|
Post by holajonathan on Sept 16, 2021 11:20:02 GMT -5
I've got some large RIJ nodules that I've been scared to slab because I spent too much money on them, they have the potential to be amazing, and I have sometimes had troubles slabbing RIJ.
Part of the problem I run into is that the nodules are covered in a soft chalky crust. As a result, I have no way of knowing how to clamp the nodule into the saw vise so that the blade hits the jasper at a 90 degree angle. I have chipped corners off RIJ slabs, and cut slabs with excessive saw marks, when the blade ended up hitting the jasper at a narrow angle and the blade struggled to straighten itself out in the cut, if that makes sense.
Anyone have any advice on slabbing large nodules of this stuff? I think I've got 2 or 3 nodules that are in the 2-4 pound range, and a couple more that are around a pound each. The biggest one will cut some 8" x 4" slabs if I cut parallel to the largest face, which is the high-risk / high (potential) reward way of cutting them. All are huge compared to all of the RIJ I have bought before. Together with Condor agates, these are the most expensive rocks I have bought, which is part of the reason I haven't found the courage to clamp them in my slab saw and let-'er-rip.
|
|
|
Post by HankRocks on Sept 16, 2021 17:05:49 GMT -5
One way might be to split the nodule using a clamp I bought from Ebay. The clamp hold a roundish rock pretty well and once split, glue the halves to wood the finish the slabbing. I don't think it will cut as big a geode as advertised. www.ebay.com/itm/233788491157It works pretty well except that it does not fit every saw and I needed to keep track of where the cut is or else it starts cutting the steel. I had to raise it up in the vise to get a longer cut. Also have a custom built for the 20 inch saw by a good friend, geode holder that does pretty well, just has a size limit the the ebay device helps with. He in the process of designing and building one for the 24 inch saw which will cut larger geodes(rounds) Clamping rocks properly is always a challenge. I have a couple that have defied me and they are set aside until I get an inspiration.
|
|
|
Post by holajonathan on Sept 16, 2021 20:20:53 GMT -5
Thanks to both of you. The two real big ones are, of course, oddly shaped, which is part of the problem. And my desire to cut slabs with the largest face possible limits the options for clamping them in the vise. I am going to buy that clamp off ebay. I am sick of struggling with big Brazilian agates, and using something like that to cut them in half would be a good first step. I will be interested to see if it will hold roundish rocks off center. With Brazilians, my favorite part is usually the outside 1/2" to 1" of the stone because the matrix often caused cool designs when the agates started forming. It would be nice to be able to slab off all the sides. I don't think that will be possible, but I will experiment. Slabbing rocks is one of my favorite activities, and yet, fighting to get them clamped into the vise securely is a constant, frustrating struggle. Hopefully that clamp is a good addition to my arsenal of wedges and slab grabbers.
|
|
|
Post by HankRocks on Sept 16, 2021 21:04:56 GMT -5
Thanks to both of you. The two real big ones are, of course, oddly shaped, which is part of the problem. And my desire to cut slabs with the largest face possible limits the options for clamping them in the vise. I am going to buy that clamp off ebay. I am sick of struggling with big Brazilian agates, and using something like that to cut them in half would be a good first step. I will be interested to see if it will hold roundish rocks off center. With Brazilians, my favorite part is usually the outside 1/2" to 1" of the stone because the matrix often caused cool designs when the agates started forming. It would be nice to be able to slab off all the sides. I don't think that will be possible, but I will experiment. Slabbing rocks is one of my favorite activities, and yet, fighting to get them clamped into the vise securely is a constant, frustrating struggle. Hopefully that clamp is a good addition to my arsenal of wedges and slab grabbers. What size saw do you have? On my 20 inch if I just mount the device in the vice, it would run into the blade eventually. I put blocks under it in the vice to raise it up and give a longer cut. The 20 inch does not have an auto stop so I have to watch it. Moved the clamp empty until it hit the blade, then used a yellow tie wrap to mark the chain. The chain should be connected to the switch so that it does stop after a certain distance. The switch on mine is installed the wrong way to get turned off by the chain, I need to fix it. Hey it's on the list!!! The custom made geode holder I have is built to fit the 20 inch and the metal bridge moves over the blade safely.
