|
Post by holajonathan on Oct 11, 2021 0:33:43 GMT -5
rockpickerforever I get your point about a willful failure to improve despite years of "experience." I'm not in a position to critique anyone else's cabs, but it's a common phenomenon throughout life. My way of trying become good at anything is to start by copying people who have truly mastered the task at hand ( rockjunquie fits the bill!). At this point, I don't see any need to figure out my own way of doing things. First I need to be able to produce good results using methods that others have proven to work well. And only at then, I might try experimenting with my own way of doing things. Some people decide too early on that they prefer their own ways, without ever mastering the proven fundamentals. And poor fundamentals don't produce good results just because you apply them for many years.
|
|
|
Post by Starguy on Oct 11, 2021 1:50:28 GMT -5
holajonathan Do you mark your girdles? I always use a sharpened aluminum rod to mark my girdle thickness. After flattening the bottom of the preform and chamfering it I mark the girdle by laying the aluminum rod on a flat surface and then rotate the preform,(bottom down) around the marker. That marks a girdle line around the circumference of the preform. The mark should be a uniform height above the bottom of the preform. I then grind three bevels on the crown trying to maintain the same angles all the way around the crown being sure not to cut past the girdle line. I check my accuracy by looking at the freshly ground bevel. It should be a similar shape to the original preform. Once the three bevels are cut, I start rocking the preform back and forth to remove the high points from each bevel on the crown. Once the crown is fairly uniform, I go to coarse sanding. I spend quite a bit of time on the coarse sanding stage to make sure the crown is a uniform dome. Then on to fine sanding and polish. This method usually results in a pretty flat dome, with a uniform girdle. I use my finger tips to check the consistency of the dome as much as I use my eyes. The biggest trick is to never grind beyond the girdle line on the circumference. It works pretty good on rounds, ovals and freeforms. Go light and slow on finer points of free forms as rockjunquie said. You can get rid of the circumference line on fine sanding and/or polishing but it usually results in a nice sharp girdle line. Great question. Sorry about the long, drawn out explanation. I’m sure everyone does it a little differently. Feel free to PM me or ask questions in this thread if something I described isn’t clear. I remember struggling with well defined girdles and uniform domes. Here’s a picture of an oval preform with the circumference girdle line. In this case, the dome would be on the side held by my thumb. 