chaosdsm
starting to spend too much on rocks

Member since April 2024
Posts: 106
|
Post by chaosdsm on Jul 21, 2024 16:16:41 GMT -5
I have a 7inch blade tile saw with a guide fence, but I don't have any way to clamp rocks down and run them through the saw. Don't have any way to buy any other saw till at least next year, probably longer.
Still, I want to cut very thin, consistently flat slabs. I'm looking for 1.2mm to 2.4mm thick slabs for various projects as well as some thicker slabs.
I've thought of 2 potential ways to do this, just wondering if anyone has tried anything like this, or am I even on the right track? ? ? ?
1> Starbond KEG-500, Max Strength, Flexible, Medium Thick, Premium CA Super Glue: Make an initial cut on the rock and use the KEG-500 to adhere it to a block of wood, then just run it through the saw. The Starbond KEG-500 is supposed to have much higher bond strength than regular CA glues, but would it be strong enough to hold for up to 20 or so cuts on a 4" wide rock???
2> Epoxy Pour: Much more expensive, but I could use rectangular silicone molds and pour a 1/4" to 1/2" thick epoxy base (depending on the stiffness of the epoxy) on the bottom of the rock to act as a guide. But I would end up with a thick piece near the end that I would probably still have to superglue to a block of wood
3> OTHER: I'm open to suggestions....
|
|
Mark K
Cave Dweller
Member since April 2012
Posts: 2,733
|
Post by Mark K on Jul 21, 2024 16:28:46 GMT -5
Make your cut, clean the rock up real good. Clean it again. Run it through the dishwasher when the boss isn't home. Use good wood glue to glue it to your PERFECTLY clean wood and clamp it. Leave it longer, by a few days, than you think you need to, then cut your rock. If it does break loose, it probably was not real clean. I assume you are using only water in the saw. Make multiples at a time to save time. Quality control is key.
And get a real saw.
|
|
|
Post by Peruano on Jul 21, 2024 16:32:52 GMT -5
Use standard carpenter wood glue on wood stubs. If the stone is high enough to allow the wood yo be slid on saw table you have on perpendicilr plane . Clamp a guide like a saw fence at approprite distance from blade to standardoze thickness. Watch for bindin but you can do it if you dont crowd you blade by going too fast.
|
|
|
Post by Peruano on Jul 21, 2024 16:34:42 GMT -5
Can you tell I am typing this on a moving Alaskan Marine Highway Ferry?
|
|
|
Post by HankRocks on Jul 21, 2024 19:08:27 GMT -5
Make your cut, clean the rock up real good. Clean it again. Run it through the dishwasher when the boss isn't home. Use good wood glue to glue it to your PERFECTLY clean wood and clamp it. Leave it longer, by a few days, than you think you need to, then cut your rock. If it does break loose, it probably was not real clean. I assume you are using only water in the saw. Make multiples at a time to save time. Quality control is key. And get a real saw. I use the same method for cutting rocks on my 10 inch saw with short pieces of 2x4's and for my 24" saw using short pieces of 4x4's. I use "Interior" rated wood glue so that the last slab of the rock will come off after soaking in water for a a few days. I messed up and used "Exterior" rated wood glue on one rock and it's been soaking for months with no loosening!! Usually let the small pieces on the 2x4's dry for a week, and the larger pieces on the 4x4's dry for 3 to 4 weeks. I usually have 1 set of drying while another set is cutting
|
|
chaosdsm
starting to spend too much on rocks

Member since April 2024
Posts: 106
|
Post by chaosdsm on Jul 21, 2024 19:18:45 GMT -5
Based on this: I will NOT be trying wood glue.... But, to be fair, he used Elmer's Carpenters Wood Glue which is NOT waterproof.... and did not appear to clamp it while the glue set... All wood glue manufacturers suggest at least 100psi of clamping force for the first 30 minutes. This helps push the glue into any pores that may be there. I think I'll try the thick CA route.... Loctite set a Guinness world record with their superglue lifting 5020 Kg with just 9 drops of glue. Although not directly relatable, as that's tensile strength, and its shear strength that is the primary factor in my application.. but at least CA is completely waterproof. Normal CA has a relatively low shear strength due to how hard (brittle) it sets up, but the KEG-500 remains flexible so its shear strength should be much higher. Almost $15k in debt right now, and my bonuses just vanished without warning, so not happening... at least not anytime soon...
|
|
chris1956
fully equipped rock polisher
 
