|
Post by rockjunquie on Jan 8, 2014 14:06:08 GMT -5
The first part of my first project went very well. Much easier than I had expected it to. I got some great tips here, too, for my next one. The bail part turned into a nightmare. I decided to use this template from Cooltools to make a simple bail. What you get is something like you see below. I ended up cutting with shears because my bench pin is still in the mail. I made several because I messed up several.  I tried a variety of ways to solder this. I photographed the last tries today after several failures yesterday. First let me say that when you are making a bezel, you really have to see things a new way. Luckily, I am used to it from wire wrapping. But, even I, at first had trouble seeing that the bail couldn't be at a 90 degree angle to fit flush with the bezel wire. In other words- the areas to be soldered were NOT 90 degree angles, although at first your brain thinks they are. I had to put an ever so slight concave curve in the bail end with a file. I then had to decide where to place the bail in relation to the bezel cup. I decided to solder the bail midway on the bezel. I needed to lift the bail up to solder and tried a stainless steel wire to do it. It didn't work. I had to file solder off the bezel. Even though I knew the copper bail needed more heat, the thinner silver still got hotter and the solder flowed up the bezel.  Next I tried using my new solder station that I got from DH for Christmas. Looks like a good fit.  However, I could NOT get the solder to flow no matter what! It was easy solder, too. I think the clamps were too much of a heat sink, so I went back to the charcoal.  The 3rd hand lifted the bail up enough and I thought everything looked good. At first, I thought the solder wouldn't flow again, but I quickly ran some heat under the join and it ran beautifully.  But, look what happened. I don't know if I moved it, didn't line it up right to begin with, didn't have enough solder or maybe the fit was just off, but I was left with a gap.  Here's the back.  As you can see, I was soldering the bail closed AND soldering the bail to the top. A lot of solder ran up the copper, but it is soldered shut and the bail does seem secure. I thought about trying to use extra easy solder to solder the gap, but I don't want to distort the bezel by doing it. I would have to form the metals closer together. Since this is my first project, I have decided to let it go. My focus will be on finishing when my order comes in. I got some finishing paper. I will glue some to Popsicle sticks (Thanks Pat). I got those radial sanding wheels, too. While I am here.... here's a shot of a great cheap tool. It's a cheap punch that doubles as a nice bail mandrel. It came in a set of three from Wally world. They come in handy.  I have a feeling that finishing will be the hardest part...... Thanks for reading- all comments welcome. 
|
|
|
Post by 1dave on Jan 8, 2014 14:55:32 GMT -5
I'm wondering how strong the solder joint is attached to the middle of the bezel. I used to solder lots of transistors to circuit boards. Those big heavy duty guys would vibrate and the soldered legs would break off.
I like a bale shaped like a #9 with a straight leg soldered to the back of the piece, and just the bottom edge of the bezel so there is no problem forming it to the stone.
|
|
|
Post by rockjunquie on Jan 8, 2014 15:07:53 GMT -5
I'm wondering how strong the solder joint is attached to the middle of the bezel. I used to solder lots of transistors to circuit boards. Those big heavy duty guys would vibrate and the soldered legs would break off. I like a bale shaped like a #9 with a straight leg soldered to the back of the piece, and just the bottom edge of the bezel so there is no problem forming it to the stone. I'm wondering that, too. It seems pretty solid. If I were doing a project to sell, I might not do it this way. But, this is a learning experience.
|
|
|
Post by 1dave on Jan 8, 2014 15:19:01 GMT -5
And that may well be the way that works best for you and many others! Nothing is "written in stone."
|
|
|
Post by pghram on Jan 8, 2014 17:26:24 GMT -5
Thanks, I learned something else from your project, that they make a template for bails.
Rich
|
|
|
Post by Pat on Jan 8, 2014 19:29:45 GMT -5
Onward!
Typically, we solder the bail to the back plate, not the bezel. Back plate is of thicker and stronger silver than the bezel, so the danger of the bezel melting is lessened. This also allows you easier access to the bezel to burnish it against your stone. You're doing great!
