mrhomescientist
having dreams about rocks
Member since October 2019
Posts: 51
|
Post by mrhomescientist on Feb 16, 2020 1:36:14 GMT -5
Here are my first attempts at making cabochons! I started with a cheap grab bag of slabs that I purchased, and stenciled in some shapes. I think this one is jasper? 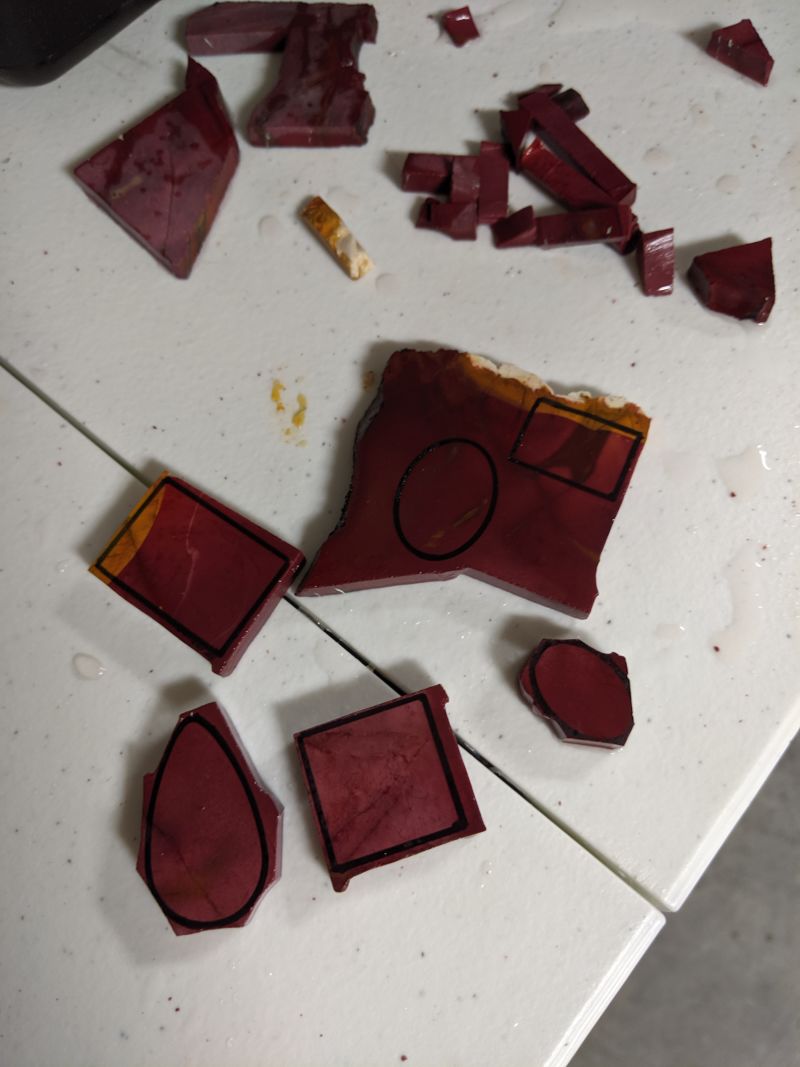 After roughing out the shapes for this and a few other slabs: 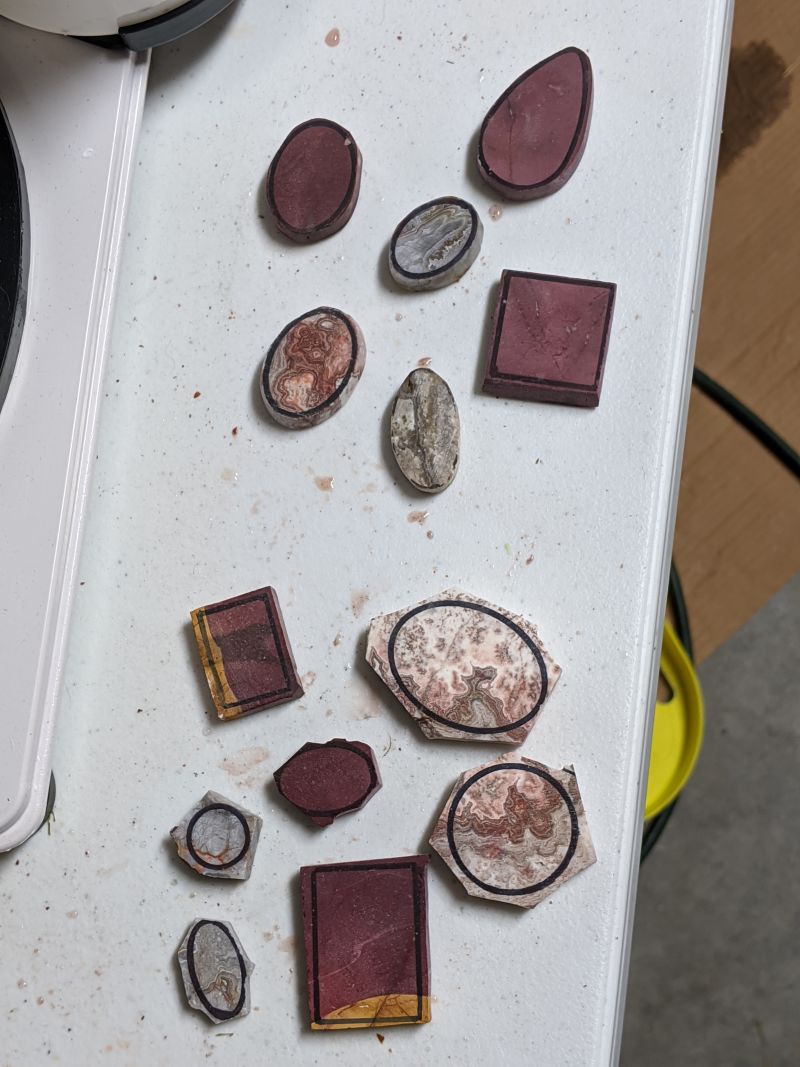 And after dopping: 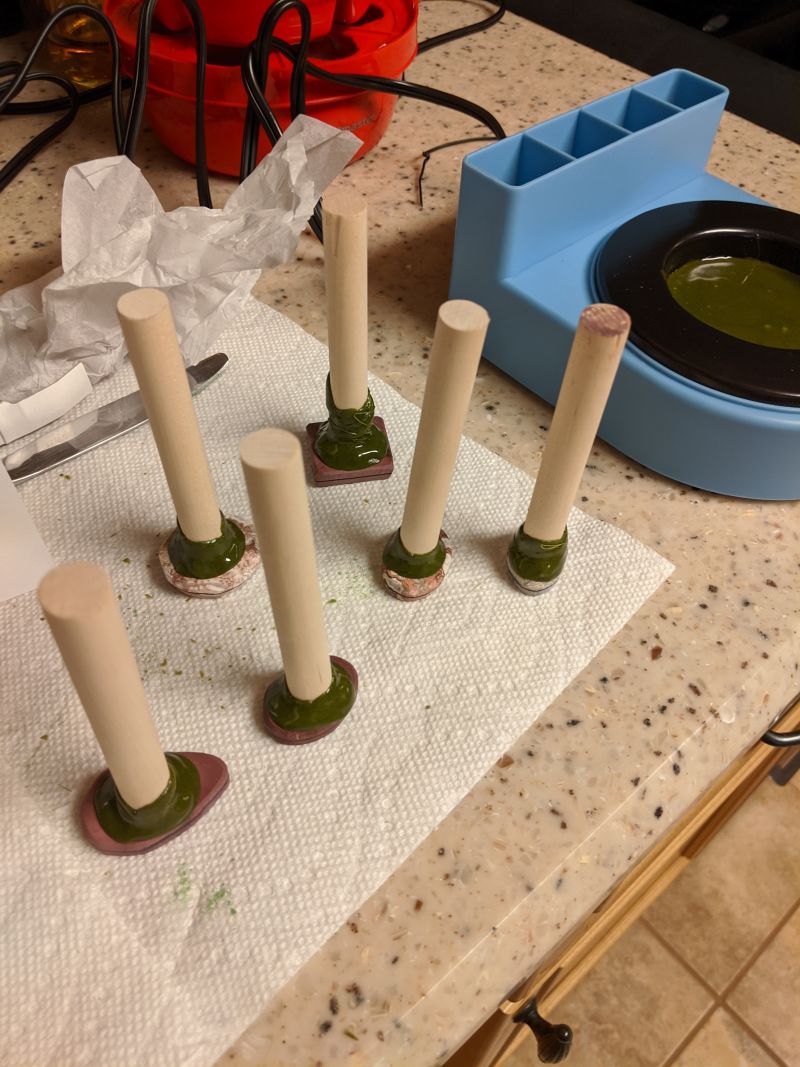 I smoothed out the edges with my flat lap on the coarse wheel (180 grit) and ground out the first