|
|
|
Post by holajonathan on Sept 17, 2021 0:35:43 GMT -5
@hankrocks I bought that clamp. I am mostly using a 14" slab saw at the moment. I also have a 10" slab saw and an 18" slab saw that I will have running again shortly.... Other than slab saws, I've a 16" MK Diamond drop saw, a 10" high speed lapidary trim saw, two 6" lapidary trim saws, a 10" tile saw, a 6" tile saw, a 4-1/2" tile saw, and one of these, although I've yet to figure out a good lapidary use for it. 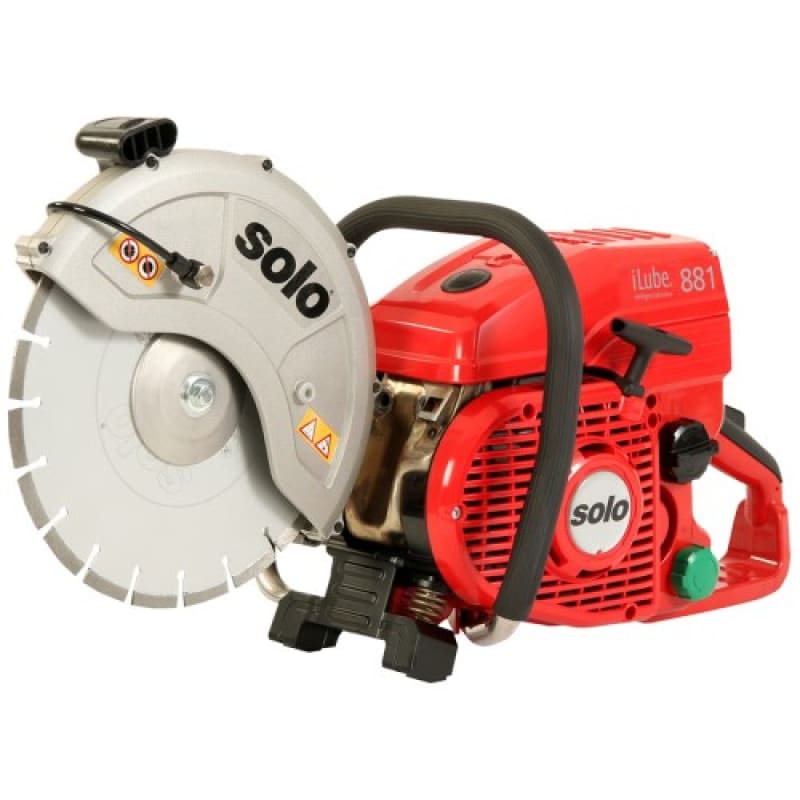 All of my slab saws have auto stop, so if I set it just right, is shouldn't be a problem. I get your idea about raising it up, so that is something else to try if needed. I bet I can figure out a good way to use that clamp with my drop saw as well. Would be a fast way to cut rock in half since it has a huge 2 h.p. Baldor motor on it and eats through rocks when set up with a good tile blade.
