noiefish
off to a rocking start
Member since August 2020
Posts: 20
|
Post by noiefish on Aug 5, 2020 17:22:34 GMT -5
New to all of this. I'm running an older 18" Highland Park. I've have a nice little stack of slabs from river rock, but I keep ending up with a couple inch heel. Maybe I'm being too conservative in where I clamp it, or is there a trick in slabbing the last couple inches? A couple have turned out to be pretty jasper-agate, so I'd love to get the last few slabs.
|
|
|
Post by hummingbirdstones on Aug 5, 2020 18:39:28 GMT -5
Generally in order to slab a heel you will need to glue it to a board that you can clamp in your vice. Then you can slab the heel all the way to the wood.
Do a search on the forum about gluing heels to wood. I know there have been a few recently.
|
|
gemfeller
Cave Dweller
Member since June 2011
Posts: 4,060
|
Post by gemfeller on Aug 5, 2020 18:54:13 GMT -5
I'm doing a bunch of those right now. I use sodium silicate (water glass) as an adhesive because it's water soluble after hardening so the last slab can be freed by soaking it for a day or two. Just let it harden completely before sawing. I give my heels 2 or 3 days to dry completely. depending on their size. I've been using it for years and so far (knock on head) no problems.
Some people use water soluble glue like Elmer's, and others us a variety of adhesives including Gorilla Glue. With the latter the last cut has to be made at the junction of stone and wood.
|
|
|
Post by stardiamond on Aug 5, 2020 18:55:14 GMT -5
I glue my heels to a board and continue to slab. I use water glass because it soaks off. In fact, after cutting a face, I do all my slabbing off a board.
The next question is what to do with the final heel. It depends on the material and what the surface is like. Heels start as a dome. If the heel is thick enough, I trim off the knife edges and draw a shape on the flat side and make a cab.
|
|
noiefish
off to a rocking start
Member since August 2020
Posts: 20
|
Post by noiefish on Aug 5, 2020 20:15:22 GMT -5
Sounds like water glass and wood is the way to go!
|
|
|
Post by opalpyrexia on Aug 5, 2020 20:40:29 GMT -5
Sounds like water glass and wood is the way to go!
Hi, and it is the way to go, but not necessarily just for heels. If you have a rock with a reasonably flat side (or you grind some flat spots on it) and it makes sense to slab parallel to that side, you can still use sodium silicate solution (water glass). The solution is fairly thick, almost like a syrup so it can grab edges and textures.
|
|
|
Post by stardiamond on Aug 5, 2020 21:48:02 GMT -5
Sounds like water glass and wood is the way to go! Hi, and it is the way to go, but not necessarily just for heels. If you have a rock with a reasonably flat side (or you grind some flat spots on it) and it makes sense to slab parallel to that side, you can still use sodium silicate solution (water glass). The solution is fairly thick, almost like a syrup so it can grab edges and textures.
There needs to be enough surface area to adhere the rock to the board. I've had some rocks with multiple content points come off the board when cutting. I like to wait 24 hours between gluing and cutting. The last piece to come off had been sitting for 24 hours. I ground it flatter and reglued.
|
|
|
Post by opalpyrexia on Aug 5, 2020 21:55:44 GMT -5
Hi, and it is the way to go, but not necessarily just for heels. If you have a rock with a reasonably flat side (or you grind some flat spots on it) and it makes sense to slab parallel to that side, you can still use sodium silicate solution (water glass). The solution is fairly thick, almost like a syrup so it can grab edges and textures.
There needs to be enough surface area to adhere the rock to the board. I've had some rocks with multiple content points come off the board when cutting. I like to wait 24 hours between gluing and cutting. The last piece to come off had been sitting for 24 hours. I ground it flatter and reglued.
Yes, it does take some experience to know how flat a side needs to be for a given weight or size.
|
|
|
Post by parfive on Aug 6, 2020 1:00:26 GMT -5
|
|
agatewhisperer
freely admits to licking rocks
 
Member since May 2020
Posts: 836
|
Post by agatewhisperer on Aug 6, 2020 21:56:30 GMT -5
I'm glad you asked this. I'm also pretty new to it and here's a picture of what I've been using. Works ok but need to be careful to get it parallel especially after the rock is tightened down. 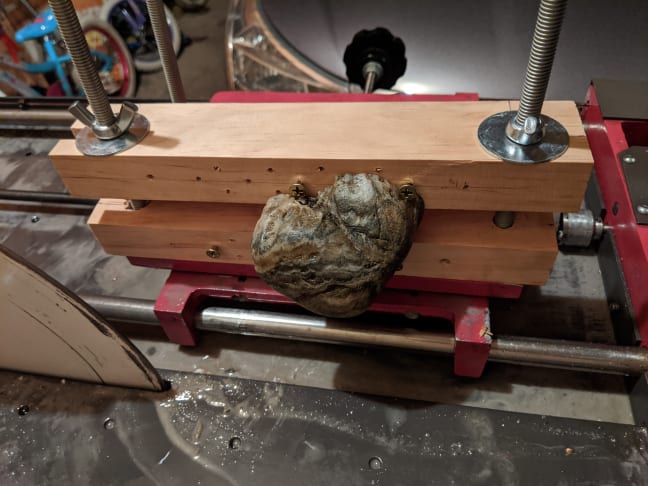
|
|
|
Post by woodman on Aug 8, 2020 9:56:59 GMT -5
I use superglue and cardboard and glue heels to a piece already in the saw. this way all the cuts are parallel with the last cut made on the piece in the saw. no messing around trying to get it lined up with blade. Also no waiting period. can be cutting in minutes, not hours.