angles to make the dome shape. I used the same wheel to then smooth over the angles to create the dome. Then, I switched to the next wheel (brown, 325 grit) and tried smoothing a few of the stones. It's working, but it's going very slowly. Take a look at this one: 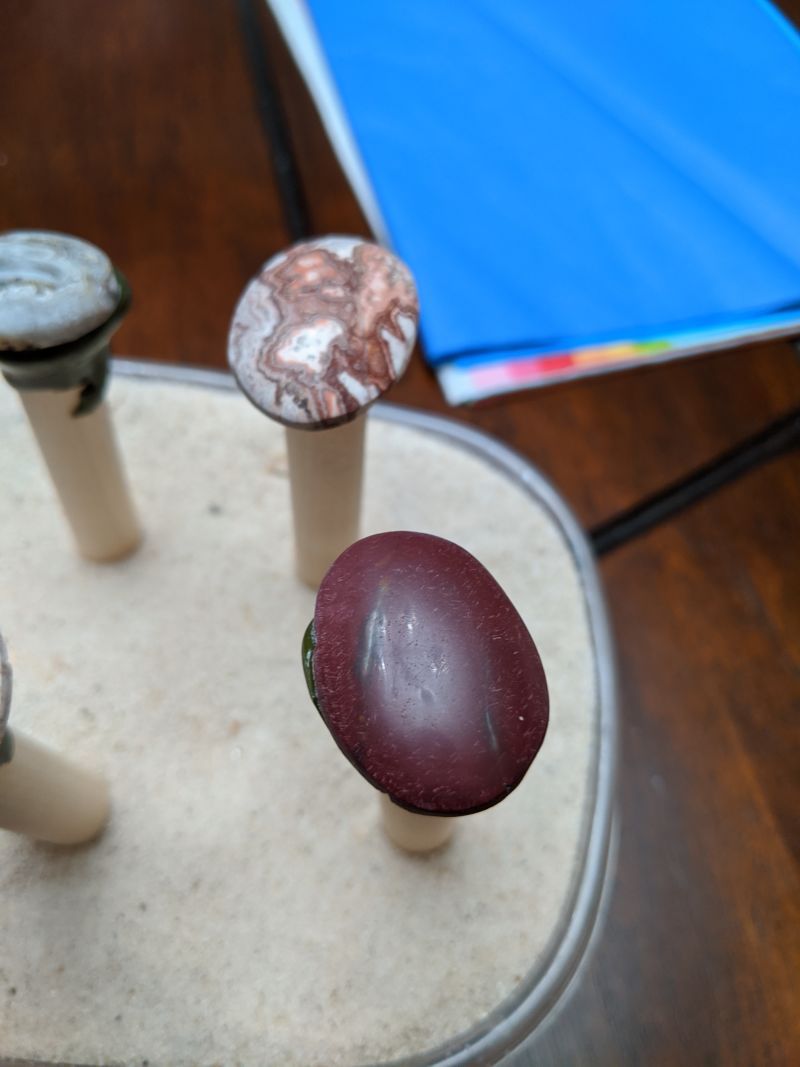 I've been at that one on the brown wheel for probably a half hour at least, and there are a lot of stubborn scratches that just don't want to go away. Is this how long it should take? I heard that experts can take a full stone from rough to finished in 30 minutes, so spending that much time on just one stage doesn't seem right. Any advice is appreciated!
|
|
|
Post by MsAli on Feb 16, 2020 8:26:39 GMT -5
When you are first starting out, it may take longer, especially depending on the stone.
What machine are you using?
You may have to go back to the 180 and then try the 325 again
Watch your pressure. Let the wheel do the work -that was a hard one for me to learn
and lastly really watch running a stones top across that 180, some dont like it much and the scratches will be harder to work out
|
|
|
Post by MsAli on Feb 16, 2020 8:42:12 GMT -5
So I read your other thread that introduced you to us.