|
|
|
Post by Rockindad on Sept 17, 2021 6:16:21 GMT -5
@hankrocks I bought that clamp. I am mostly using a 14" slab saw at the moment. I also have a 10" slab saw and an 18" slab saw that I will have running again shortly.... Other than slab saws, I've a 16" MK Diamond drop saw, a 10" high speed lapidary trim saw, two 6" lapidary trim saws, a 10" tile saw, a 6" tile saw, a 4-1/2" tile saw, and one of these, although I've yet to figure out a good lapidary use for it. 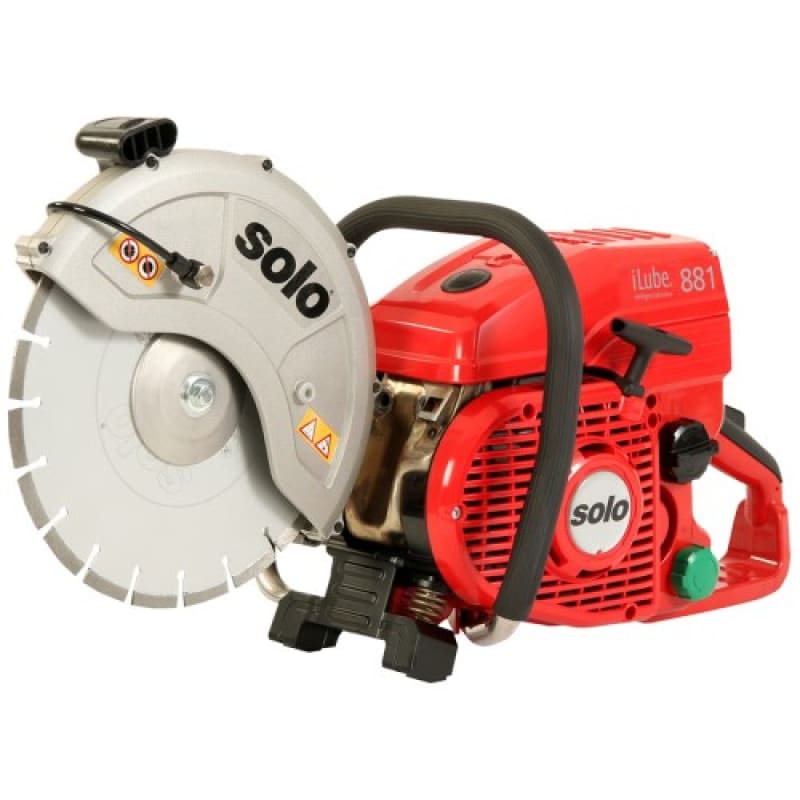 All of my slab saws have auto stop, so if I set it just right, is shouldn't be a problem. I get your idea about raising it up, so that is something else to try if needed. I bet I can figure out a good way to use that clamp with my drop saw as well. Would be a fast way to cut rock in half since it has a huge 2 h.p. Baldor motor on it and eats through rocks when set up with a good tile blade. Whether you would consider it “good” I do not know but I have used a wet cutoff saw like you have pictured to break down larger material. Very efficient and would save wear and tear on your lapidary saws/oil. I only used it for rough cuts/get a flat side and to get material small enough to get into the saw. Definitely need to pay attention to securing the piece being cut.
|
|
|
Post by holajonathan on Sept 17, 2021 10:15:01 GMT -5
Rockindad I might just try that. I have a few rocks that are way too large to fit into any of my slab saws, including a 40 pound chunk of Maligano jasper, a 50 pound chunk of Graveyard Point Plume agate, and a chunk of Australian lace agate that is shaped like a USPS large flat rate box. Maybe I could use a couple ratchet straps to secure the rocks to a big piece of wood, with a strap on each side of the cut. If I cut through the rock and into the wood that won't hurt the saw. I have also thought about partially buying the rough in a hole filled with crushed limestone and plunge cutting the rock that way. I need to either find it a lapidary use or find it a new home. 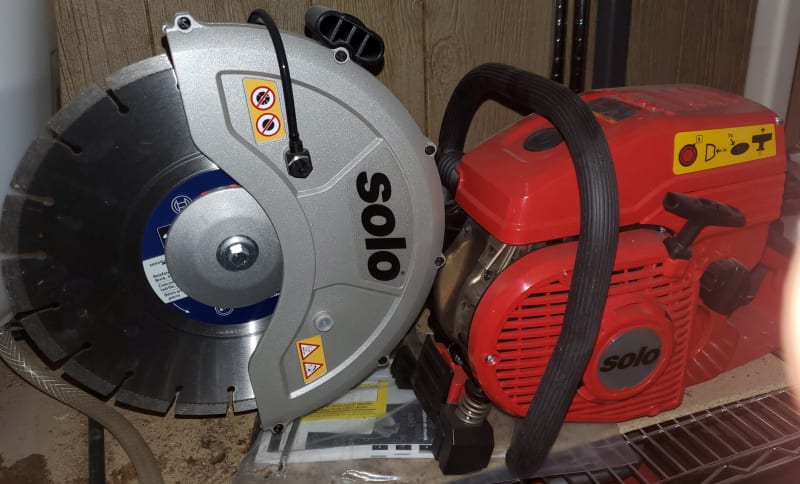
|
|
|
Post by holajonathan on Sept 17, 2021 10:29:51 GMT -5
I could install one of these 0.312 thick blades on the gas saw (my Ebay listing) and use the edge of the blade to grind / pre-shape big rocks.  How long would it take me to lose at least one finger?