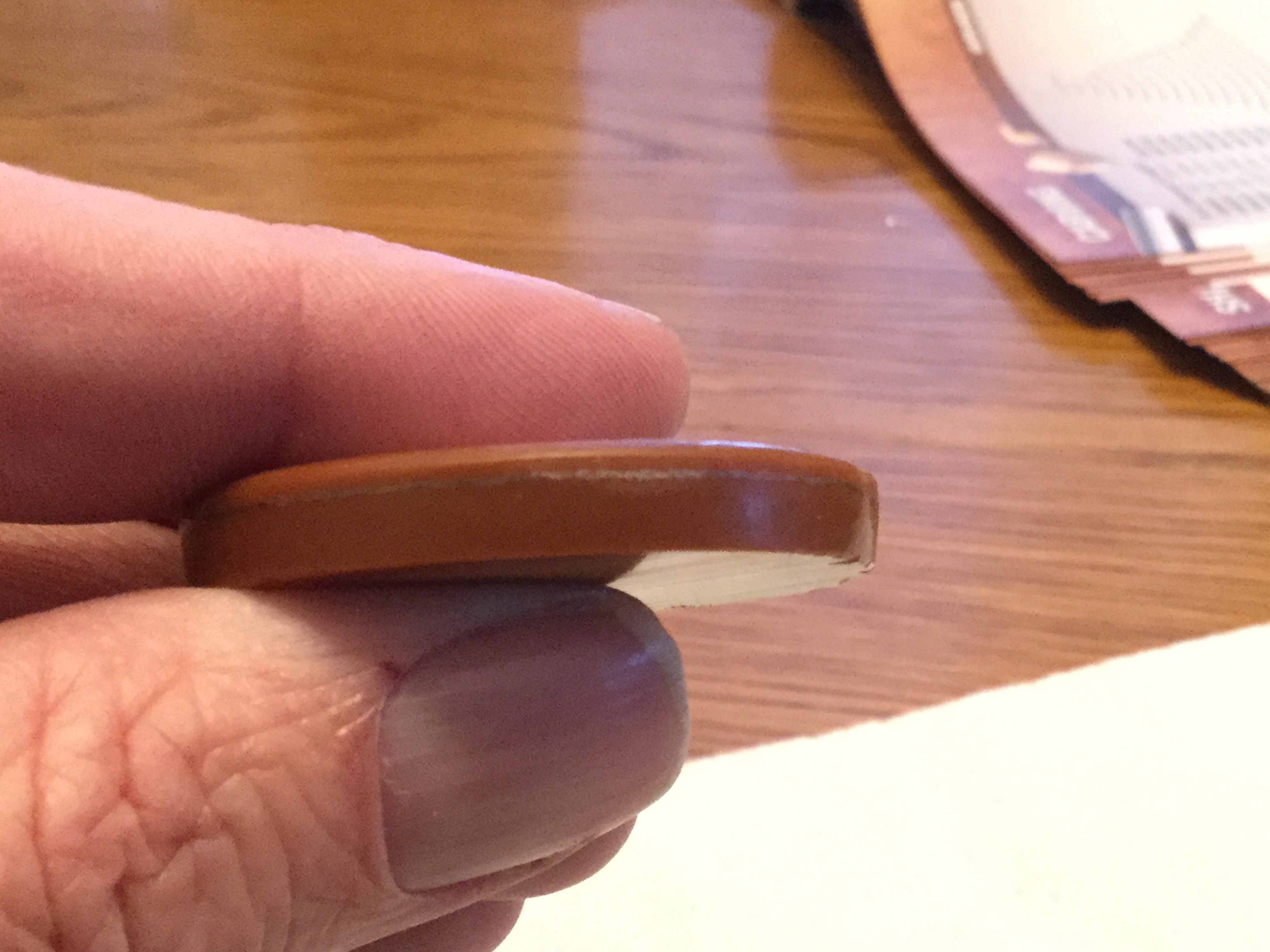 I’m looking forward to seeing some of your results. sincerely, Brent.
|
|
|
Post by Rockoonz on Oct 11, 2021 9:24:17 GMT -5
rockpickerforeverHere is one of those rare occasions that I don't entirely agree with you. The American Federation of Mineralogical Societies conducts competitive cab contests with many categories and a point system, judged by people who have to get many hours of training. In order to enter these you need 40-50 cabs for your display in a 4' display case you'll see in many club shows. One day I still intend to enter a display in a "mini cab", which is a contest the NW Federation does unofficially for first time competitors and only requires 4 cabs, Tommy if I recall, tried a "winner take all" contest with closer to that AFMS style strict judging, and it didn't really take off. The RTH contest is strictly peoples choice, so it's up to us to set the criteria we use to judge. It is all inclusive, so a retired guy like me with no job and a literal boatload if machines to use in my creation will put something in alongside someone with a dremel and a tumbler who lives in an apartment somewhere and works one or more full time jobs to make rent and eat, and may have a partner or spouse who isn't exactly supportive like Elizabeth is for me. For that person getting better at it is painfully slow, like it was for me with 3 kids still in the house, a job and cottage industry that had me at about 60 hours a week, and no budget for tools and no network to find deals on used tools. Also, in the real world I'm finding that more non traditional focal beads and freeforms get a lot more attention than a boring oval cab, thats why we have preferred art shows and bazaars over trying to sell to cheap ass rock snobs at rock and gem shows.
|
|
|
Post by rockpickerforever on Oct 11, 2021 9:42:25 GMT -5
Rockoonz I hear you, Lee. For me, it was not the fact that some people had less to work with - less equipment, less room, less spousal support, less time. It was that they did not want to even attempt to make a cab as they were conceived. Did not even know there was a set descriptionn of a cab. I guess they just don't like rules, will just do what they please.