I started learning on an arbor w/ expander wheels and belts then got my own all you need slant lap
I really wish I would of just saved up the extra money and bought a cabking.
The learning curve is completely different and yes it takes more time to pump out a cab on it
(at least for me it does)
now I have a ringleader cabochon unit to use and yesterday I did two cabs (obsidian) in less than an hour and wont go back to cab on the slant lap EVER. Although it will come in handy for final polishing and flatting the backs of cabs.
|
|
|
Post by hummingbirdstones on Feb 16, 2020 9:52:10 GMT -5
That first stone looks like it could be mookaite. If it is, it's pretty hard stuff. MsAli gave you some good advice. Let the diamond do the work. Go back to the 180 and gently go back over the whole cab until all the deep gouges are gone. Then move on to the 325. It does take longer to use the flat lap to cab than wheels, but it is still a great machine and I use mine still. I bought it a long time ago (20 years?) when I started cutting opal and it's still going strong.
Another alternative is to buy a 220 diamond disc and another base lap and use that as an in-between grit.
|
|
|
Post by hummingbirdstones2 on Feb 16, 2020 9:56:29 GMT -5
Yeah, what MsAli said - on all counts.
Cabbing on wheels is definitely easier than it is on a flat lap. I started with a cheap flat lap, and was amazed by the difference when I got a used Genie. New laps or wheels are also more aggressive than they will be after they're broken in. It's good to cut a few cabs of consistently harder agate to break them in.
The closeup of the oval cab has some low or "flat" spots. That fits with what Ali said about dropping back to the 180. Holding a cab in hand and looking away while you rub your thumb lightly over the surface will often help you find flat spots that aren't obvious to the eye.
The rough that cab came from looks like it has little lighter colored spots in it. If that's the case, they might be softer than the surrounding material and might or might not ever polish up the same as the rest of it. That's a really common (and annoying) fact of lapiday life. Mixed hardnesses in a stone are a royal pain.
I see you're using fairly large dop sticks. Depending on your hand size you might want to try other sizes. I use smaller ones unless the cab is really large. That's all just personal preference, and you'll get a feel for what you like best in no time.
Most of all, just have fun!
|
|
|
Post by hummingbirdstones2 on Feb 16, 2020 10:01:22 GMT -5
Oh yeah, I forgot one thing. I learned to "cheat" very quickly. I found Eastwind brand resin laps to be smoother and more flexible than some others. When combined with a foam rubber backer they "drape" nicely over the domes.
|
|
mrhomescientist
having dreams about rocks
Member since October 2019
Posts: 51
|
Post by mrhomescientist on Feb 16, 2020 12:10:26 GMT -5
Thanks for the replies! Lots to think about. So I did try going back to the 180 and it didn't seem to do much. I thought it was causing the scratches, since they weren't present on the original slab. Where else would they come from?
So I should go back to the 180 and try smoothing again? It's difficult for me to know when all the deep scratches are gone. There's a local-ish guy that offers lapidary classes that I'll probably take him up on eventually. If you've read my other thread on tumbling, he's actually the owner of Hogg Mine. Bit of a drive to get there, though. I'm in north Florida.
And yes the brown and white bits on the red stone are much softer. The white even crumbles easily.
|
|
|
Post by MsAli on Feb 16, 2020 12:49:53 GMT -5
Even one lesson would be worth it
sometimes it helps to see others do it rather just reading about
|
|
|
Post by knave on Feb 16, 2020 12:51:08 GMT -5
It helps to dry the stone to see remaining flaws
|
|
|
Post by knave on Feb 16, 2020 12:52:32 GMT -5
Take a pencil or paint pen and Mark all over the rock. Helps to see when you’ve covered the whole rock.
|
|
|
Post by hummingbirdstones2 on Feb 16, 2020 12:57:24 GMT -5
Sounds like your laps are still really new, so it might help to slab some harder translucent type agate and cut five or ten of those. Use light pressure and maybe slow the rpm speed down a bit. The translucent material will really show the scratches, and you'll be able to judge how different speeds and pressures feel. Also listen for any ticking sounds - it's always possible to get a clump of diamond or some particles that are higher than the surrounding surface.
