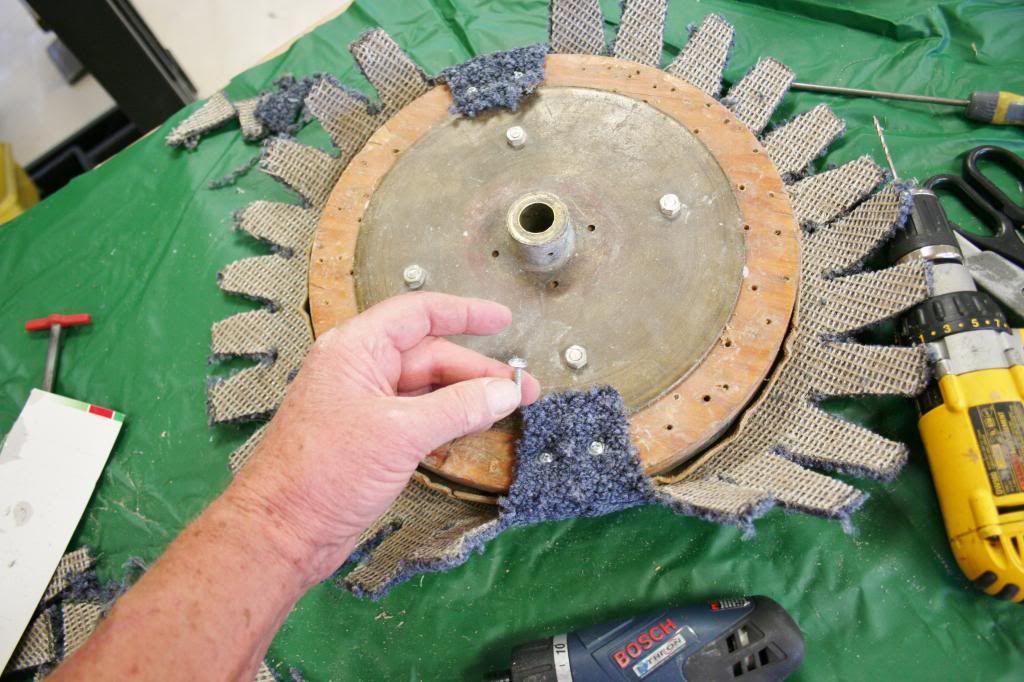
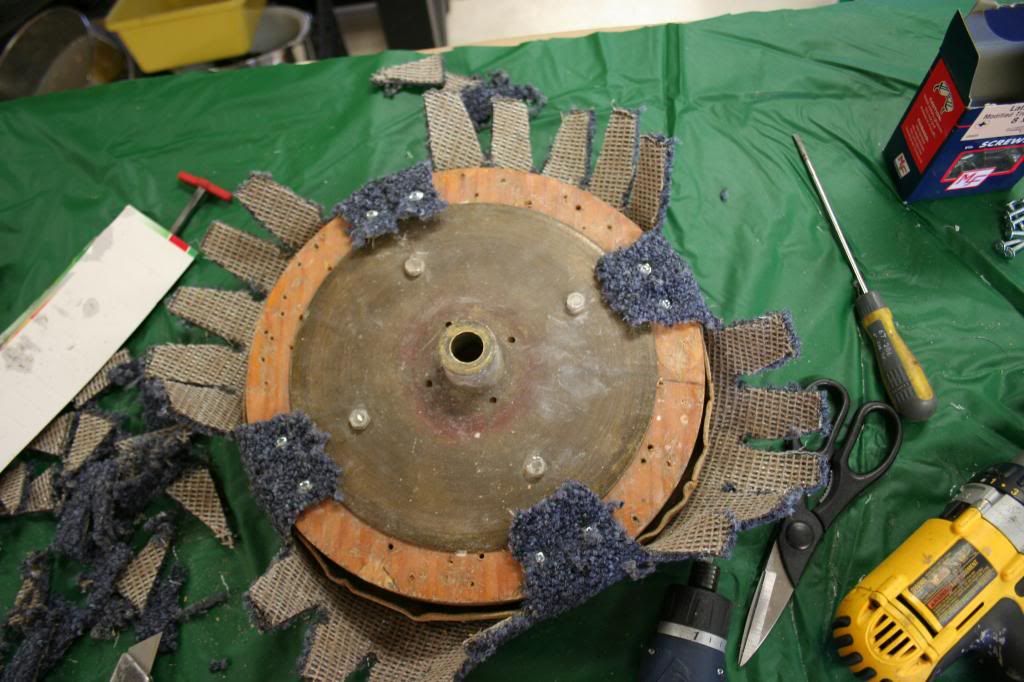
