rockbrain
Cave Dweller
Member since January 2022
Posts: 3,172
Member is Online
|
Post by rockbrain on Apr 7, 2024 12:40:37 GMT -5
I have a couple of small chunks of opal. I'm going to try and work on the wheels. I believe it's Ethiopian since I could afford it! I know some of the opals can be heat sensitive and soak up water. Is it okay to dop this on my dopping station with green wax? How about putting it in the freezer afterwards to release it? 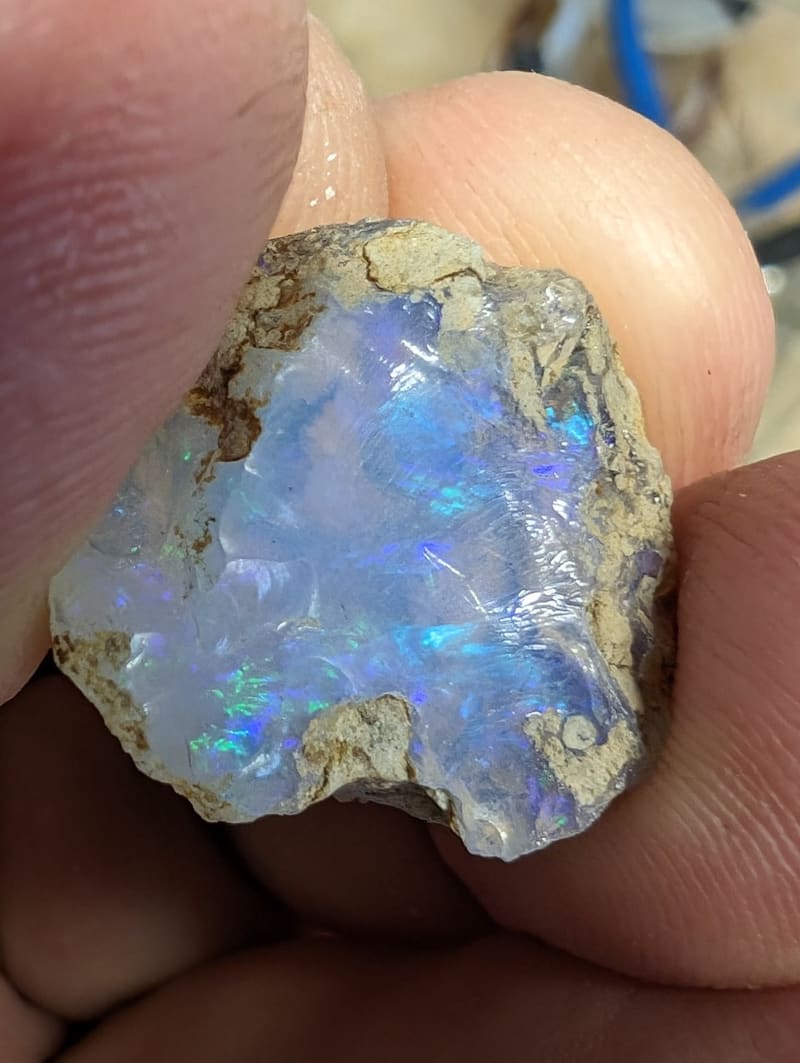 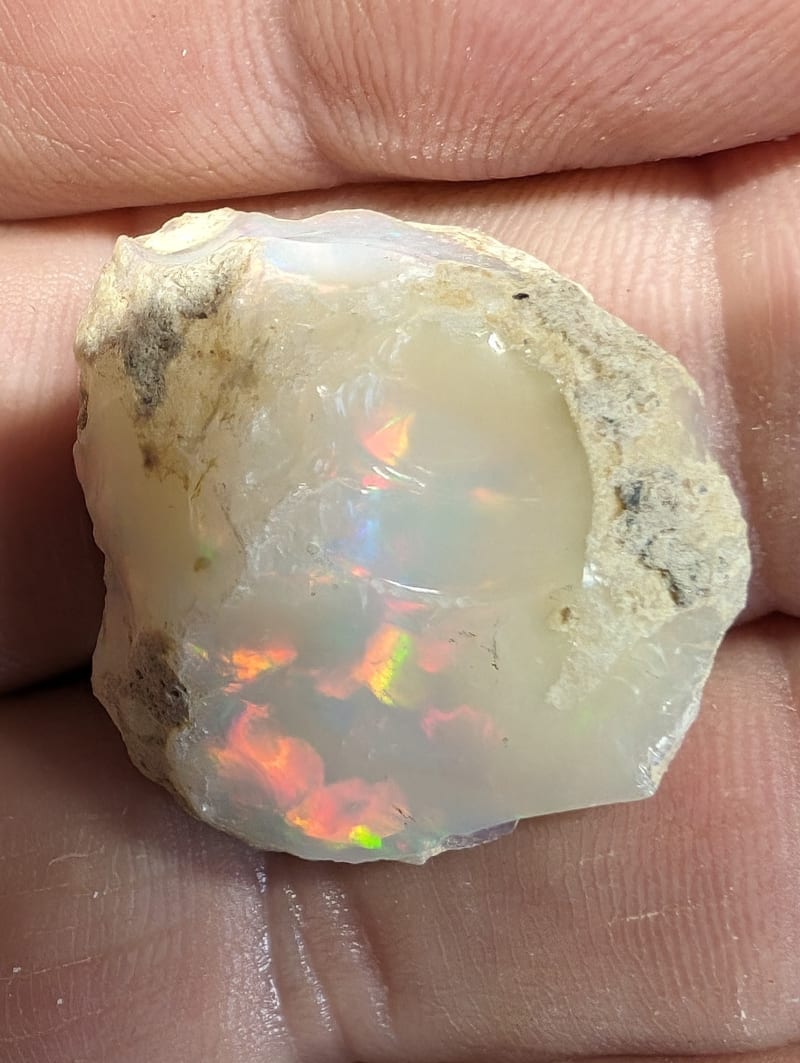
|
|
|
Post by Pat on Apr 7, 2024 12:54:28 GMT -5
|
|
goldfinder
Cave Dweller
Member since December 2020
Posts: 273
|
Post by goldfinder on Apr 7, 2024 13:36:33 GMT -5
Hey Gary, I recently went through a bit of trial and error with Ethiopian opal. Ethiopian opal is what is called "Hydrophane" and absorbs water. I first tried dopping a piece with dop wax and an alcohol lamp flame (how I do for Australian opal) but the opal promptly cracked.
After asking a few Ethiopian dealers, they recommend super glue. So I recently tried a little bit of some Starbond on a nail and it worked great, I just pulled the opal off the nail when it was finished.
One thing to consider is, I've heard that the rapid drying of Ethiopian opals can cause them to craze and crack. So it's recommended to dry them slowly, like after cabbing put it in a Ziploc bag, progressively opening it more over the next week or so. I'm sure others are much more experienced but this worked for the last couple I recently worked.
|
|
|
Post by opalpyrexia on Apr 7, 2024 15:13:13 GMT -5
