|
Post by BearCreekLapidary on Sept 14, 2004 0:24:13 GMT -5
Hello everyone, I have a few photo's of some Fire Agate for you. Lotarocks was inquiring about them the other day and I just finished this stone this evening. This is not a traditionally cut Fire Agate. It has been cut from behind the orbs, instead of, from on top of the orbs. The traditional cut gives you nice convex (domed) orbs and this design gives a nice concaved (curved inward) orbs, that really make the light dance around inside of the tiny bowls and reflect more color. This beauty has every color you could ask for in Fire Agate - gold, orange, red, blue, green and a hint of purple. I thought you might like to see what it looked like .... so here goes ....    The face of this stone was not going to offer me much in the way of cutting a nice stone ... but the back side of the color layers was just booming with color ... so I took advantage of the opportunity. Hope you enjoy the photo's, John
|
|
|
Post by Cher on Sept 14, 2004 1:08:57 GMT -5
|
|
lotarocks44
having dreams about rocks
Member since April 2004
Posts: 54
|
Post by lotarocks44 on Sept 14, 2004 7:09:12 GMT -5
that is so pretty i dont have a cutter so i just have to tumble it right now. thanks alot for the pictures
|
|
|
Post by rockyraccoon on Sept 14, 2004 10:44:34 GMT -5
i don't see how you have any left if your wife picks out the good ones cause i haven't see any i would want to leave behind!
kim
|
|
|
Post by BearCreekLapidary on Sept 14, 2004 21:35:31 GMT -5
Hello Kim, Now you know why I keep the door closed when I am cutting cabs  Enjoy, John
|
|
deepsouth
fully equipped rock polisher
 
He who rocks last rocks best
Member since January 2004
Posts: 1,256
|
Post by deepsouth on Sept 14, 2004 22:03:09 GMT -5
Hey John , they look even nicer than Belgian Chocolates.. Too nice to be eaten.
You had better hide them in a strongroom.
Wow so pretty
Thanks for sharing ;D
Jack
|
|
|
Post by cookie3rocks on Sept 14, 2004 22:08:57 GMT -5
If anything ever deserved a Yummy rating, that does. Good enough to eat!
cookie
|
|
Malkavic
noticing nice landscape pebbles

Member since March 2004
Posts: 77
|
Post by Malkavic on Sept 14, 2004 22:23:09 GMT -5
Wow... nice work John... I have one question though.... How do you get such a wonderful polish on your stones? I've got the cutting down, but I am having a hell of a time getting the polish to take... I have a cabbing machine, and have been trying the leather polishing wheel, with tin and cerium oxide... but for the most part, I get more scratches than polishing...
Any help is greatly appreciated on this one...
Billy
|
|
|
Post by BearCreekLapidary on Sept 15, 2004 11:19:38 GMT -5
Hello Billy,
Ancient Chineese Secret ;D ... and no it's not Calgonite (Who remembers that commercial?)
I use many different polishes for many different stones:
Agates, Petrified Woods, Obsidians, Porcelain Jaspers, Opals: Optical Grade Cerium Oxide with a pinch of Linde A - this polish is awesome! It will also help remove small scratches from your stones (when used on a polishing wheel)
Turquoise, Malachite, Howlite - Titanium Oxide works great.
Victoria Stone - Aluminum Oxide works the best.
Material - Is your material solid (there are some very poor jaspers out there, that just do not take a polish worth a darn).
Sanding - Are you getting the sanding marks off of the stone from the previous sanding drum/wheel. I use a jewelers magnifying visor to inspect the stone before I go to the next stage - so you don't strain your eyes, and it helps you to see scratches that you might have overlooked with the naked eye.
Equipment - Silicone carbide or diamond wheels? What stages are you sanding through? 220, 600 and then to polish or 280, 600, 1,200 and then 14,000 and then on to polish?
Polishing wheel/pad - some people will argue to the death, that 400rpm through 700rpm is the ultimate polishing speed ... that may be true on some materials, but, not all of them. Some people like a very damp/wet polishing wheel, where as others like an almost dry wheel. Some people use a very light pressure to polish the stone and others use a lot of force when polishing. I polish at 1725rpm, damp leather pad, and depending on the stone - I'll use light pressure for the softer stones and moderate pressure when polishing harder stones.
Polishing time - a lot of people do not take their time when polishing stones, and thus do not get a better polish. If I have a good dense agate, I'll polish it for a good 10 minutes or so and with the combination of the Linde A (.3 micron and a Mohs 9 hardness) and Cerium Oxide polish - you'll find that your cabs will be scratch free and absolutely smooth - even when magnified by 15 times. So, to the un-aided eye ... it's a true blazing beauty!
Polishes - there are a bunch of different polishes on the market today. Some are very general polishes (they can be used with many different stones) and others may have a specific intended use for one or two kinds of stone. I would not use Titanium Oxide on an agate, nor would I use any Linde A on Turquoise. It all comes down to what works best for you.
Contaninated wheels/pads - I accidently had some 220 grit silicon carbide grit get on one of my polishing pads - IT WAS RUINED! If you are getting scratches from your polishing wheel ... it may be contaminated? I would recommend that you try to change it out and try a new clean one and see what happens there. Polishes can also become contaminated ... so you may be dealing with a compounding problem.
If you are certain that the scratches you are seeing after you try to polish the stone were not there before you started the polishing phase ... then it sounds like a contaminated polish wheel/polish.
Also, always use a clear towel/rag to wipe down your stones when polishing them. If you are using a dirty towel/rag and then going back to the polishing wheel ... you may be putting contaminates on the wheel that way too.
A quick question: is your machine set up with the polishing wheel right next to the grinding/sanding wheel?
I hope this has been of some help, if there is something else that I can try to help with ... let me know.
Enjoy,
John
|
|
|
Post by Cher on Sept 15, 2004 12:42:17 GMT -5
John, Thank you so much, this was very helpful. And The Rock Shed thanks you too *smile* I just place an order for more grit, including some of the 1000 grit Al Ox and some Tripoli. ;D ;D [glow=red,2,300] ~ Cher ~[/glow] pages.prodigy.net/bestsmileys1/signs/RockOn.gif [/img]
|
|
Malkavic
noticing nice landscape pebbles