Member since July 2022
Posts: 1,962
|
Post by chris1956 on Jul 21, 2024 19:34:54 GMT -5
Make your cut, clean the rock up real good. Clean it again. Run it through the dishwasher when the boss isn't home. Use good wood glue to glue it to your PERFECTLY clean wood and clamp it. Leave it longer, by a few days, than you think you need to, then cut your rock. If it does break loose, it probably was not real clean. I assume you are using only water in the saw. Make multiples at a time to save time. Quality control is key. And get a real saw. I use the water resistant wood glue and let it cure for two weeks (probably overkill but hasn't failed yet).
|
|
chaosdsm
starting to spend too much on rocks

Member since April 2024
Posts: 106
|
Post by chaosdsm on Jul 31, 2024 12:06:47 GMT -5
Make your cut, clean the rock up real good. Clean it again. Run it through the dishwasher when the boss isn't home. Use good wood glue to glue it to your PERFECTLY clean wood and clamp it. Leave it longer, by a few days, than you think you need to, then cut your rock. If it does break loose, it probably was not real clean. I assume you are using only water in the saw. Make multiples at a time to save time. Quality control is key. And get a real saw. I use the water resistant wood glue and let it cure for two weeks (probably overkill but hasn't failed yet). Definitely overkill, but, if you have the extra time to wait, go for it! Maximum bond strength for most wood glues is achieved within 24 hours at normal glue layer thickness of about 0.005 - 0.008" / 0.13mm to 0.2mm. For gap filling thickness up to about 1/32" allow 72 hours. Warmer temperatures will speed up the cure times, colder temperatures will slow down the cure times.
|
|
|
Post by HankRocks on Jul 31, 2024 12:53:01 GMT -5
I use the water resistant wood glue and let it cure for two weeks (probably overkill but hasn't failed yet). Definitely overkill, but, if you have the extra time to wait, go for it! Maximum bond strength for most wood glues is achieved within 24 hours at normal glue layer thickness of about 0.005 - 0.008" / 0.13mm to 0.2mm. For gap filling thickness up to about 1/32" allow 72 hours. Warmer temperatures will speed up the cure times, colder temperatures will slow down the cure times. I do the longer time, a week for a 2x4 and closer to a month for a 4x4. I have found that the glue towards the center of the rock does not dry as fast.
|
|
