|
Post by Drummond Island Rocks on Jun 3, 2020 18:13:01 GMT -5
|
|
AzRockGeek
has rocks in the head
 
Member since September 2016
Posts: 703
|
Post by AzRockGeek on Jun 3, 2020 18:42:31 GMT -5
It should not matter what side of the arbor you press it out from, the arbor shaft on the inside is 0.87" from bearing to bearing, it is milled down for the inner sleeve of the bearing and then milled down to 0.75 for pulley and blade. At least on one I have that is currently torn apart.
Tim
|
|
AzRockGeek
has rocks in the head
 
Member since September 2016
Posts: 703
|
Post by AzRockGeek on Jun 3, 2020 18:48:01 GMT -5
After looking at your pictures again, I would definitely press it from the pulley side so that you don't have to remove the flange at the end. Mine is completely torn apart, so it did not seem like it made a difference. :-)
|
|
|
Post by Drummond Island Rocks on Jun 3, 2020 19:39:24 GMT -5
After looking at your pictures again, I would definitely press it from the pulley side so that you don't have to remove the flange at the end. Mine is completely torn apart, so it did not seem like it made a difference. :-) Is it ok to put a 2x4 against the pulley side and beat it out of the housing or should I try to find a machine shop that can press it out? Pretty sure I used the brute force method on my 14" but that does not make it right, lol Chuck
|
|
AzRockGeek
has rocks in the head
 
Member since September 2016
Posts: 703
|