|
|
|
Post by victor1941 on Oct 11, 2021 10:53:29 GMT -5
Rockpickerforever, you brought up some interesting points about what is needed when rules are used for judging cabs. I use a 60 grit flat lap for my initial shaping and then finish the cabs in a UV-18 vibe for all remaining steps. This method produces a different (more rounded) girdle when compared to a wheel finished cab. By the way, your Brenda plume finished extremely well with this method but I assume if a contest required a crisp girdle I would need to recut and polish the edge to meet the rules or points would be deducted. I cut for artistic enjoyment and luckily don't need to sell so I can make any shape that pleases me and not worry about the rules. It is my opinion that the older members are dying off and the RTH expansion includes many that are tumblers and not too involved in cab making from a competition standpoint.
|
|
|
Post by Rockoonz on Oct 11, 2021 11:06:41 GMT -5
Rockoonz I hear you, Lee. For me, it was not the fact that some people had less to work with - less equipment, less room, less spousal support, less time. It was that they did not want to even attempt to make a cab as they were conceived. Did not even know there was a set descriptionn of a cab. I guess they just don't like rules, will just do what they please. I still want them to participate, and I've seen that most are open to advice. Ultimately if it ever stops being fun I'll stop doing it anyway, I think we agree there. Art and creativity tends to transcend rules. But I do hear what you're saying.
|
|
|
Post by rockjunquie on Oct 11, 2021 11:10:01 GMT -5
This conversation comes up now and again. I think it's important to remember that it is for fun and the majority of members wanted to include non traditional cabs.
|
|
|
Post by Rockoonz on Oct 11, 2021 11:13:24 GMT -5
Rockpickerforever, you brought up some interesting points about what is needed when rules are used for judging cabs. I use a 60 grit flat lap for my initial shaping and then finish the cabs in a UV-18 vibe for all remaining steps. This method produces a different (more rounded) girdle when compared to a wheel finished cab. By the way, your Brenda plume finished extremely well with this method but I assume if a contest required a crisp girdle I would need to recut and polish the edge to meet the rules or points would be deducted. I cut for artistic enjoyment and luckily don't need to sell so I can make any shape that pleases me and not worry about the rules. It is my opinion that the older members are dying off and the RTH expansion includes many that are tumblers and not too involved in cab making from a competition standpoint. To retain as crisp as possible edge in a vibe tumble you might get a 180 grit lap to do your shaping and start with graded 400 in the vibe, aluminum oxide if under about mohs5.5 in hardness, and definitely AO the rest of the way through, with soft filler all the way through. You'll get a lot less rounding, Elizabeth does that with her earrings.
|
|
|
Post by rockpickerforever on Oct 11, 2021 12:30:57 GMT -5
Rockpickerforever, you brought up some interesting points about what is needed when rules are used for judging cabs. I use a 60 grit flat lap for my initial shaping and then finish the cabs in a UV-18 vibe for all remaining steps. This method produces a different (more rounded) girdle when compared to a wheel finished cab. By the way, your Brenda plume finished extremely well with this method but I assume if a contest required a crisp girdle I would need to recut and polish the edge to meet the rules or points would be deducted. I cut for artistic enjoyment and luckily don't need to sell so I can make any shape that pleases me and not worry about the rules. It is my opinion that the older members are dying off and the RTH expansion includes many that are tumblers and not too involved in cab making from a competition standpoint. Victor, glad to hear the Brenda material that you won worked up so well. I don't care what machines you use, flat lap, genie, tumblers, dremels, whatever you have, whatever works for you. I feel some here may think I am being hard on... let's see, how shall I say it... younger, poorer people, that maybe don't have room or the resources for this hobby, or are just getting started down this slippery slope (aka, rabbit hole, lol)? There have been many folks that started out on a low budget, using inexpensive tools, or even making their own machines, then as time and money allowed, moved upward with better machines and better skills. And some are still doing it how they started. I will admit, I have a hypercritical eye: surface scratches, internal cracks, uneven radii or irregular bends, just don't sit right with me. But hey, if you aren't looking for perfection, then you have certainly achieved that. What mostly bothers me, is for instance, when I take the time to make a nice, well-proportioned low dome on a hard stone like agate, while someone else cuts a rectangle out a slab, rounds the edges over, and polishes it (or tumbles it). The two just cannot be compared. Not talking about the work you put into your cabs, victor1941. I know you put in the work.
