|
Post by Drummond Island Rocks on Dec 23, 2018 11:56:45 GMT -5
This one was all about persistence. I accidentally ordered 26 gauge bezel material instead of 28 gauge. The problems started right away. The thick bezel wire was difficult to even get pushed against the stone to get the length correct. I soldered it and it was too loose so I cut it at the solder joint and took some more material out to get it right. The whole time I was working on the bezel and soldering I knew the thick bezel was going to give me problems. When I put the stone in I tried using the bezel pusher with no luck. I then tried to push the bezel over using the burnishing tools also not much success. As a last ditch effort I ended up using the plastic end of my jewelers hammer and beat the bezel over. Not the best approach and I needed to file some marks out but I think I salvaged it. Lesson learned. I wont try that again. 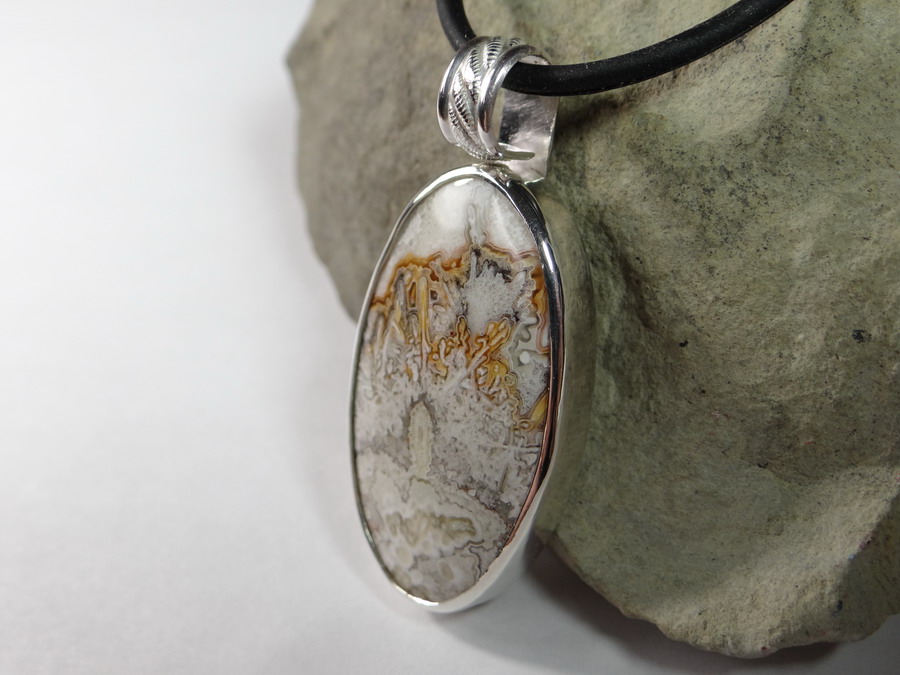 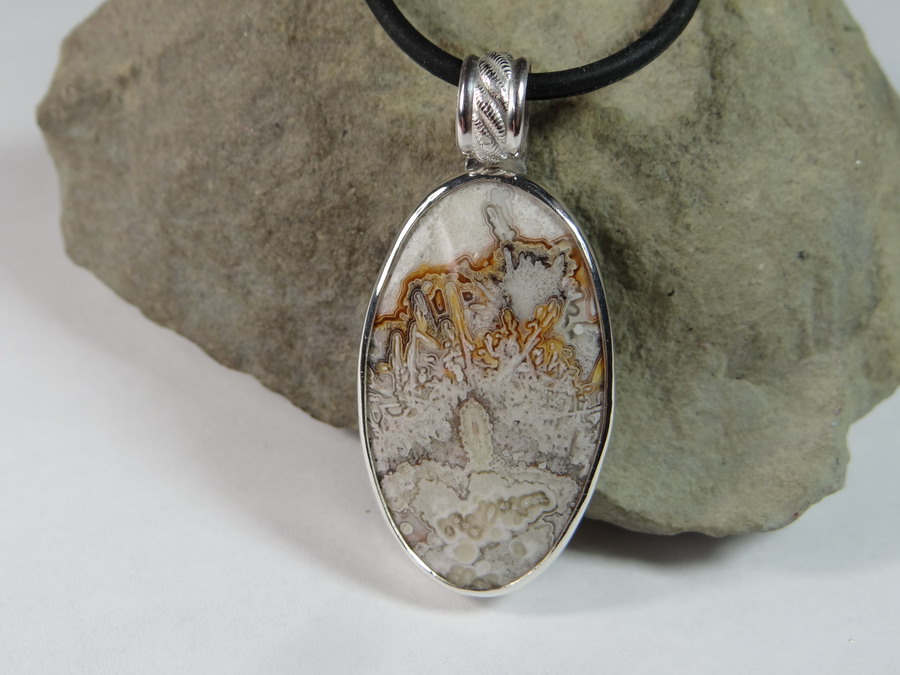 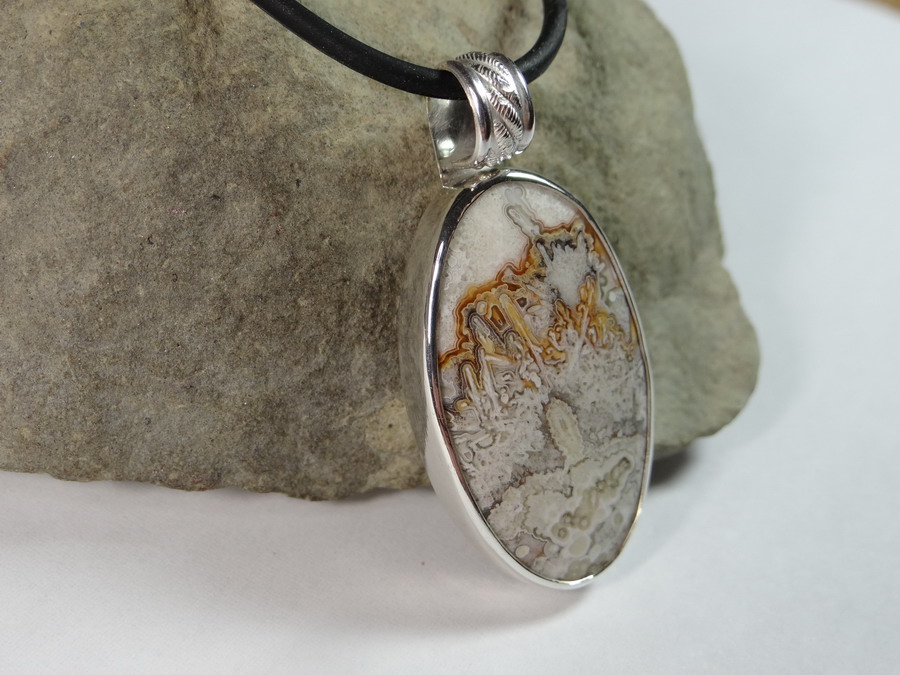 Thanks for looking Chuck
|
|
quartz
Cave Dweller
breakin' rocks in the hot sun
Member since February 2010
Posts: 3,357
|
Post by quartz on Dec 23, 2018 12:19:16 GMT -5
Looks like you worked through it pretty well, nice piece.
|
|
|
Post by rockjunquie on Dec 23, 2018 12:21:06 GMT -5
You wouldn't know by looking at it that it gave you problems.
|
|
|
Post by Bluesky78987 on Dec 23, 2018 12:26:08 GMT -5
All's well that ends well! I like your bail - gonna copy that.