|
|
|
Post by Rockindad on Sept 17, 2021 17:21:08 GMT -5
I could install one of these 0.312 thick blades on the gas saw (my Ebay listing) and use the edge of the blade to grind / pre-shape big rocks.  How long would it take me to lose at least one finger? You could do the lapidary version of this: I've watched a few demonstrations of this (not this particular guy) in person, pretty amazing. As far as securing a large piece I started with a piece of 3/4 plywood. I placed the stone on it and screwed some scrap 2x4's around the piece to create a cradle so it could not slide around, I left an opening where the cut(s) were going to be. I drilled four 2" holes (2 on each side of the cut) and ran a couple of ratchet straps through the platform and around the rock on each side of the cut, rocks weren't going anywhere.
|
|
rewdownunder
spending too much on rocks

Member since March 2012
Posts: 357
|
Post by rewdownunder on Sept 18, 2021 13:12:59 GMT -5
A dealer friend of mine would save up all his very large rough and rent one of these saws from Home Depot for a day. He said it was cheaper than killing the blades on his big saws. You could cut things fast because you were not concerned about the blade. He would make a cradle out of wood as described or set the rock in concrete a few days ahead of time. An old school way of cutting nodules right where you wanted them cut was to set them in plaster or fiber glass so they fit in the vice in the correct direction. I saw this done at Colorado School of Mines in the 1980s for a display of geodes the were doing. Our club has a geode clamp with the three arms that works well because you can set the rock on a table and lock the clamp to it then put the whole thing into the saw.
|
|
|
Post by holajonathan on Oct 3, 2021 11:53:54 GMT -5