I've cut only one Ethiopian opal and I didn't so anything different from what I do with Australian or US opal. goldfinder has some good advice regarding the use of superglue dopping. Loctite Super Glue Ultra Gel Control works great. If you have a good gram scale you may be able to determine if the opal is in fact hydrophane. Remove it from water storage, dry it with a towel and weigh it. Now leave it in a warm place for several days and weigh it again. Same weight or has there been a loss? And if drying causes crazing, well, then you wouldn't want to make jewelry with it.
|
|
gemfeller
Cave Dweller
Member since June 2011
Posts: 4,059
|
Post by gemfeller on Apr 7, 2024 15:34:48 GMT -5
rockbrain Yes, it's Ethiopian hydrophane. I cut mostly Aussie opal but have worked with Ethiopian a bit. My first move would be to remove the matrix with a Mizzy heatless wheel using a Foredom. This can be done dry but it generates dust so mask up. Once done you'll be able to see the full shape of the opal and can orient it accordingly. I don't usually dop opal at this stage, preferring to manipulate it manually, grinding slowly with a 220 hard wheel to establish shape. I use minimal water for this because the color may disappear as the opal becomes saturated. I dop Ethiopian opal with Elmer's white glue, which is water soluble, for sanding and polishing. I let it set up overnight for maximum curing to avoid quick water saturation while working it. I remove the stone by soaking in water, then letting the finished stones dry slowly for as long as it takes for the play of color to return. Maybe I've been lucky but none I've cut this way have crazed. I'll be interested to learn the methods others use. Good luck!