|
|
|
Post by toiv0 on Dec 23, 2018 12:34:39 GMT -5
I use the 26 ga all the time. Make sure they sent you .999 and not sterling. You can aneal it and make it more workable. You can also sand down the thickness where you are going to push it over. (I do this when using sterling for bezel.) All that said I think your piece is awesome.
|
|
|
Post by MsAli on Dec 23, 2018 13:28:30 GMT -5
I think it came out fantastic!
|
|
|
Post by miket on Dec 23, 2018 13:32:11 GMT -5
It's amazing. Great work!
|
|
|
Post by hummingbirdstones on Dec 23, 2018 13:36:01 GMT -5
The pendant turned out beautiful! I'd never guess you had trouble with it.
|
|
|
Post by Drummond Island Rocks on Dec 23, 2018 13:50:35 GMT -5
I use the 26 ga all the time. Make sure they sent you .999 and not sterling. You can aneal it and make it more workable. You can also sand down the thickness where you are going to push it over. (I do this when using sterling for bezel.) All that said I think your piece is awesome. You hit the nail on the head. The item number I had been using in the past at RIO was not available anymore so I guessed and was way off. I just looked at what I ordered ended up being 24 gauge .925 sterling strip. Really bad for bezel work. Chuck
|
|
|
Post by Drummond Island Rocks on Dec 23, 2018 15:24:09 GMT -5
I use the 26 ga all the time. Make sure they sent you .999 and not sterling. You can aneal it and make it more workable. You can also sand down the thickness where you are going to push it over. (I do this when using sterling for bezel.) All that said I think your piece is awesome. When I soldered the bezel strip to the back plate with medium solder wouldn't that have annealed the bezel strip? I have never annealed metal before but I thought it was just heating till it starts to turn pink. A quick google search says medium silver solder melts at 1390 degrees and annealing silver is listed at 1200 degrees. Chuck
|
|
|
Post by vegasjames on Dec 23, 2018 15:40:11 GMT -5
Looks great to me.
|
|
|
Post by toiv0 on Dec 23, 2018 16:35:55 GMT -5
I use the 26 ga all the time. Make sure they sent you .999 and not sterling. You can aneal it and make it more workable. You can also sand down the thickness where you are going to push it over. (I do this when using sterling for bezel.) All that said I think your piece is awesome. When I soldered the bezel strip to the back plate with medium solder wouldn't that have annealed the bezel strip? I have never annealed metal before but I thought it was just heating till it starts to turn pink. A quick google search says medium silver solder melts at 1390 degrees and annealing silver is listed at 1200 degrees. Chuck Depends on where to directed your flame. If your whole piece including the bezel turns pink its probably to hot and if that is the case yes it would have anealed it. You would also have fire scale more than likely also unless you protected the piece. When you aneal you bring it up to the pink color, let it set a second then quench it.
|
|
|
Post by Drummond Island Rocks on Dec 23, 2018 16:51:21 GMT -5
