dtcmor
freely admits to licking rocks
 
Back to lickin' rocks again!
Member since May 2006
Posts: 898
|
Post by dtcmor on Mar 7, 2012 3:31:20 GMT -5
A friend of mine from work gratiously offered me a few deer antler sheds that he had found on his property in exchange for a primative style flint knife. I have been wanting to make some bone handles- all of my replicas so far have been with wood handles. My knapping friend, Dave Perry, was able to supply some superior points from Obsidian, Perdinallis and Flint Ridge. It turned out to be a fun project, and now I am hooked. Here are the resulting knives. We ended up trading away the Flint Ridge knife (bottom) as payment to our friend for all the horns. It was well worth it as now we have enough bone to make about 12 more knives for our trade shows!  5" Black Obsidian blade... 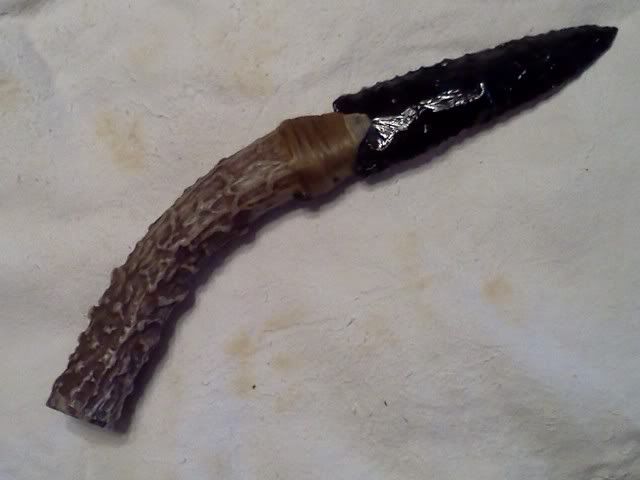 3 1/2" Perdinallis clovis style blade... 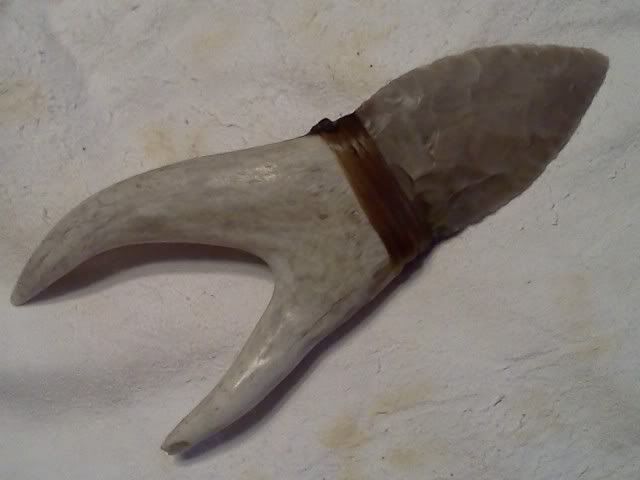 4" Flint Ridge Hopewell style blade... 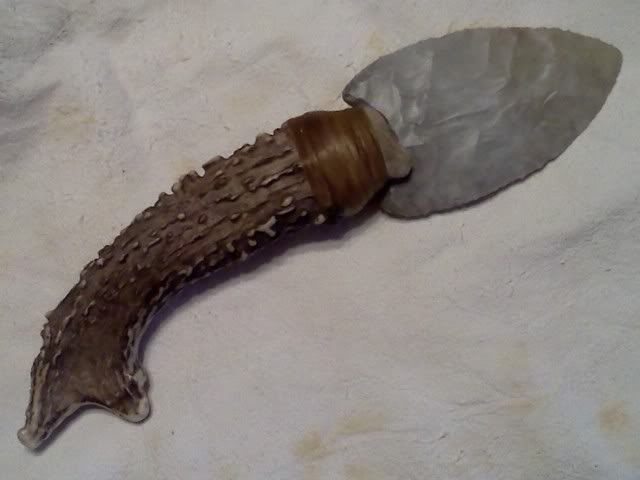 Thanks for looking! Dave
|
|
|
Post by helens on Mar 7, 2012 3:54:25 GMT -5
Wow... those are awsome!!! Um.. those ties look like catgut... that can't be real catgut?? (which I don't believe was ever made from real cats, but from sheep guts)
|
|
|
Post by Donnie's Rocky Treasures on Mar 7, 2012 6:52:48 GMT -5
Great job on those knives!
|
|
|
Post by FrogAndBearCreations on Mar 7, 2012 9:50:49 GMT -5
Very cool!
|
|
|
Post by NatureNut on Mar 7, 2012 9:56:34 GMT -5
Very cool. Love how they turned out. Great deal. Jo
|
|
rockingthenorth
fully equipped rock polisher
 
Member since January 2012
Posts: 1,637
|
Post by rockingthenorth on Mar 7, 2012 12:07:24 GMT -5
way cool knives
|
|
hulagrub
spending too much on rocks