Breaking in any new lap or wheel with some agate will always help you get better results. Eventually, when your laps get really well-worn and start slowing down so much that you replace them, don't toss them. You'll want those for softer stones.
|
|
|
Post by Rockoonz on Feb 16, 2020 13:21:33 GMT -5
Sounds like everybody has given some excellent advice, I can offer encouragement. When I started I would generally "finish" a cab in a day, 4 to 5 shop hours basically. Now, about 15 years later, when in production mode they take between 15 and 20 minutes on average for fairly standard free form shapes, and the more complex shapes with inside curves or difficult materials from 30 min to an hour. Intarsia, doublets, triplets, and carved pieces will increase the time as well. It looks like you are already ordering your operations in a way that will help a lot once your steps get to be more automatic. A teacher at the NW rockhound retreat makes all his cabs with a flat lap. He has an elaborate collection of plated steel laps and the flexible toppers with rubber discs under them to do it. I have a few shapes of focal beads that I make that could be made almost entirely with a lap, but since I have a 6 wheel cabber I only use the lap for shaping. Learning to do everything on a lap is especially helpful if you want to take your hobby on the road, laps can be very portable.
|
|
mrhomescientist
having dreams about rocks
Member since October 2019
Posts: 51
|
Post by mrhomescientist on Feb 17, 2020 22:09:30 GMT -5