rockbrain
Cave Dweller
Member since January 2022
Posts: 2,955
|
Post by rockbrain on Jul 31, 2024 13:58:45 GMT -5
I have a 7inch blade tile saw with a guide fence, but I don't have any way to clamp rocks down and run them through the saw. Don't have any way to buy any other saw till at least next year, probably longer. Still, I want to cut very thin, consistently flat slabs. I'm looking for 1.2mm to 2.4mm thick slabs for various projects as well as some thicker slabs. I've thought of 2 potential ways to do this, just wondering if anyone has tried anything like this, or am I even on the right track? ? ? ? 1> Starbond KEG-500, Max Strength, Flexible, Medium Thick, Premium CA Super Glue: Make an initial cut on the rock and use the KEG-500 to adhere it to a block of wood, then just run it through the saw. The Starbond KEG-500 is supposed to have much higher bond strength than regular CA glues, but would it be strong enough to hold for up to 20 or so cuts on a 4" wide rock??? 2> Epoxy Pour: Much more expensive, but I could use rectangular silicone molds and pour a 1/4" to 1/2" thick epoxy base (depending on the stiffness of the epoxy) on the bottom of the rock to act as a guide. But I would end up with a thick piece near the end that I would probably still have to superglue to a block of wood 3> OTHER: I'm open to suggestions.... Those are some seriously thin slabs!
|
|
|
Post by Rockoonz on Jul 31, 2024 14:14:09 GMT -5
I have tried everything, well, lots of things, and the best is the original gorilla glue. Out of over 100 glue ups, probably a LOT more, I have had 3 fails, and all were due to error on my part not degreasing the stone well enough. Unless you're doing production, get the smaller bottles of glue, a big one will start to thicken and go bad long before you can finish it. After fully cleaning, wipe the rock surface to be glued with alcohol right before gluing. Use the cut end grain on the board, NOT the factory cut side grain. Clean wood is important, but the worst utility grade is fine, I look in the back of lumber at HD for the purple painted culls. Apply glue to the wood, and clean water to the rock right before joining them. Clamp with a bar clamp. spray the water around the perimeter of the join, Gorilla glue is water activated. Like this... 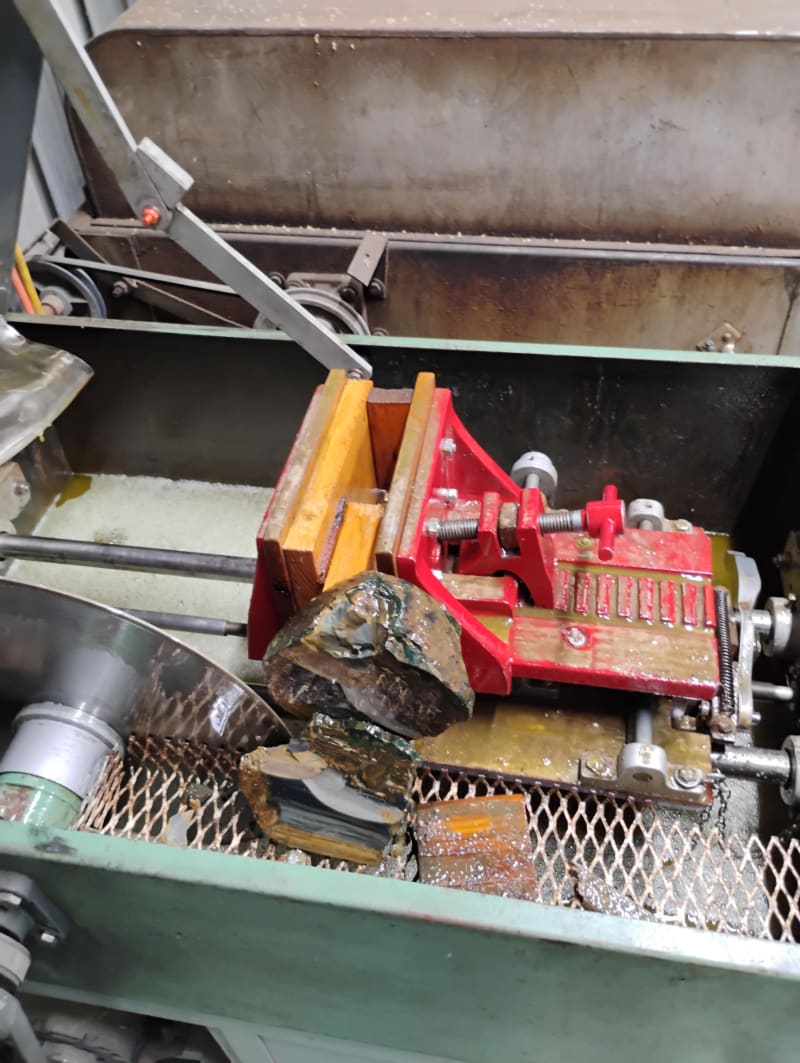 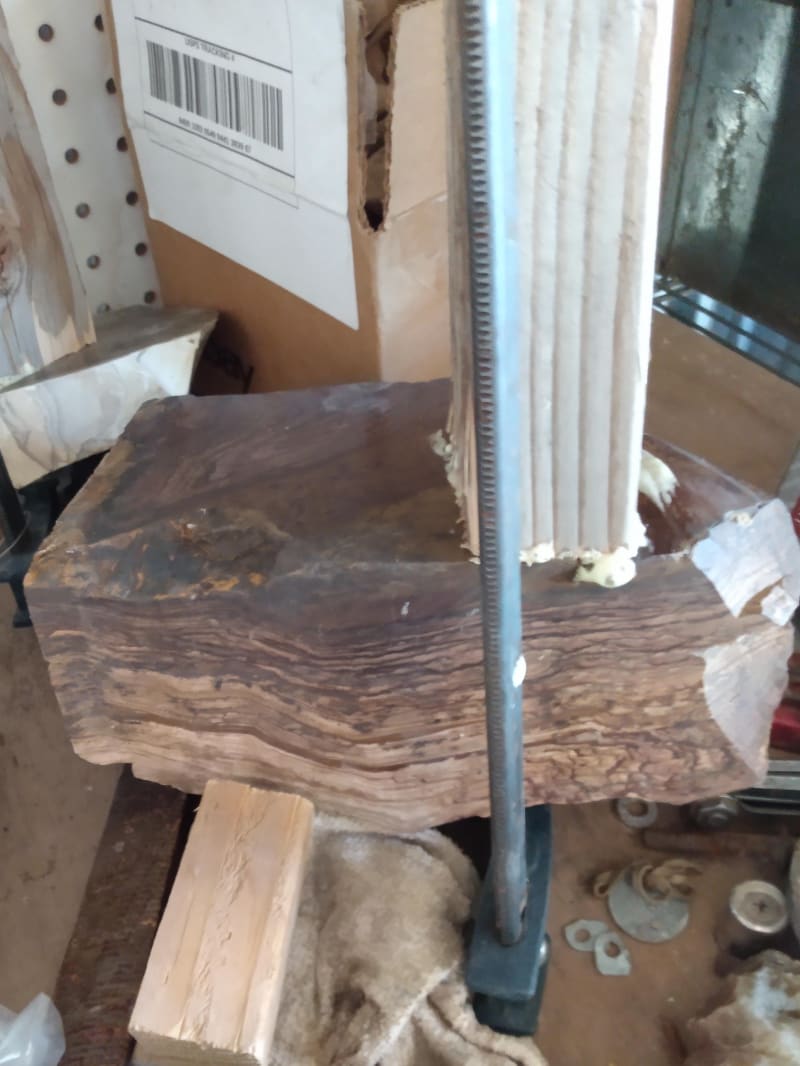
|
|
chaosdsm
starting to spend too much on rocks