I wonder why your new soldering station didn't give the expected result. I just received a new soldering station, too. Did you hold the torch under the piece so the solder would flow to the heat? Did you warm up the heat sinking handles first?
Thanks for posting all this. It's very helpful.
|
|
|
Post by rockjunquie on Jan 8, 2014 21:03:00 GMT -5
Onward! Typically, we solder the bail to the back plate, not the bezel. Back plate is of thicker and stronger silver than the bezel, so the danger of the bezel melting is lessened. This also allows you easier access to the bezel to burnish it against your stone. You're doing great! I wonder why your new soldering station didn't give the expected result. I just received a new soldering station, too. Did you hold the torch under the piece so the solder would flow to the heat? Did you warm up the heat sinking handles first? Thanks for posting all this. It's very helpful. I feel kinda dumb now. I guess I'll be having a hard time with the setting.  No, I didn't heat the clamps farther down than the ends. Yes, I did heat under... and over... and sideways... and back again. No go. I bet it was the handles. It was my first use of it. I'll know better next time. I do like it a lot, though. It holds well and is very articulated.
|
|
|
Post by Pat on Jan 8, 2014 21:10:57 GMT -5
Tela, this is good information for me re the soldering station. The only thing I've done on mine is make one silver ball! I think the station is going to be great! I think you will find a way to make the bezel work just fine.
|
|
|
Post by connrock on Jan 9, 2014 10:19:34 GMT -5
You're doing great and learning a lot as you go along! As you're learning,some thought has to go into designing a piece and not only how pretty it looks. A LOT of prep work has to be done before the soldering and setting up the pieces to be soldered takes a long time....especially when your first learning. The tools you have to do your set-up work will more then likely vary from piece to piece so 1 set-up toll won't work for everything you solder. Sometimes your imagination is your best friend and a common nail or screw,etc can be used as a heat sink or to hold a piece in the right position for soldering. "Binding Wire" can be useful in some set-ups and you can even make a "bed" with it to lay your pieces on to be soldered,,,,, 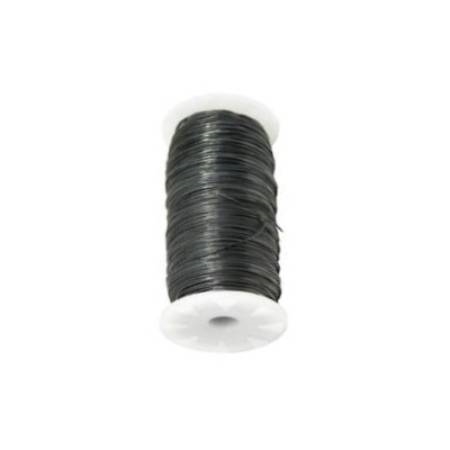 It comes in different guages and is inexpensive to buy. Before applying any heat to your work,,,,look at the entire set-up and the pieces to be soldered.Try to think of them as being 1 "entity",,,,,,what is thicker and needs more heat,,,,,what is thinner and will melt on me fast,,,,,will my heat sinks need to be preheated,,,etc,etc,etc!Form a plan in your mind before you attack! Fitting pieces improperly is probably the most common mistake we all make when first learning how to silver solder.We tend to think we're doing something wrong during the actual soldering process but our problem was created long before we even lit the torch! Fitting the pieces can be very frustrating but it HAS to be done right or no amount of soldering experience will help to make a good soldered joint.If you have ANY gap,,,you WILL have a bad soldered joint! At times it's almost impossible to get a bezel wire to lay flat on a back plate!No matter if we try to "bend" the bezel wire or make the back plate flat,,the 2 pieces just will not fit without a gap or gaps! There are a few ways of remedying this problem but what I do is,,,, when I see the solder flow at a point where there is no gap,,,I push ever so lightly down on the part(s) where I know there is a gap with a solder pick.When I see the solder go all around the bezel wire/back,,I take to heat away. Things happen FAST so again you have to think this through before you put the heat to the pieces. Another thing about soldering is the what type of soldering block you're using.Each type will change the way your pieces and solder act. Example,,,,a fire brick will cause you to need a lot more heat to get everything hot enough ,,,yet a charcoal block will reflect the heat much faster causing your pieces to heat up much faster. "Suspended" pieces will heat up even faster. Going from one type of torch/gas to another is a whole new learning experience too!It can be like getting into someone elses car at night and trying to find the windshield wiper switch when it start to rain,,,,in traffic! LOL connrock
|
|
jamesp
Cave Dweller
Member since October 2012
Posts: 36,583
|
Post by jamesp on Jan 9, 2014 10:34:36 GMT -5
Watching solderers from a distance. Learning.