I tried working a few more crazy lace agate pieces that I had, to help break in the 180 wheel. I then went over one of my other red stone cabs, and I'm still seeing a lot of those deep scratches. 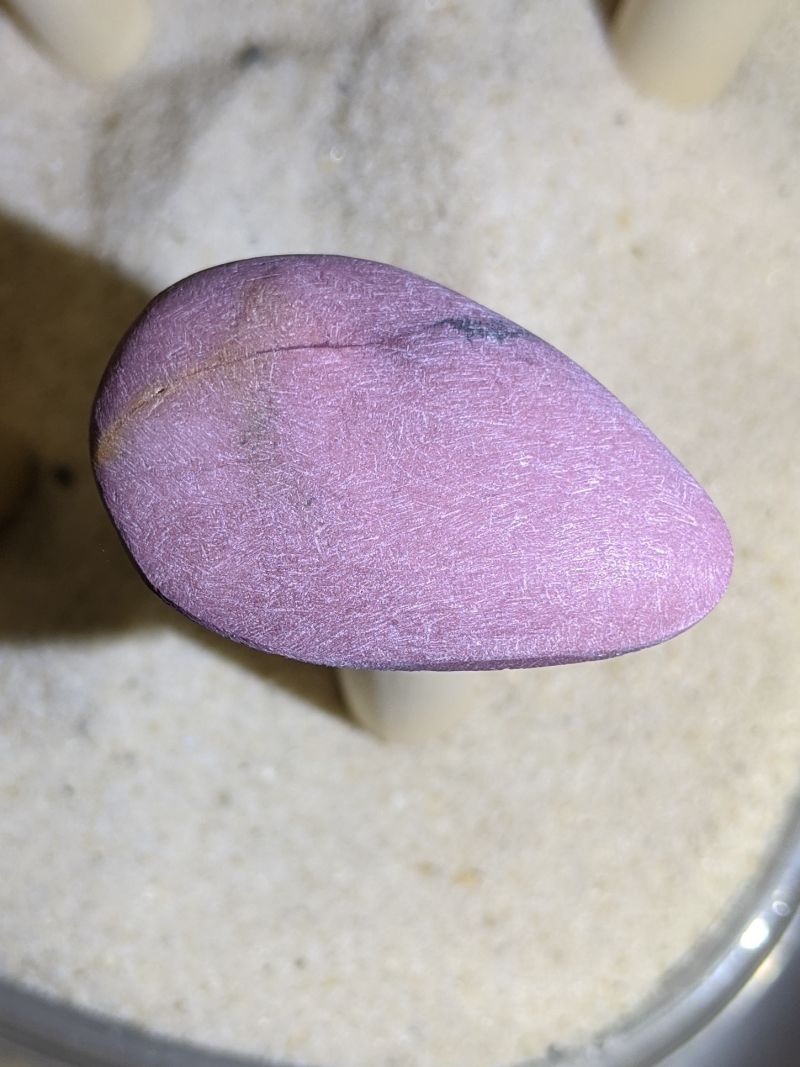 I mean, that's definitely caused by the wheel. Does that not polish out at the next step? I don't see how I can shape a stone without causing deep scratches. I must be missing something. For reference, here's the stone from before under the same lighting. 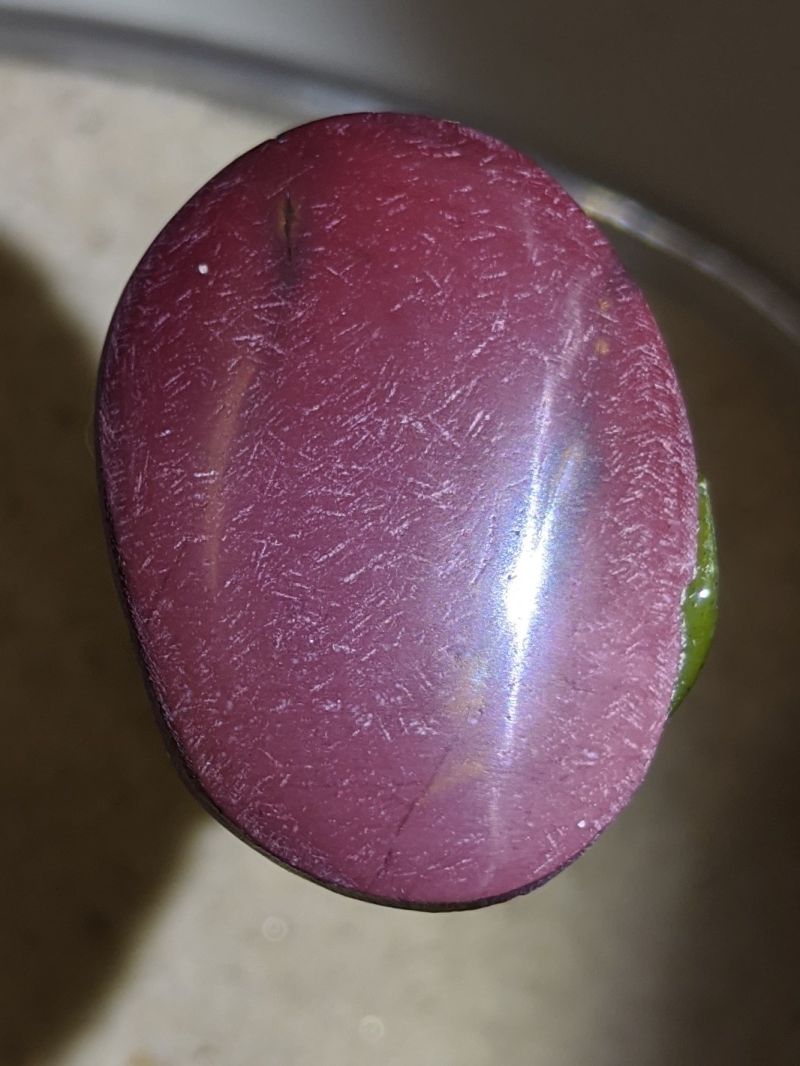 I do also have a big Brazilian agate I can slab and cut up, if you think the wheel being new is the problem.
|
|
|
Post by hummingbirdstones2 on Feb 18, 2020 8:00:36 GMT -5
Those scratches will decrease as the 180 is broken in more. I hate breaking in new wheels.
Like Robin said, adding a 220 grit to the sequence would help a lot.
|
|
mrhomescientist
having dreams about rocks
Member since October 2019
Posts: 51
|
Post by mrhomescientist on Feb 18, 2020 8:24:47 GMT -5
Looks like the "official" disc for the All-U-Need comes in 260 grit - hitechdiamond.com/shop/electroplated-diamond-laps/Good enough? It's $80 though  Here's a 240 on Amazon for cheap, but I think it's just the disc and not the acrylic backing plate, which would be another $25 or so.
|
|
|
Post by joshuamcduffie on Feb 18, 2020 8:46:22 GMT -5
I always went from 180 grit to 220, but I think MsAli was correct, you need to use a lighter hand on the 180 wheel, especially once you have it close to the desired shape. It's a common mistake that most of us probably did when we started cabbing. One more thing to check, are you using enough water? Make sure you are. As knave said, Try drying the stone occasionally while working, and you can see scratched areas you need to polish on.
|
|
|
Post by hummingbirdstones on Feb 18, 2020 8:49:27 GMT -5
You can buy a 220 disc and a separate backer plate to put it on.