|
|
rockbrain
Cave Dweller
Member since January 2022
Posts: 3,172
Member is Online
|
Post by rockbrain on Apr 7, 2024 17:55:26 GMT -5
Hey Gary, I recently went through a bit of trial and error with Ethiopian opal. Ethiopian opal is what is called "Hydrophane" and absorbs water. I first tried dopping a piece with dop wax and an alcohol lamp flame (how I do for Australian opal) but the opal promptly cracked. After asking a few Ethiopian dealers, they recommend super glue. So I recently tried a little bit of some Starbond on a nail and it worked great, I just pulled the opal off the nail when it was finished. One thing to consider is, I've heard that the rapid drying of Ethiopian opals can cause them to craze and crack. So it's recommended to dry them slowly, like after cabbing put it in a Ziploc bag, progressively opening it more over the next week or so. I'm sure others are much more experienced but this worked for the last couple I recently worked. Thanks, definitely won't go the way I was going to. I've cut only one Ethiopian opal and I didn't so anything different from what I do with Australian or US opal. goldfinder has some good advice regarding the use of superglue dopping. Loctite Super Glue Ultra Gel Control works great. If you have a good gram scale you may be able to determine if the opal is in fact hydrophane. Remove it from water storage, dry it with a towel and weigh it. Now leave it in a warm place for several days and weigh it again. Same weight or has there been a loss? And if drying causes crazing, well, then you wouldn't want to make jewelry with it. Thanks! "Remove it from the water storage" They're just in little ziplock bags that they purchased them in. Sounds like I should be doing something different. rockbrain Yes, it's Ethiopian hydrophane. I cut mostly Aussie opal but have worked with Ethiopian a bit. My first move would be to remove the matrix with a Mizzy heatless wheel using a Foredom. This can be done dry but it generates dust so mask up. Once done you'll be able to see the full shape of the opal and can orient it accordingly. I don't usually dop opal at this stage, preferring to manipulate it manually, grinding slowly with a 220 hard wheel to establish shape. I use minimal water for this because the color may disappear as the opal becomes saturated. I dop Ethiopian opal with Elmer's white glue, which is water soluble, for sanding and polishing. I let it set up overnight for maximum curing to avoid quick water saturation while working it. I remove the stone by soaking in water, then letting the finished stones dry slowly for as long as it takes for the play of color to return. Maybe I've been lucky but none I've cut this way have crazed. I'll be interested to learn the methods others use. Good luck! Thanks, I don't know why I didn't think of wood glue. I was using that for dopping for a while. I guess I'll set these aside for a while and order some heatless wheels.
|
|
aGates
has rocks in the head
 
Building a silver studio
Member since January 2021
Posts: 518
|
Post by aGates on Apr 7, 2024 18:06:33 GMT -5
Another thing I've learned with Ethiopian opal AKA Waelo opal is that you must polish the opal all in one sitting from course to finish product. Also that it goes clear as you work it but dries like you originally saw it and also the opal cutters I talked to said you want to polish the back to the same polish as the front and once polished to final stages the rock "seals" and you won't get crazing but if left un polished the water can evaporate out the course area. Some beautiful stones if done correctly. All that said I haven't tackled my specimen yet. A teardrop with a high dome is my goal. I have a flat lap I'll be lapping the back with. And of course nooo oil! rockbrain
|
|
rockbrain
Cave Dweller
Member since January 2022
Posts: 3,172
Member is Online
|
Post by rockbrain on Apr 8, 2024 9:05:00 GMT -5
Another thing I've learned with Ethiopian opal AKA Waelo opal is that you must polish the opal all in one sitting from course to finish product. Also that it goes clear as you work it but dries like you originally saw it and also the opal cutters I talked to said you want to polish the back to the same polish as the front and once polished to final stages the rock "seals" and you won't get crazing but if left un polished the water can evaporate out the course area. Some beautiful stones if done correctly. All that said I haven't tackled my specimen yet. A teardrop with a high dome is my goal. I have a flat lap I'll be lapping the back with. And of course nooo oil! rockbrain That's interesting! I often leave the backs till later but I'll make sure I do these all at once. I'll probably be pretty anxious to see how they turn out anyway and will be doing them by themselves instead of my typical dopping of several at once.
|
|