Member since April 2024
Posts: 106
|
Post by chaosdsm on Jul 31, 2024 18:06:16 GMT -5
Yep, I have a few larger chunks of rock that appear to be fracture free, so I am aiming to make some guitar picks, and wind chimes. Though I should clarify, I'm hoping the finished thickness will be in that 1.2mm to 2.4mm range, so the cut slabs will need to be a little bit thicker, but not a whole lot more.
|
|
Mark K
Cave Dweller
Member since April 2012
Posts: 2,733
|
Post by Mark K on Jul 31, 2024 19:13:03 GMT -5
I have tried everything, well, lots of things, and the best is the original gorilla glue. Out of over 100 glue ups, probably a LOT more, I have had 3 fails, and all were due to error on my part not degreasing the stone well enough. Unless you're doing production, get the smaller bottles of glue, a big one will start to thicken and go bad long before you can finish it. I started with gorilla glue as well. I had about a 20% success rate. The rest came off on the first cut, usually 1/2 to 2/3 of the way through. That was with any type of rock. MT agate, jasper, stuff that may have been a little bit porous, almost everything failed. I even wand washed them with dish soap.
|
|
|
Post by Rockoonz on Jul 31, 2024 19:35:43 GMT -5
Mark K has to either be a process thing or bad glue, like I said the very few failures I've had were 100% on me for how I degreased. Got to clamp them too, all glues are weaker as the bond area becomes thicker. Also, LOTS of water to activate it.
|
|
chris1956
fully equipped rock polisher
 
Member since July 2022
Posts: 1,962
|
Post by chris1956 on Aug 1, 2024 13:03:34 GMT -5
Yep, I have a few larger chunks of rock that appear to be fracture free, so I am aiming to make some guitar picks, and wind chimes. Though I should clarify, I'm hoping the finished thickness will be in that 1.2mm to 2.4mm range, so the cut slabs will need to be a little bit thicker, but not a whole lot more. I have made some picks. Tough to get under 2mm thick. I tumbled them after cutting and some people said they were too slick to hang onto.
|
|
chaosdsm
starting to spend too much on rocks