|
|
|
Post by holajonathan on Oct 11, 2021 12:42:42 GMT -5
holajonathan Do you mark your girdles? I always use a sharpened aluminum rod to mark my girdle thickness. After flattening the bottom of the preform and chamfering it I mark the girdle by laying the aluminum rod on a flat surface and then rotate the preform,(bottom down) around the marker. That marks a girdle line around the circumference of the preform. The mark should be a uniform height above the bottom of the preform. I then grind three bevels on the crown trying to maintain the same angles all the way around the crown being sure not to cut past the girdle line. I check my accuracy by looking at the freshly ground bevel. It should be a similar shape to the original preform. Once the three bevels are cut, I start rocking the preform back and forth to remove the high points from each bevel on the crown. Once the crown is fairly uniform, I go to coarse sanding. I spend quite a bit of time on the coarse sanding stage to make sure the crown is a uniform dome. Then on to fine sanding and polish. This method usually results in a pretty flat dome, with a uniform girdle. I use my finger tips to check the consistency of the dome as much as I use my eyes. The biggest trick is to never grind beyond the girdle line on the circumference. It works pretty good on rounds, ovals and freeforms. Go light and slow on finer points of free forms as rockjunquie said. You can get rid of the circumference line on fine sanding and/or polishing but it usually results in a nice sharp girdle line. Great question. Sorry about the long, drawn out explanation. I’m sure everyone does it a little differently. Feel free to PM me or ask questions in this thread if something I described isn’t clear. I remember struggling with well defined girdles and uniform domes. Here’s a picture of an oval preform with the circumference girdle line. In this case, the dome would be on the side held by my thumb. 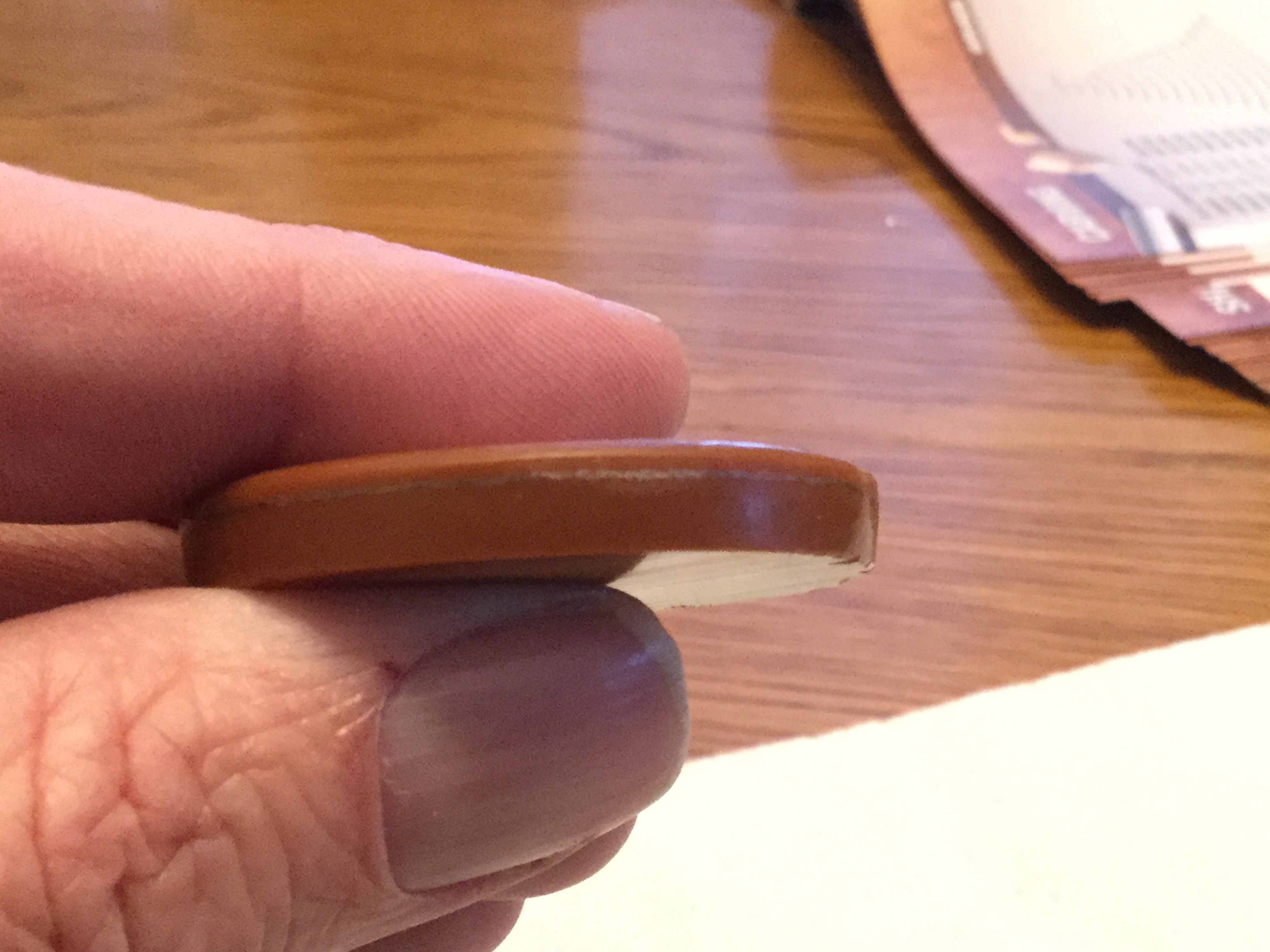 I’m looking forward to seeing some of your results. sincerely, Brent. Thank you, Brent. Your explanation is similar to what I have received from others, but I appreciate receiving it again in a slightly different way. I do mark a girldle line, and with ovals, tear drops, and similar shapes, I have no problem staying above it. Cabs with long flat sides, inside curves, and sharp points, are what have been throwing me for a loop. When