Post by AzRockGeek on Jun 3, 2020 19:46:56 GMT -5
After looking at your pictures again, I would definitely press it from the pulley side so that you don't have to remove the flange at the end. Mine is completely torn apart, so it did not seem like it made a difference. :-) Is it ok to put a 2x4 against the pulley side and beat it out of the housing or should I try to find a machine shop that can press it out? Pretty sure I used the brute force method on my 14" but that does not make it right, lol Chuck Haha.... That is something I would do, it usually creates extra work filing down the arbor from the dings from hitting it too hard.  Do you have a Harbor Freight near you? You could probably by a cheap press for less then taking it to a machine shop. Remember... They don't make these arbors no more, so don't ruin it.
|
|
|
Post by Drummond Island Rocks on Jun 4, 2020 18:59:10 GMT -5
Well impatience won and I beat the arbor out of the housing. I attached the housing to a piece of plywood then snugged that plywood up against a concrete step. With it held in place I put a piece of 2x4 against the pulley side and gave it a couple hard blows. It came out pretty easy. Now that left me with an arbor that has the blade flange, splash shield and bearing on it. The bearing can't be removed without removing the blade flange and shield. I dropped that part off at a machine shop today and they are supposed to see if they can press it all off. I came across a post from captbob from years ago about trying to disassemble a poly arbor. Did you ever successfully complete that project captbob? Any hints? I did look into getting a bearing press. I have two projects going right now that both require a press for removal and for installation. Probably makes sense but that is a tool that takes up room and only gets used once a year at the most. Will that shield slide right off? it spins freely right now but is trapped between the blade flange and bearing so I cant tell if it is attached or just slipped on. The steps on the shaft look like what AzRockGeek described. Shaft is .875" diameter. I.D. of bearing is .79 (14mm) and then it is turned down to 3/4" on the pulley side and tapped 3/4" on the blade side. 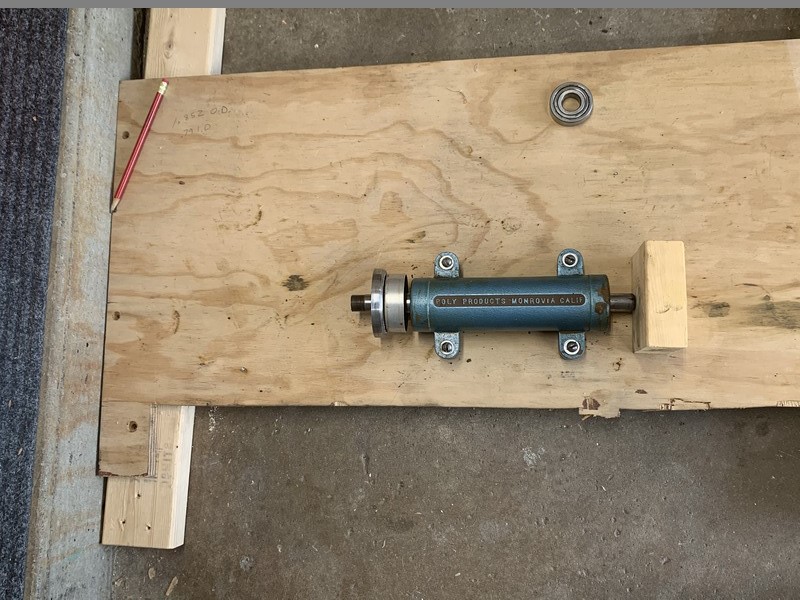 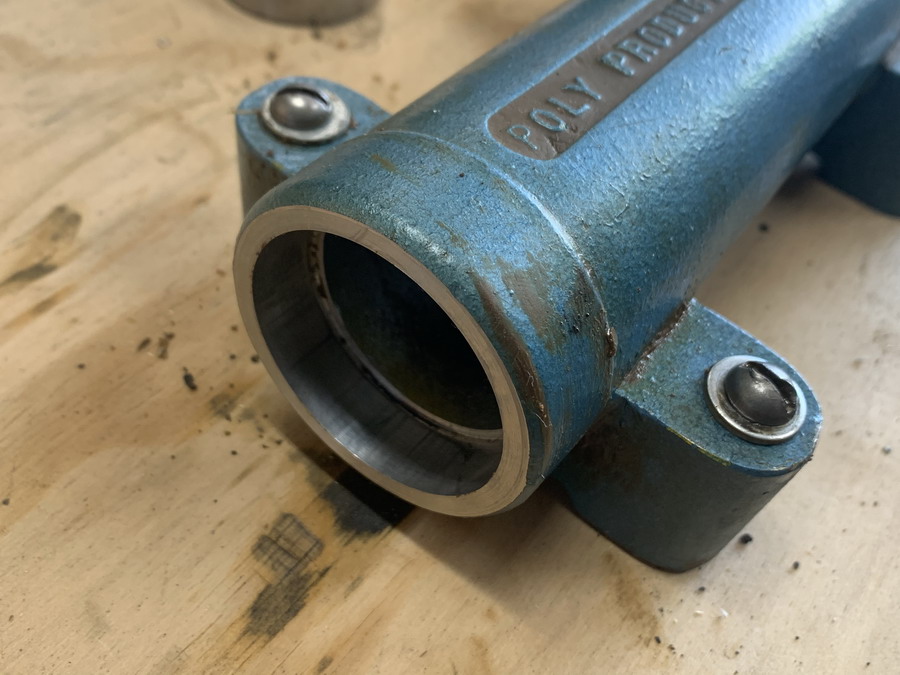 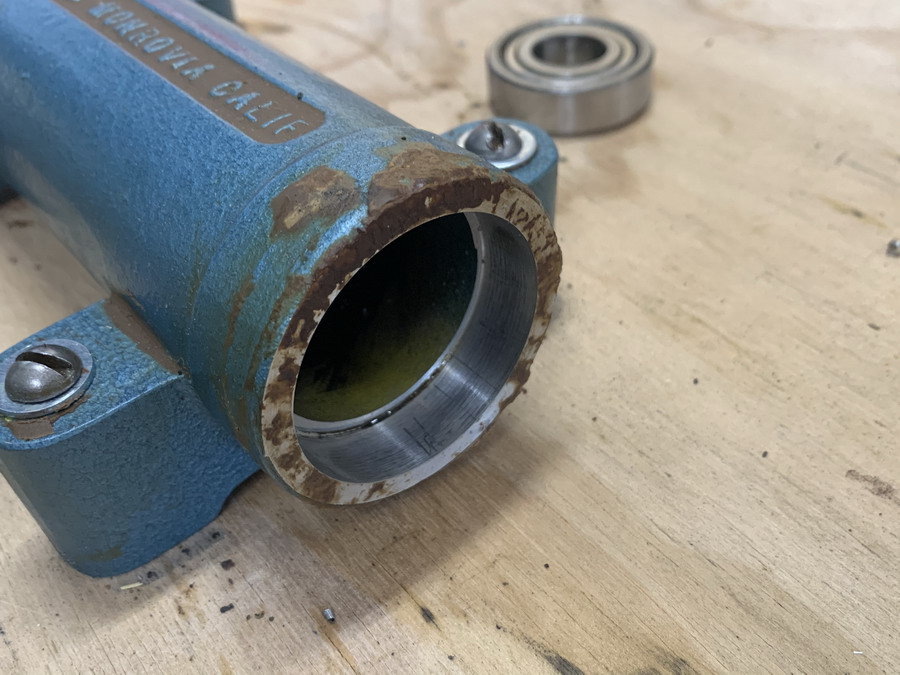 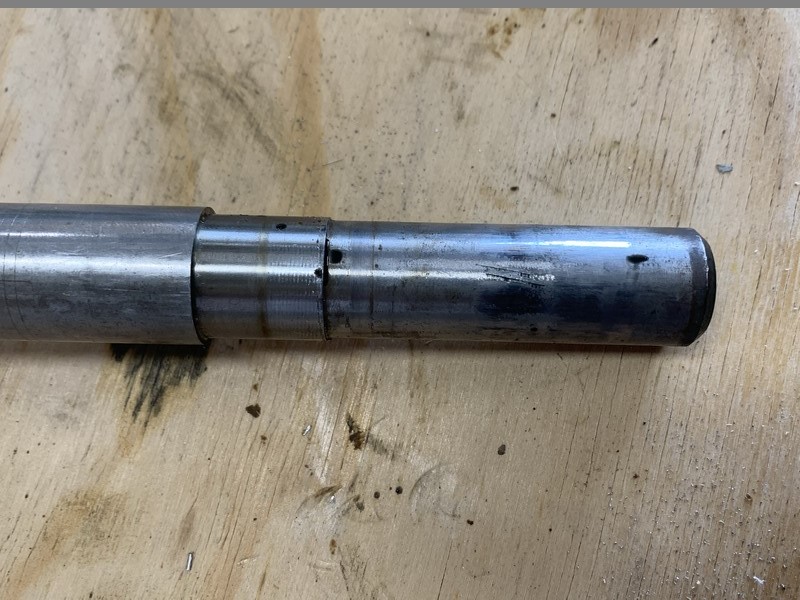 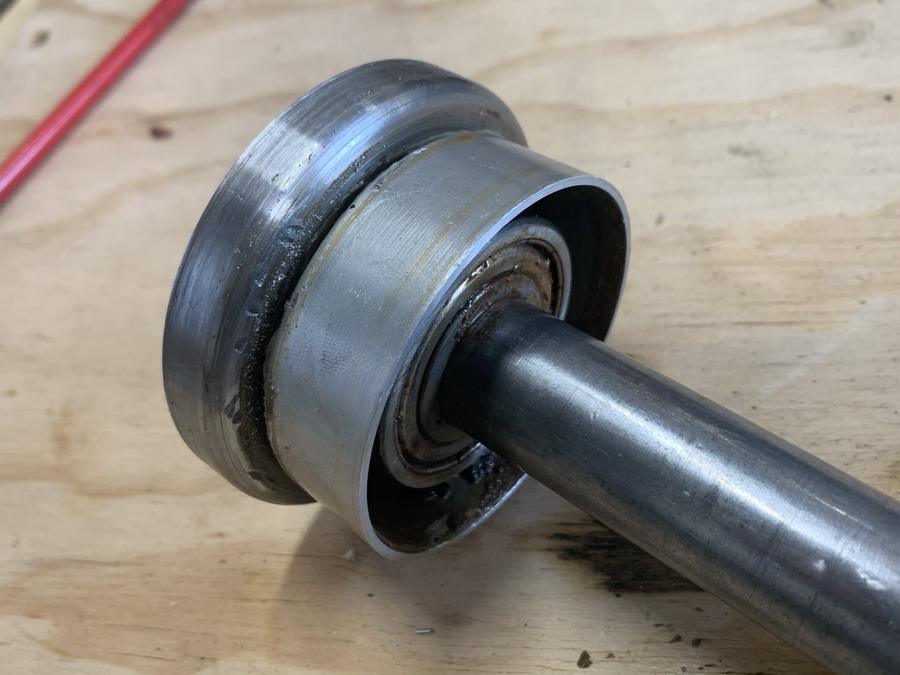 Chuck
|
|
|
Post by oregon on Jun 14, 2020 12:39:02 GMT -5
Will that shield slide right off? it spins freely right now but is trapped between the blade flange and bearing so I cant tell if it is attached or just slipped on. The steps on the shaft look like what AzRockGeek described. Shaft is .875" diameter. I.D. of bearing is .79 (14mm) and then it is turned down to 3/4" on the pulley side and tapped 3/4" on the blade side. 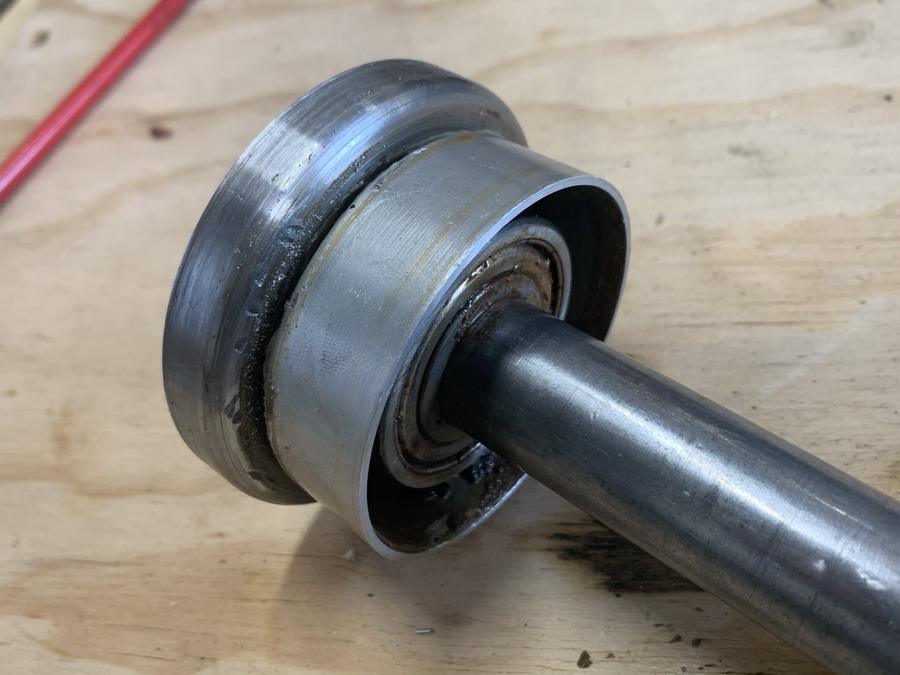 Chuck
So did the flange just press off the shaft?