Lurking....I love putting structural iron up but soldering will humble you.
Soldering.....ugggg. The key to humility.
|
|
|
Post by rockjunquie on Jan 9, 2014 10:39:03 GMT -5
connrock - Good things to think about.  I used to do borosilicate lampworking/glassblowing and used a big oxy/propane torch for it. A veriflow/national 3a. I'm used to big fire. But, since I don't have a proper place to do what I am doing, the small micro torch has been serving me. I hope to step up to a Smith's little torch oxy/propane sometime in the future. I know it will be a big adjustment, just as using the micro torch has been. I hear ya about the planning. In doing my more complicated wire work, the design and planning stage took longer than the act of making it.
|
|
jamesp
Cave Dweller
Member since October 2012
Posts: 36,583
|
Post by jamesp on Jan 9, 2014 11:42:58 GMT -5
I have a big oxy acetylene welders rig Tela. I can attach a tiny jeweler's torch to it.
It has the smallest welder's torch that is made. But it is way bigger than the jewelers torch.
Point being that when i need really hot i can test the waters with oxy/acetylene.
Sometimes it takes more heat than i ever imagined or i want quick heat for hard to hold operations.
I have talked to silversmiths that like the high heat level of oxy/acetylene.
Would like to hear opinions on oxy/acetylene sometime. (on a another thread perhaps as i am going in hi-jack subject)
But it seems appropriate for this discussion.
|
|
|
Post by 1dave on Jan 9, 2014 12:56:32 GMT -5
connrock You are a national treasure for your insight, experience sharing, and telling it like it is! I worked on 5 different construction jobs at Geneva Steel that used to be just south of Orem Utah. I got years of watching the skills of those men doing astonishing things on a daily basis. Now all torn down, the men scattered, the skills ignored. What a waste!
|
|
|
Post by connrock on Jan 10, 2014 7:20:06 GMT -5
James,,,, I think the discussion of which torch/gas is best can go on forever.To me,,,it's like asking a person which is better ,,Coke or Pepsi!Some like Coke and others insist on Pepsi! My experience,,, I wanted to learn to silver solder sterling silver.I read and read and then read more about which torch/gas is better.I opted on Smith's Little torch with oxy/acet.My first experience was NOT a good one and I was pretty disgusted with the whole thing.My wife knew my dilemma and asked a silversmith where she buys some of her jewelery if he would help me.He agreed and we went to see him.I was shocked to see that his main torch was a plumbers B tank with acetylene and air.He used a #3 tip and did some outstanding work!I told him I had the Little Torch and he (Richard) told me to get rid of it and get whet he had! Well,,,I had 3 B tanks,regulators and a ton of tips already so when I got home I had at it with one of my plumbers torches and a #3 tip!The flame seemed HUGE and totally uncontrollable but I had seen Richard use it with ease so I kept at it.I tried for 3 solid 10-12 hour days to use that rig and got even more frustrated then I was using the Little Torch! I went back to using the Little Torch and still do today. Coke or Pepsi?  ? Here's Richards web site,,,take a look at what he does with his plumbers torch,,,, www.littlesilvershop.com/default.aspThe rig you have is way too big for jewelery but I'll bet there's someone,somewhere who can use it and do a great job too! I'm NOT saying it's the right rig or that you should try it ,,,I'm just saying it can probably be done. Your regulators are too big too.Trying to regulate the oxygen . I mainly use a #3 tip in my Little Torch(oxy/acet)and trying to set the oxy regulator to 3-5 PSI when the first increment on the guage is 25PSI is a trip! Before you cuss yourself out for not being able to silver solder,,,,get a rig that's a tad smaller then what you have now!LOL connrock
|
|
|
Post by connrock on Jan 10, 2014 7:40:17 GMT -5
Dave,,, I try to tell it like I see it and in todays society where "everyone gets a trophy" I have to bight my (big) tongue! LOL It's sometimes difficult to convey what we want to say using a key board and 1 word in the wrong place can get a fella in a LOT of trouble.  I tried to help someone years ago with a rock tumbling problem and got a VERY nasty PM.I was very upset and quit this group for a while but came back again later.Some people just don't take constructive criticism well and after thinking about it have decided that it's their loss as I have NEVER tried to hurt anyone but rater try my VERY best to help. I've made a L O T of mistakes and have had a L O T of people who helped me to get to where I know the little that I do know. I spend a lot of time on this site,not only because I learn something every day,but because of the people who are here and are willing to share their knowledge with others who need their help. They ARE the National Treasures,,,NOT me!