Member since April 2024
Posts: 106
|
Post by chaosdsm on Aug 3, 2024 10:22:19 GMT -5
Yep, I have a few larger chunks of rock that appear to be fracture free, so I am aiming to make some guitar picks, and wind chimes. Though I should clarify, I'm hoping the finished thickness will be in that 1.2mm to 2.4mm range, so the cut slabs will need to be a little bit thicker, but not a whole lot more. I have made some picks. Tough to get under 2mm thick. I tumbled them after cutting and some people said they were too slick to hang onto. Bright & shiny is definitely a nice look, but even a tiny bit of sweat & it can go flying.... Typically, you'll need to grind a very slight recess into the pick for grip, or drill a pattern of holes. I had 2 Brazilian Agate guitar pics, one was 0.9mm thick high gloss finish, no grip at all, as soon as a little bit of sweat started, it would go flying. Second was 1.8mm high gloss finish, but it had a grove on either side of the pick put on after polishing. I could play for hours with that one, but I also had to keep mindful of it or it could slip. I drilled a pattern of 6 holes through the 0.9mm one, & I think the hole patterns give the best grip, but they also have the highest risk of breakage... It didn't break while drilling it, but about 6 to 8 weeks later I was playing and it just broke apart. It broke right on a layer line which was about 1mm from one of the holes, so I'm guessing the vibrations from the drilling may have played a part. A third option is to laser engrave a grip pattern onto the surface of both sides. I've only seen a laser engraved pick, so not sure how well that works. The ones I've seen look more like screen printing.... very light, very shallow engraving. My tests with laser engraving stone so far have left a much rougher look & finish but may be easier for gripping. Also considering sandblasting or acid etching a grip pattern onto the stone.
|
|
chris1956
fully equipped rock polisher
 
Member since July 2022
Posts: 1,962
|
Post by chris1956 on Aug 3, 2024 19:34:54 GMT -5
I have made some picks. Tough to get under 2mm thick. I tumbled them after cutting and some people said they were too slick to hang onto. Bright & shiny is definitely a nice look, but even a tiny bit of sweat & it can go flying.... Typically, you'll need to grind a very slight recess into the pick for grip, or drill a pattern of holes. I had 2 Brazilian Agate guitar pics, one was 0.9mm thick high gloss finish, no grip at all, as soon as a little bit of sweat started, it would go flying. Second was 1.8mm high gloss finish, but it had a grove on either side of the pick put on after polishing. I could play for hours with that one, but I also had to keep mindful of it or it could slip. I drilled a pattern of 6 holes through the 0.9mm one, & I think the hole patterns give the best grip, but they also have the highest risk of breakage... It didn't break while drilling it, but about 6 to 8 weeks later I was playing and it just broke apart. It broke right on a layer line which was about 1mm from one of the holes, so I'm guessing the vibrations from the drilling may have played a part. A third option is to laser engrave a grip pattern onto the surface of both sides. I've only seen a laser engraved pick, so not sure how well that works. The ones I've seen look more like screen printing.... very light, very shallow engraving. My tests with laser engraving stone so far have left a much rougher look & finish but may be easier for gripping. Also considering sandblasting or acid etching a grip pattern onto the stone. Thanks for the ideas. I guess they need to be more practical rather than perfectly shiny.
|
|
chaosdsm
starting to spend too much on rocks

Member since April 2024
Posts: 106
|
Post by chaosdsm on Aug 5, 2024 21:58:49 GMT -5
Depends on the use, for jewelry, definitely shiny, shiny, shiny!!! But even if it's for practical use, nicely polished can help it glide off the strings easily. Here's the 1.8mm Brazilian Agate pick I have. It was cut, polished, then had finger groves added to both sides.  I've actually found this pick much easier to play with than any other guitar pick because it doesn't hold onto the strings the way Delrin (like the 1.14mm Dunlop Gator Grip that used to be my go-to pick) & other plastic picks do. EDIT: Also just got my orders in from Kingsley North & Starbond: 0.36mm (0.014") kerf 6" continuous rim diamond blade, & the KEG-500 flexible CA glue! I just hope there's enough blade to make it all the way through the thickest piece. I know the 7" blade is tall enough, but it's a 1.8mm (0.07") kerf, which is lot of wasted material.
|
|