it came to cabs with long points, for example, I had to choose among 3 options: (1) let the girlde get shorter at points (to allow the dome to continue to fall to the end of the point), (2) leave something of a ridge along the top of the point, which allows the girldle to stay consistent; or (3) have a flat spot in the top of the cab running in the direction of the point, if that makes sense. rockjunquie and other seem to use option #2, as well-illustrated in the photos that she posted for me in a separate thread. You said "I check my accuracy by looking at the freshly ground bevel. It should be a similar shape to the original preform." I think you mentioned that to me before, and I have come to love doing that. Assuming the angle of the bevel is consistent around the cab, this is a fail proof method. If you make cabs with geometric shapes, flat sides, or long points, I would love to see a few photos when you get a chance. I may create a thread asking the entire community to share such photos so that I and others may learn from them. I appreciate your willingness to help guide me in the right direction. I'll continue to post photos of my progress.
|
|
|
Post by rockjunquie on Oct 11, 2021 12:48:58 GMT -5
holajonathan The only cab that had ridges at the corners was the first one. If any others looked that way, it was reflections. Just wanted to make that clear. It is generally preferable to NOT leave a ridge.
|
|
|
Post by victor1941 on Oct 11, 2021 14:09:02 GMT -5
Rockoonz, I do have a full set of flat laps but usually make cabs by the pounds and the 60 grit will leave quartz shock and/or scratches in my material. This usually requires two cycles in the 100/220 SiC grit and this is where the rounding takes place. I agree with what you said but don't make cabs one at a time from start to finish. When a contest opens I check to see if I have any leftover material to make a few cabs for entry. I am nearing the end of the material I purchased or collected many years ago and wanted to process as much as possible while I still have good motor skills.
|
|
|
Post by victor1941 on Oct 11, 2021 14:23:04 GMT -5
Rockpickerforever, I still remember your large Brazilian cab from a few years and do understand the work that went into such a stunning piece! It is the same reward that I have when I did find and cut a beautiful Marfa Bouquet plume in hard agate that lets me make a very low dome or flat top.
|
|