Member since October 2009
Posts: 256
|
Post by hulagrub on Mar 7, 2012 19:15:33 GMT -5
Dave, they are way cool!!!!!!!
|
|
|
Post by Toad on Mar 7, 2012 20:47:07 GMT -5
They look great.
|
|
herchenx
Cave Dweller
Member since January 2012
Posts: 3,360
|
Post by herchenx on Mar 7, 2012 20:47:18 GMT -5
Really nice
|
|
NDK
Cave Dweller
Member since January 2009
Posts: 9,440
|
Post by NDK on Mar 7, 2012 20:48:35 GMT -5
Fantastic pieces Dave! Sounds like you made a great trade.
Nate
|
|
dtcmor
freely admits to licking rocks
 
Back to lickin' rocks again!
Member since May 2006
Posts: 898
|
Post by dtcmor on Mar 7, 2012 21:07:50 GMT -5
Thanks everyone!!  Helen - The wraps are a modern synthetic nylon chord with a beeswax coating. After I wrap them, I heat them with a lighter or candle to shrink the chord and melt the wax. It gives it such a realistic appearance. I have used actual tendon chord before, but the process is messy and its hard to get it to shrink and dry as perfect as the nylon.
|
|
adrian65
Cave Dweller
Arch to golden memories and to great friends.
Member since February 2007
Posts: 10,790
|
Post by adrian65 on Mar 7, 2012 23:19:41 GMT -5
They look beautiful, all of them. Me too, I thought you were using some natural material to wrap the blade.
Adrian
|
|
|
Post by helens on Mar 7, 2012 23:28:12 GMT -5
Well that looks completely real and just amazing!!! I watched a few videos on knapping... it looks like a lot of fun too!! If you're in an area with a lot of flint, you'd do great. Also, Sue said that knappers heated the rocks so they could knap better... when heated, the colors are PHENOMENAL. The color alone might draw extra people to your sales, and make your knives even more spectacular looking (which is hard to do, they are pretty spectacular!!). She would certainly be able to tell you more about it, but I can definitely vouch for the flints colors getting mindblowing (the colors come out like Willow Creek or Mozarkite).
|
|
dtcmor
freely admits to licking rocks
 
Back to lickin' rocks again!
Member since May 2006
Posts: 898
|
Post by dtcmor on Mar 8, 2012 0:28:06 GMT -5
Thanks Adrian- I just happened to see your knife project (I have been away for a short while and am just now catching up...). Yours is a truly amazing work of art!! I could only dream of creating something like yours!!  Helen - It is true that knapping is a neat artform. It takes a very long time to master though, even the basics. I have been learning for about 3-4 years now from my friend and trade partner Dave Perry. He can create fantastic replicas in 30 minutes or less. For me, I still break more points than I can make. But the learning process is so rewarding. In reguards to heat treating the flint, most of our materials are heated, the only exception is usually Obsiadian. I live in Ohio and Flint Ridge material here is a great example for color change and workability. The bottom knife is Flint Ridge, but without much color change. My camera and lighting were poor, but the blade is actually a blue tone with yellow and orange towards the tip. Flint Ridge is hard to heat just right because the temperatures need to reach 700-800 deg. in order for the colors to really pop. My friend and I are using differant methods to see which works best. I would like to try a kiln, but they are too expensive, and we need something that will handle large volumes also.
|
|
|
Post by helens on Mar 8, 2012 4:59:45 GMT -5
Hi DTC:). I guess I won't be taking up knapping anytime soon... if in 3-4 years you still haven't mastered it, I'll probably need 10:P. Also, I don't think I have the physical strength it looks like a lot of the guys in the videos have to physically poke the tool in a rock and PULL a piece off. Over and over and over again. It's incredible. Took a quick look at NW Ohio's Craigslist for you... there's a ceramic kiln listed for $500 (ceramic kilns are the biggest and also the cheapest kind of kiln): toledo.craigslist.org/art/2839225890.htmlThat's not the cheapest price I've seen, but it looks almost new. It doesn't have a digital controller, but for heating rocks, I don't think you'd need one, as precise temperatures may not be necessary, and you can check on the progress. Digital kilns are useful for controlling the timer, so you can walk away. There's another option, which is to build your own kiln. It will still cost you a lot because firebricks are EXPENSIVE... but you might even be able to buy/trade/get free a completely destroyed one for the frame and firebricks and replace the heating elements, pyrometer, thermocoupler and controller with new parts and make a really big kiln for your rocks. If you need info, I can help you find it, I've done TONS of research on kilns because you can't do glass without one:). If you are going to make knives for sale often, it may be cheaper to buy the kiln, you should be able to get one for less than $500 (or negotiate with the guy selling the one on the craigs list... who knows... you may be able to swap him a couple of knives for it:P). When people want to get rid of kilns, they want to GET RID of them because they take up a lot of physical space... never know if he'd be willing to trade or bargain:). I don't know if different heating produces different colors... but Sue sent me Ohio Flint Ridge Flint.... so I'd guess it's the same materials near you maybe. It was the first flint I'd ever seen, so I assumed all flint was brightly multi-colored. It's only recently that I discovered that flint wasn't always FIRE red and orange. Here's a few pieces she sent that were heated:     And here's what's INSIDE the most uncolorful one of all, after grinding more than 1/2 the flint away (point being that the color penetrates the entire stone): Original flint:  Inside color (smack in the middle of rock)- this photo is true color... it's BRIGHT:  Flint polishes like a dream too... very fast, and very very shiny, so I don't think heating affects the structural integrity of the rock any. She said that the knappers always heats it to make knapping easier (no just for color). Your work is GORGEOUS, I think brightly colored blades would help you sell them. Did you check on ebay? There's several people selling knives similar to yours on Ebay, and they charge hundreds for them. Here's one: www.ebay.com/itm/EXTRAORDINARY-Buckeye-Burl-handle-Knife-on-Stand-Wicked-Lace-Obsidian-flint-/110831983959?pt=LH_DefaultDomain_0&hash=item19ce19dd57#ht_777wt_1127They aren't all as pricey as the above, here's another: www.ebay.com/itm/Large-Exotic-Flow-Obsidian-Cody-Knife-Flint-Knapping-Black-Powder-Mountain-Man-/110837725946?pt=LH_DefaultDomain_0&hash=item19ce717afa#ht_1084wt_1127I don't know how big the market is for those, but there can't be too many people making them, and I'd think Southwestern gift shops would eat them up:).
|
|
meta99
has rocks in the head
 