When I soldered the bezel strip to the back plate with medium solder wouldn't that have annealed the bezel strip? I have never annealed metal before but I thought it was just heating till it starts to turn pink. A quick google search says medium silver solder melts at 1390 degrees and annealing silver is listed at 1200 degrees. Chuck Depends on where to directed your flame. If your whole piece including the bezel turns pink its probably to hot and if that is the case yes it would have anealed it. You would also have fire scale more than likely also unless you protected the piece. When you aneal you bring it up to the pink color, let it set a second then quench it. Thanks. Still a lot to learn. Just finished another one. Went a little better. Now that I know this is 24 gauge I just used the pusher a bit then went straight to the hammer. Chuck
|
|
|
Post by opalpyrexia on Dec 23, 2018 18:28:16 GMT -5
I routinely use 24 gauge for pendant and ring cabs, and 26 gauge for earring cabs. I just prefer the look of a heavier bezel (including 20 gauge if I'm setting a large faceted stone). And I hand hammer-set all cabs. Rather than use a hammer directly, to make it easier to control and limit marking the silver I use one of these two punches I made: 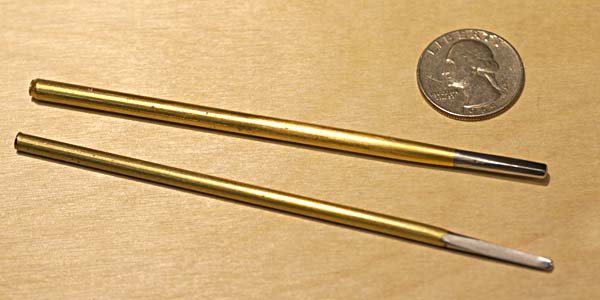 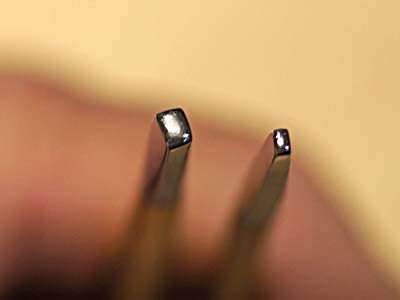 Marking tends to be minimal and pretty limited to the edge of the bezel. Then I take my absolute favorite pumice wheel to take out the marks. They're white, knife edge wheels on which I've sanded a flat edge. They're fast and do a great job and you can go directly to tripoli polish or follow with fine wheels prior to triploli and final polish. 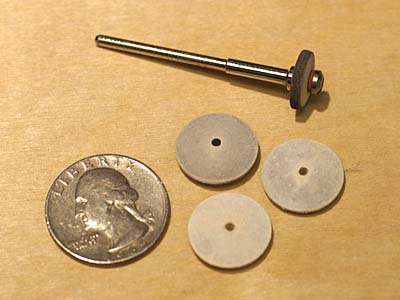 I've purchased all of these pumice wheels on eBay — when they show up. I don't need any more, but there's a guy on eBay right now who has 6 sets of 20 wheels for a decent price: www.ebay.com/itm/Cratex-or-WR999-rubber-abrasives-Select-Wheels-Knife-sizes-grit/372053500550?hash=item56a01de286:m:m9ghEKcsk5hncaon3nfd_vQ:rk:12:pf:0
|
|
|
Post by hummingbirdstones on Dec 23, 2018 20:35:03 GMT -5
opalpyrexia did you make those out of brass rods? I've been meaning to make some but didn't know what metal to use.
|
|
|
Post by opalpyrexia on Dec 24, 2018 0:00:21 GMT -5
opalpyrexia did you make those out of brass rods? I've been meaning to make some but didn't know what metal to use. Yes, they're made with brass rod with short sections of nails silver-soldered on the businesss end.
|
|
|
Post by fernwood on Dec 24, 2018 3:34:22 GMT -5
The cab is awesome. You did a great job with the setting.
|
|
NDK
Cave Dweller
Member since January 2009
Posts: 9,440
|
Post by NDK on Dec 24, 2018 10:21:27 GMT -5
Chuck you perservered and that's what matters. Nice job finishing the setting, your hard work paid off.
|
|
|
Post by toiv0 on Dec 24, 2018 10:26:06 GMT -5
opalpyrexia did you make those out of brass rods? I've been meaning to make some but didn't know what metal to use. Yes, they're made with brass rod with short sections of nails silver-soldered on the businesss end. What is the purpose of soldering onto brass? Why not just use the nail itself?
|
|
|
Post by toiv0 on Dec 24, 2018 10:31:33 GMT -5
I routinely use 24 gauge for pendant and ring cabs, and 26 gauge for earring cabs. I just prefer the look of a heavier bezel (including 20 gauge if I'm setting a large faceted stone). And I hand hammer-set all cabs. Rather than use a hammer directly, to make it easier to control and limit marking the silver I use one of these two punches I made: Is the 24 ga you use for your bezel sterling or .999? Do you cut it yourself? Thanks
|
|