Front view of the completed wheel
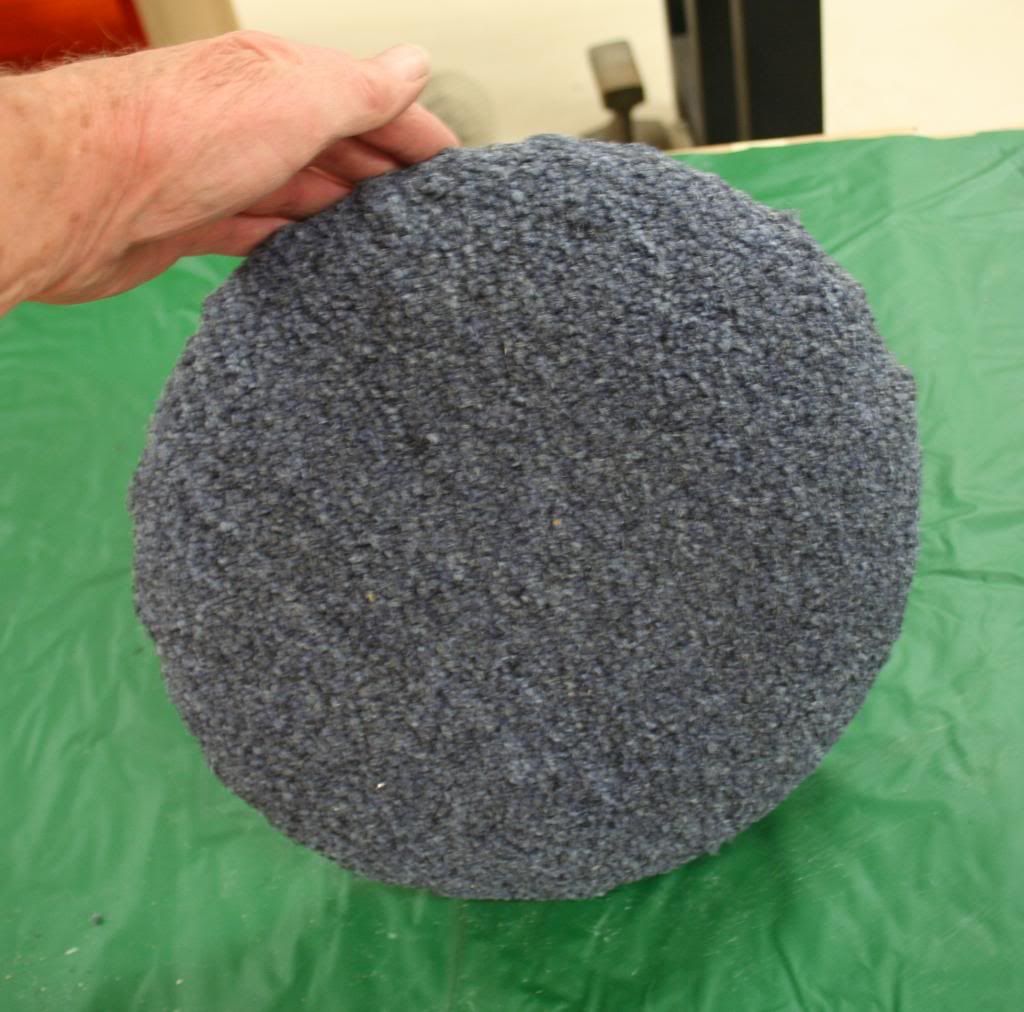
Side views.