Member since March 2004
Posts: 77
|
Post by Malkavic on Sept 15, 2004 13:59:03 GMT -5
Wow, thanks for all the information, John...
To answer a few of the questions...
The polishing wheel is to the direct right of the grinders... I have a Barranca Cab Combo setup with the 6" trimsaw, 2 diamond grinding wheels, and the expandable drum, with the polishing setup on the end... The grinding wheels are 60 and 220 I think... and then I have a few belts for the expandable drum that are 400, 600, 800, and 1200. So the highest I have right now is 1200... I then have the leather pad, and some almost meshlike pads, that came with syringes of polishing compound... but I was having horrible luck with those... so I stuck to the leather pad, and was using my cerium and tin oxides that I had from my tumblers...
A few of the rocks are coming out really well... I have a few pieces of Larvikite that turned out brilliant... it seems that the rocks that I cut anything other than domed, are coming out horrible. It's very possible it's my technique, since as you said, I am the type that doesn't take enough time with the polishing...
I cut a 6 sided agate pendant the other night, and tried to polish it with the tin oxide... only the very outer points of the sides were polishing... and it was leaving a very odd brown film, as if it were wearing off the leather and sticking it to the rock... very disturbing.. ::chuckles::
I'll try to take more time with them, and see if I can clean the leather pad to reduce any contamination... I may give the other polishing pads a shot now... they came with higher end grits... I think the highest being 15,000 grit polish... so we shall see how that works...
Anyway, Thanks again for all the good info...
Billy
|
|
|
Post by BearCreekLapidary on Sept 15, 2004 21:36:41 GMT -5
Hello Billy,
You might find it to your advantage to remove the leather plishing pad when you are grinding rock (so that the rock dust doesn't come in contact with the leather pad and contaminate it).
Domed stones are far easier to polish, compared to the flat stones. When you are pushing the stone into the wheel, only the edges of the stone really get a good contact with the sand paper, which creates a slight void on the very top of the stone. You might try a medium dome on that piece, which will aleviate the flat spot, allow the sand paper to contact the entire surface, which will turn out a much nicer stone. Unless you are using a lap (flat silicon carbide lap or a diamond lap) the larger flats can be a real booger to get perfectly smooth.
As far as the brown film - if it a dry hard film that you have to scratch off with your fingernail ... you are using too much pressure on the leather polishing wheel, which causes the water to evaporate and causes heat. This heat will turn your polish into a hard paste that will cake up on your stone. Try a little less pressure and more water/polish on the pad.
See if this helps any.
Have a great day!
John
|
|
Malkavic
noticing nice landscape pebbles

Member since March 2004
Posts: 77
|
Post by Malkavic on Sept 17, 2004 3:07:42 GMT -5
Thanks for all the good advice, John.... I worked with a piece of tiger iron earlier today, and took your advice, and went a bit gentler on the pressure, and amazingly it polished up great... now I just have to go back with the carnelian and regrind it down and then try again on the polishing... I'm having good luck with Larvikite and the tiger iron so far... going to try my hand on some obsidian in a bit... also the fire agates seem to be polishing well, but most of those are bubbled, and are taking well with the curves... it's the flat spots on most of the rocks that give me the most problems... I've pondered using a dremel with a polishing head, and see how I come out with that...
Thanks again, and I'll keep you updated on the progress.
Billy
|
|
|
Post by krazydiamond on Sept 18, 2004 17:11:48 GMT -5
oooh, yeh, this is real good info here, must bookmark this page so i don't ask all the same questions.....you should publish, Bear!
hey, Billy, what is Larvikite ? never heard of it, gotta pic?
hey Bear, what is Victoria Stone? gotta pic? i have a neice named Victoria, would be a great present, where do you get it?
thanks for all the good natured help! KD
|
|
Malkavic
noticing nice landscape pebbles