I have a NOS one of these, are these arbors that valuable? been thinking of using it for a not so serious project but....
|
|
AzRockGeek
has rocks in the head
 
Member since September 2016
Posts: 703
|
Post by AzRockGeek on Jun 14, 2020 14:59:19 GMT -5
So did the flange just press off the shaft?
I have a NOS one of these, are these arbors that valuable? been thinking of using it for a not so serious project but....
I have seen the sell for $40- $100. I think they are more valuable to someone restoring/repairing older equipment, or a lapidary equipment enthusiast like you and me. I have a box full of poly arbors, all the wrong size for what I am looking for. LOL I would like to locate three like this one but with a 5/8-11 thread to make a sphere machine like the old HP sphere machines.
|
|
|
Post by Drummond Island Rocks on Jun 19, 2020 16:52:25 GMT -5
Will that shield slide right off? it spins freely right now but is trapped between the blade flange and bearing so I cant tell if it is attached or just slipped on. The steps on the shaft look like what AzRockGeek described. Shaft is .875" diameter. I.D. of bearing is .79 (14mm) and then it is turned down to 3/4" on the pulley side and tapped 3/4" on the blade side. 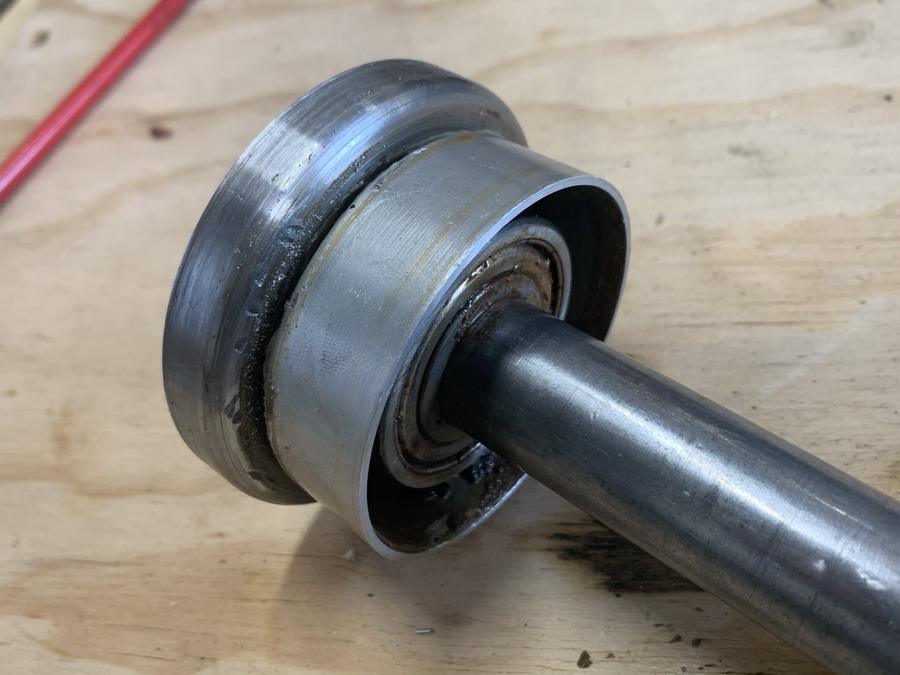 Chuck So did the flange just press off the shaft? I have a NOS one of these, are these arbors that valuable? been thinking of using it for a not so serious project but....
Yes the blade flange was able to be pressed off. The shaft was knurled in that location to form a press fit. After the flange was off the aluminum shield slid off and then last step was to press the remaining bearing off the shaft. It is all back together now and sounds awesome but now I need to address alignment. On my beacon star which has a similar arbor there are features that make it so taking it off and putting it back on does not effect location. This arbor just has the 4 screw holes with clearance so there is a lot of wiggle room to work with. Chuck
|
|