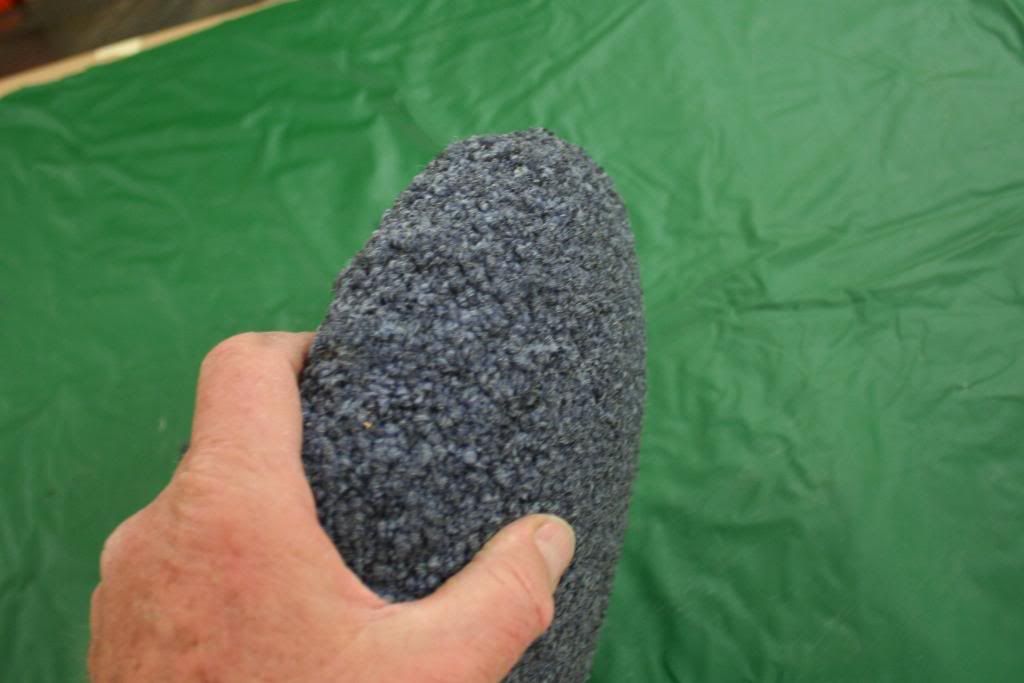
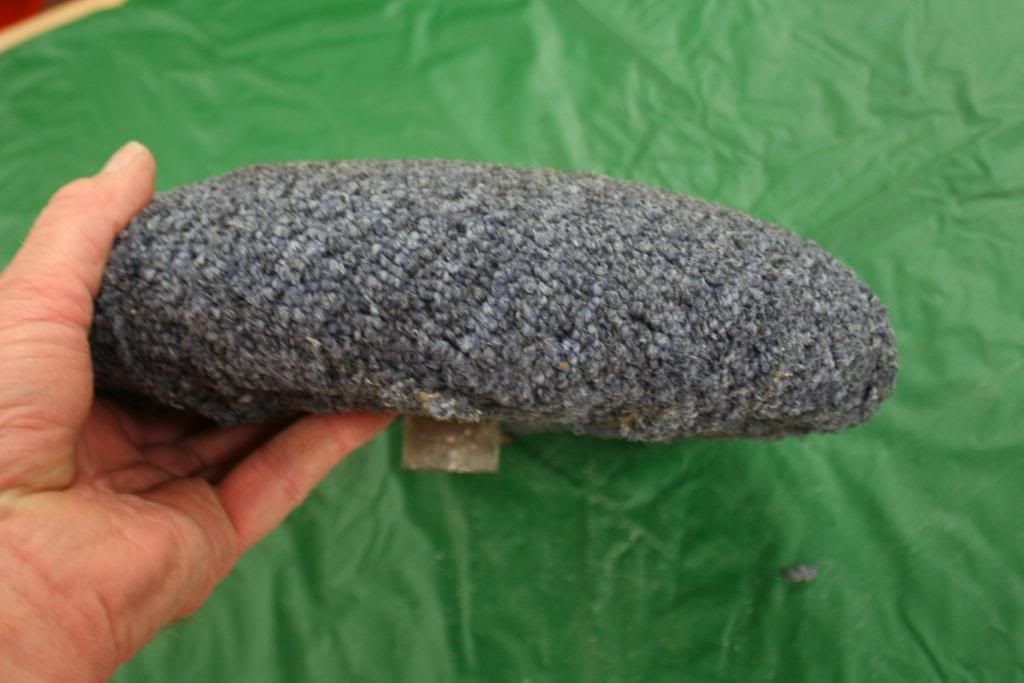
As you may have noticed the wheel has a significant dome in the middle and rounded outer edges. I made it this way so I can readily reach the center of the large cabs (or slabs) and the rounded outer edge allows me to polish the inner curves on a concave sided freeform cab. Here is a photo of it mounted on my (messy) machine.