A little bit cheaper and they'll last a long time. I still have all my original backer plates. I just have to replace the smoothing discs every once in a while. It takes a really long time to wear those suckers out.
|
|
|
Post by MsAli on Feb 18, 2020 9:10:33 GMT -5
Adding the 220 helped ALOT! Highly recommend it
|
|
mrhomescientist
having dreams about rocks
Member since October 2019
Posts: 51
|
Post by mrhomescientist on Feb 18, 2020 19:08:26 GMT -5
I'm slabbing a little piece of crazy lace agate, and it seems like it's taking ages. How long should a piece this size take to cut through? It's on a 10" saw, and the piece is 2" long x 2" tall at the highest point. I've been going for probably 20 minutes to make that progress. 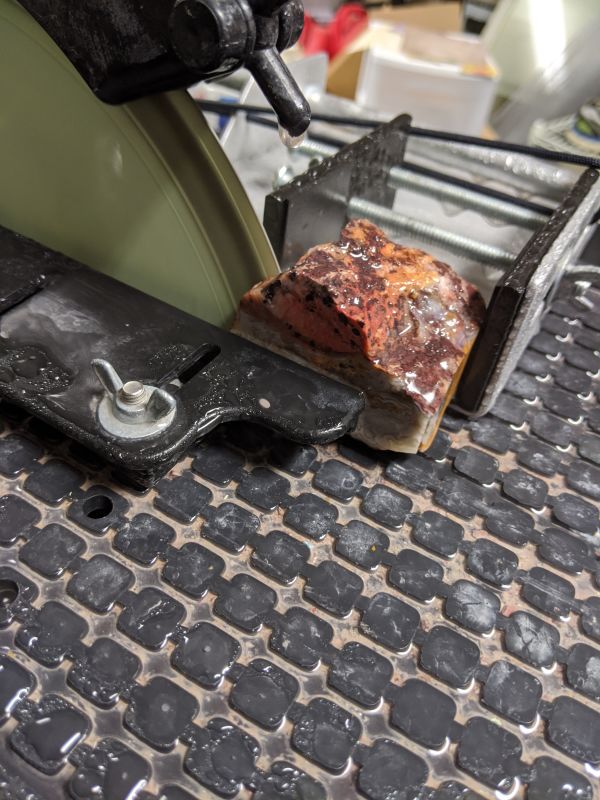
|
|
mrhomescientist
having dreams about rocks
Member since October 2019
Posts: 51
|
Post by mrhomescientist on Feb 18, 2020 19:11:27 GMT -5
Also, I just rigged up a weight system to keep pressure on the vise. Is that wise? How much weight should be in there? 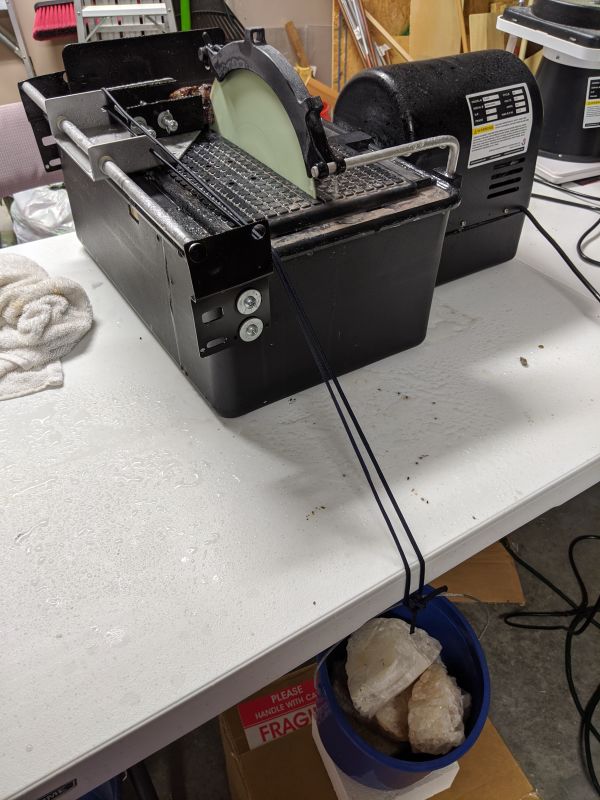
|
|