|
|
|
Post by Donnie's Rocky Treasures on Jan 10, 2014 9:43:15 GMT -5
I am soooooo loving these posts! So much good information & support!
|
|
|
Post by 1dave on Jan 10, 2014 10:16:06 GMT -5
connrock Being real matters to me! Thanks for sharing Richard Parker and the Little Silver Shop with us. I LOVE those "button bracelets" he makes! 
|
|
|
Post by radio on Jan 10, 2014 10:42:24 GMT -5
For bezel to get a good join it needs to be touching the backing evenly all around. This can be accomplished by leaving the stone in the soldered and shaped bezel and laying them on a large file and pushing it back and forth carefully with your fingers spread over the cab/bezel to cut down any high spots, and especially at the bezel join. While connrock's method of pushing the bezel down while soldering is great for experienced smiths, it often results in disaster for beginners as the join of the bezel often comes unsoldered and the whole thing has to be redone or scrapped. Not trying to sound like a know it all, or refute anyone else's advice. Just sharing what I have found with many beginning metal smiths
|
|
|
Post by rockjunquie on Jan 10, 2014 11:52:51 GMT -5
I found out the hard way how hard it is to get two perfect 90 degree angles to join the bezel wire. I think my best advice from very limited experience would be to get a tool that allows for a perfect cut. I found just the tool and ordered one after seeing Bill Fretz use it in a video.  This is the cheapest one I could find that wasn't junk. (Rio had 2 about 150.00 ea) I haven't gotten it, yet. I'm hoping it is decent. www.amazon.com/gp/product/B0084H6TWO It can be used on strip and wire as well as tube. I intend to take the gauge off. If the bezel is soldered with 90 degree ends then one shouldn't have to sand the bottom.
|
|
Tom
fully equipped rock polisher
 
My dad Tom suddenly passed away yesterday, Just wanted his "rock" family to know.
Member since January 2013
Posts: 1,557
|
Post by Tom on Jan 10, 2014 13:40:42 GMT -5
Tela I thing that alot of your issues are from using the micro torch. I have seen some pretty cool things done with them but I think when you are in a situation where you are sinking he heat away faster than the torch will provide (like with your solder station) you would do better with a bigger (hotter) torch.
I use Smiths Acetylene air torch and have 5 tips, I normally use only the 2/0 and the 1/0 tip. Smiths little torch acet/ox is hotter but you need more tanks, more regulators, more hoses. I can pump out the heat with my system enough to destroy things:) (from experience)
Our club has the acet/ox unit but we are going to get an acet/air torch.
a club member that has been doing this for 35 plus years has both torches at home, he NEVER uses the acet/ox unit.
It would be really nice if you could try out a couple different options before buying a torch (and I know you will you said so:))
NOTE: I am not saying the acet/air unit is better than the acet/ox unit, just saying I prefer it and alot of others do to, its going to be a matter of personal preference.
I am almost positive if people really really get into this they will graduate from the micro torches. Tom's humble opinion!
Have a super day
|
|