|
|
gemfeller
Cave Dweller
Member since June 2011
Posts: 4,060
|
Post by gemfeller on Aug 8, 2020 14:48:08 GMT -5
I use superglue and cardboard and glue heels to a piece already in the saw. this way all the cuts are parallel with the last cut made on the piece in the saw. no messing around trying to get it lined up with blade. Also no waiting period. can be cutting in minutes, not hours. That's very interesting. Does superglue adhere to oily rock surfaces or do they have to be cleaned with solvent? Do you sandwich the cardboard between the heel and the piece in the saw? Not quite clear on how it all comes together.
|
|
|
Post by woodman on Aug 8, 2020 15:33:23 GMT -5
I use superglue and cardboard and glue heels to a piece already in the saw. this way all the cuts are parallel with the last cut made on the piece in the saw. no messing around trying to get it lined up with blade. Also no waiting period. can be cutting in minutes, not hours. That's very interesting. Does superglue adhere to oily rock surfaces or do they have to be cleaned with solvent? Do you sandwich the cardboard between the heel and the piece in the saw? Not quite clear on how it all comes together. The different pieces do HAVE to be clean of oil, I use acetone mostly, sometimes also a degreaser. cut whatever you have in saw. leave it clamped in saw, clean all the oil off, glue cardboard to the piece in saw, then clean the heel and glue it to the cardboard. I do use an accelerator to make the superglue set up real fast. superglue on one part and excellerator on the other, join the pieces and move it around for a second and then hold until it sets up. someplace in the archives there is a post I made showing photos of the process. search for Not for the faint of heart.
|
|
|
Post by woodman on Aug 8, 2020 16:19:01 GMT -5
|
|
|
Post by hummingbirdstones2 on Aug 8, 2020 22:28:59 GMT -5
OK - you got me. Reckon I would've been too cowardly to try that. But if you glued a 38 lb. chunk that way and it didn't fail it's obviously a great method. For perfectly parallel pieces your method is infallible. The photos you post are proof of that.
For everyday slabbing a 4x4 will be close enough for me - if the end is perpendicular to the length. We like to keep at least one slab for cutting cabs, so if the thickness varies end-to-end on the last one it's not a big deal.
The screw-head type slab grabbers were responsible for us getting one of our best pieces of Royal Sahara. Edge broke and trashed the guy's blade. Made him so mad he priced the large last slab low. He didn't want to look at it anymore. We cut eight or nine cabs from it and sold them all... .
|
|
|
Post by woodman on Aug 11, 2020 18:25:24 GMT -5
|
|
|
Post by stardiamond on Aug 12, 2020 12:18:11 GMT -5
I had a small piece of Blue Mountain rough about 2x2x1. I glued it to a board 3 times with water glass and waited 24 hours. It should have held but came off the board. Each time I tried something different. The fourth time, I sprayed shout on the face, used the 280 soft wheel, glued and waited 48 hours. It stayed on the board. Some material really soaks up oil including Blue Mountain and Tahoma. Both stink of oil after being slabbed and cleaned with dish soap and water.
|
|
|
Post by woodman on Aug 19, 2020 20:32:50 GMT -5
I had a small piece of Blue Mountain rough about 2x2x1. I glued it to a board 3 times with water glass and waited 24 hours. It should have held but came off the board. Each time I tried something different. The fourth time, I sprayed shout on the face, used the 280 soft wheel, glued and waited 48 hours. It stayed on the board. Some material really soaks up oil including Blue Mountain and Tahoma. Both stink of oil after being slabbed and cleaned with dish soap and water. I have large kitchen oven and a small toaster oven to cook the oil out. Wife would not let me use the one in our kitchen so had to set them up out in the shop!
|
|
|
Post by knave on Aug 19, 2020 21:17:13 GMT -5
I just tried silicone and it worked good. Sets in a couple of hours. Warm the rock faces with a soft flame to open the pores and dissipate oil.
|
|
|
Post by victor1941 on Aug 20, 2020 20:35:26 GMT -5
I tried the method suggested by Woodman on a thick slab of Carey plume with excellent results. I used sodium silicate and pressed all the pieces together by using a spongy(but firm) foam between the saw tank side and rock. I changed my blade from heavy cutting to a thin blade for this material. I would like to thank Woodman for sharing this method.
|
|