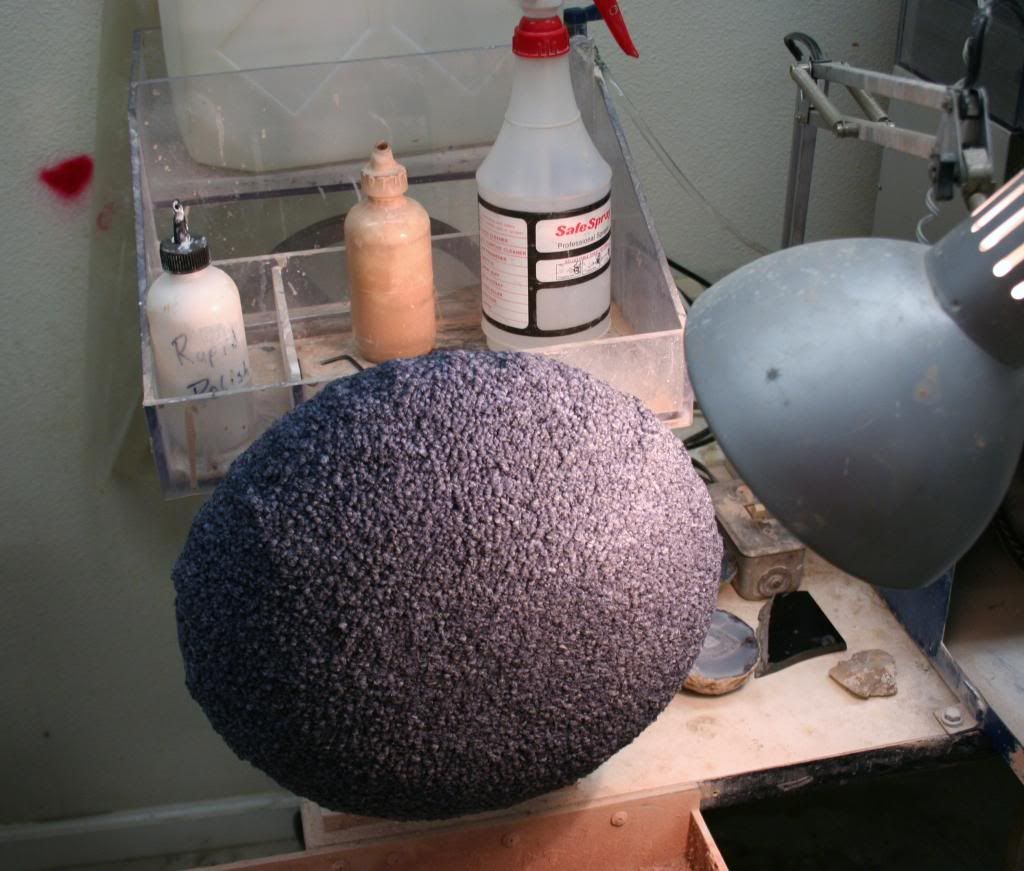
The wheel turns at about 275 rpm and I use cerium oxide for a polish. By using carpet for the cover I can get a significant amount of polish embedded in the knap as well as it holding considerable moisture. This allows me to polish a lot longer before needing to add water or polishing compound.
Sorry if I bored you with so much detail.
Bob