Ohio Flint Ridge flint
Member since October 2010
Posts: 540
|
Post by meta99 on Mar 8, 2012 9:00:08 GMT -5
Helen's flint was heat treated the old fashioned way on site at Nether's Farm. It was left over from knappers who didn't want anything with vugs or crystals to interfere with their knapping. I picked it up because I liked the colors. Snuffy has some of it too. I'd be interested in knowing if it tumbles.... Sue
|
|
|
Post by helens on Mar 8, 2012 22:09:13 GMT -5
Sue, I can answer that now... they DO tumble, and very well... UNLESS they have crystals in them... then they are iffy. I put in a beautiful thin slice with a little bit of crystals running through... and the tumbler split the piece up and ate the crystals:(. That was the only casualty tho. Now this is in a vibe tumbler, I don't know how a rotary would do with them. What the vibe does is shine them, with almost no shaping. That's exactly what I wanted tho, no shaping, I like the shapes:).
|
|
dtcmor
freely admits to licking rocks
 
Back to lickin' rocks again!
Member since May 2006
Posts: 898
|
Post by dtcmor on Mar 9, 2012 1:56:38 GMT -5
Thanks Helen for all the info!  The kiln on craigslist is still out of my price range unfortunatly. I had thought of ways to make a homemade one also, that way we could put it together a few pieces ay a time as money allows us. The method we use now is primative (just like the ancient people did), but it works fairly well. We have a shallow, bowl shaped pit about 1ft deep and we lined it with sand. We layer the flint in the bottom and cover with more sand, alternating about 3 layers this way until the pit is full. Then we light a fire over the pit and regulate the coals all day long to maintain an even temp. After about 12 hours we let the coals burn themselves out overnight, and by the middle of the next afternoon it is cool enough to take the flint out. Most of the pieces cook well, and those that need more get added back in the next time. It sounds primative, but it really does work good. The idea is to slowly ramp the temperatures up to the hottest point - this can take about 4-5 hours, and then try to hold max temps for at least 6 to 12 hours, depending on the type of flint. Then the cool down is about 10 hours. I have also done some flint in a turkey roaster with good results. The temps there are only about 400-500 deg. and works well on cherts and other flints. I did see those auctions on e-bay too. There is a wide price range on the knives it seems. It basically comes down to what the customer will think is a fair price. We have sold pieces cheaply at some shows and festivals, only to go to the next show and get top dollar for them then. We arent really out for profit, as most of the shows we do are for demonstration and hands on teaching only, and most of the money goes back into buying more materials. We make alot of other replica artifacts also - spears, arrows, tools etc. Most of our profit is actually the satisfaction of teaching and passing on the art of knapping and the ancient cultures. For us, it is just plain fun to do. 
|
|
|
Post by Woodyrock on Mar 9, 2012 17:59:32 GMT -5
Dave: Your knives are looking very nice, wish that Ohio flint was closer. Will the turkey roaster get hot enough for the Ohio flint? I like the heat treatment of the wrap, it sure does improve the look. Sausage casing looks pretty good, maybe even better than real sinew, but it too is messy to work with. When you figure out shows, you could make a fortune teaching the rest of us. Gun shows are a good for knapped knives. Last year I did a Christmas show, took 100 knives, and sold five, when I thought this show would be a good one..it was juried, and hard to get in. About this time every year, I have to explain to IRS why I have such a low business profit. Woody
|
|
|
Post by Bikerrandy on Mar 9, 2012 20:21:27 GMT -5
Those knives are sweet!!
|
|