Member since March 2004
Posts: 77
|
Post by Malkavic on Sept 18, 2004 22:36:16 GMT -5
Hey KD... here's a pic of the Larvikite in rough form.. I recieved a few pieces from Ebay... it's native to Larvik, Norway... 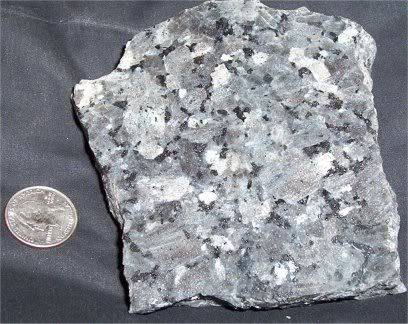 It's a really nice rock to work with... similar in flashiness to Labradorite and Spectrolite... cuts well, and has a good solid basis to work with. Billy
|
|
|
Post by BearCreekLapidary on Sept 18, 2004 23:18:11 GMT -5
I'm Back ...
Billy - that looks pretty nice, I am going to have to try some of that. I have never cut any of that before.
KD - Victoria Stone ... here is a litttle history of the stone:
History of Victoria Stone
In the mid 1960’s an aged Japanese scientist, Dr. S. Imori (retired from the Institute of Physical & Chemical Research in Tokyo) devoted himself to the creation of gemstones. Although he worked on several types (Meta Jade, Maple Jade, Halo Stone and Meta Amethyst), Victoria Stone was his piece de resistance and a crowning worldwide commercial success.
Victoria Stone is/was made of natural raw minerals: quartz, feldspar, magnesite, calcite, fluorspar, etc. Those materials were fused together by heating them to intensely high temperatures to form a molten magma (he actually melted the rocks). They were “mineralized” to a new mineral by adding special crystallizers and crystal habit regulators to the molten rock. The magma was then poured into boules and placed under 2000 pounds of pressure. The cooling process was in an extremely controlled environment (taking months to cool). During this time the phenomenal chatoyant crystals were formed. As you can surmise, Victoria Stone is not a synthetic or simulated gemstone. While being mineralogically similar to Nephrite Jade, the arrangement of the actinolite crystal is not the same. The stone has a Moh’s hardness of 5.5 to 6.0; a specific gravity of 3.02; and a refractive index ox 1.62.
Victoria Stone was marketed in thin, calibrated cabochons and beads. Eventually the rough (in over twenty different colors) was marketed through the Lapidary Journal. The rough was sound in four-pound boules at a cost of $20.00 per pound, which was exorbitantly expensive for lapidary material at that time. Unobservant lapidaries that did not follow the explicit instructions for decompressing and slabbing the boules rendered much of the material sold uncabbable. Due to the difficult and tedious process of decompressing the boules, and the fact that Dr. Iimori himself marketed calibrated cabochons, one rarely finds freeform cabochons. Lapidary dealers, anywhere, rarely offer freeform cabochons. Production of Victoria Stone ceased sometime in the 1980’s, upon or around the time of Dr. Imori’s death. As far as anyone knows or can find out, Dr. Imori was the only person to ever know the formula, and it was lost with his passing. Others have spent thousand of dollars and tried to reproduce this spellbinding legendary gemstone. Alas, all that is left in the world is what was purchased and produced 20 – 35 years ago (that was decompressed properly).
Victoria Stone is commonly found with many minor flaws. Fractures, decompression fractures, very small air bubbles are not uncommon. True gem grade Victoria Stone is in itself an extreme rarity. True gem grade Victoria Stone has sold in the past for ten times what the lesser grades of this material has sold for. It is extremely rare! It is not uncommon for a gem grade freeform cab in an approximate size of 30 mm x 20 mm to sell for $200.00 to $300.00, depending on the degree of chatoyancy (the play of light across the stone), style of cut, color and finish. Most gem grade material is highly coveted and prized, and is rarely every sold.
In the past year, three original uncut boules were sold at a price of $1,100.00 per boule or $275.00 per pound. That is $3,300.00 for approximately 12 pounds of Victoria Stone. There was one Indigo Blue boule, one Blue/Green boule and one Yellow/Green boule. The Indigo Blue and the Blue/Green are the higher prized colors of the three.
The prices for Victoria Stone have skyrocketed in the past ten years, and it is fully expected to continue its upwardly climb. Victoria Stone is an excellent investment. Twenty years ago, you could buy it for $20.00 a pound and now (if you can find any) you will pay close to $200.00 - $400.00 per pound. If an uncut boule of brown, black or white and possibly gray were found, it would command prices of unheard of proportions. Possibly as high as $5,000.00 per boule. As for all of the colors that were produced…these four are the rarest colors of them all.
I hope that you have enjoyed the history of the Victoria Stone.
It's an absolutely gorgeous stone.
I wish I had some left ... I sold my collection a year ago and I kick myself every time I think about it.
I am always looking for Victoria Stone.
Hope this helps,
John
|
|