@jadedvision HankRocks I finally found the bravery and patience to start slabbing my large royal imperial jasper nodules. They were larger than I remembered -- 5-6 pounds each and oddly shaped. The way I had to position them in the vise, most of the rock was sitting on the carriage and only about an inch was hanging off the carriage. So I could only get 2 or 3 slabs from each rock. At this point I am going to glue them to 2x4's to finish slabbing. Both rocks have some potential. The first would be amazing if not for the green bands, which are all too common in these rocks. I could have tried to slab it parallel to the green bands, which were visible on the rock exterior. But since the bands are not exactly straight or parallel, that would have been easier said than done. The hole in the center seems to be closing up as I cut into the rock. The largest slab is about 4"x5" 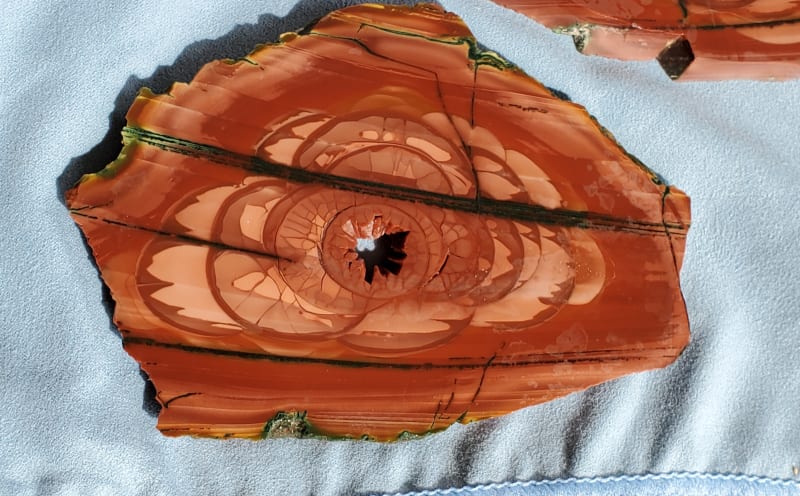 I am more excited about this one. I have only cut about 1" into it the rock and there is about 4" to go. I am hoping for more eggs and that the orange area takes over the soft white part. This one is big, about 7-1/2" x 3-1/2" 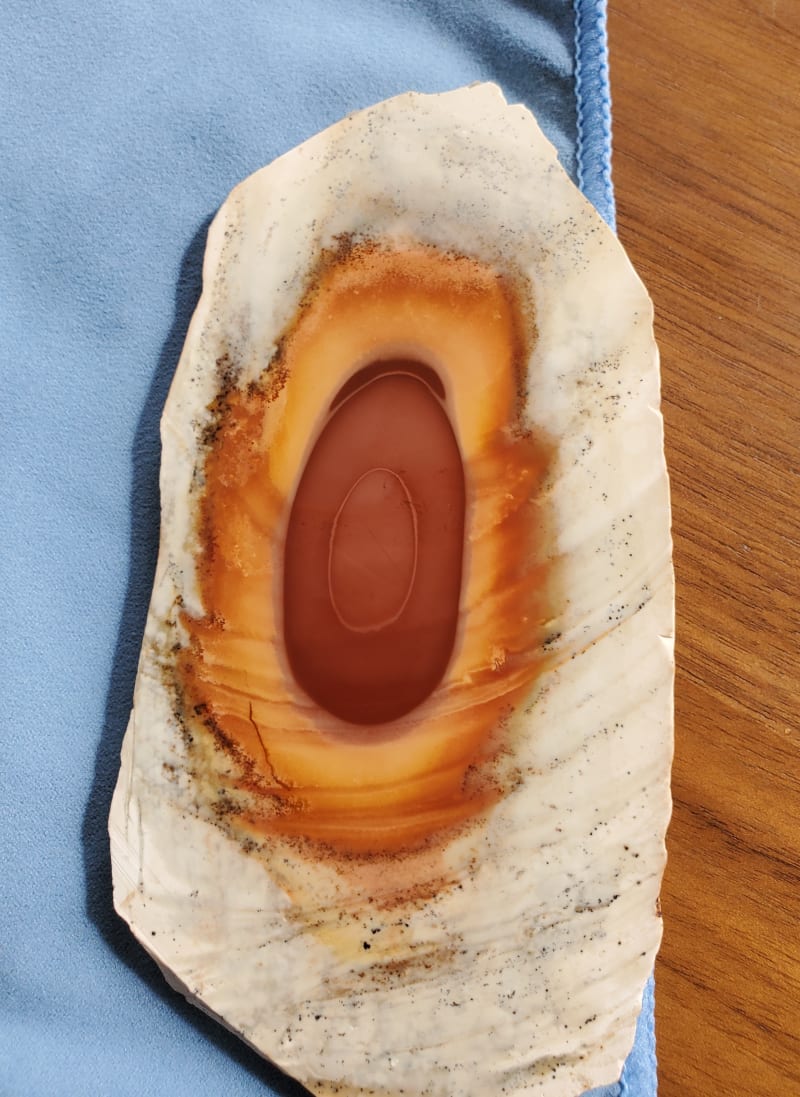
|
|
|
Post by jasoninsd on Oct 3, 2021 16:21:33 GMT -5
Wow Jonathan! That first one has some seriously cool patterns going on in it! I'll be curious to see how the second "egg" turns out the further you get into the rock. 
|
|
|
Post by holajonathan on Oct 3, 2021 19:13:47 GMT -5
Wow Jonathan! That first one has some seriously cool patterns going on in it! I'll be curious to see how the second "egg" turns out the further you get into the rock.  The first one is going to be made into a whole bunch of long, skinny cabs, I suppose, in order to work around the green stripes. I am excited about the second one as well. Slabbing these is quite a cliff hanger.
|
|
|
Post by jasoninsd on Oct 3, 2021 20:03:28 GMT -5
Wow Jonathan! That first one has some seriously cool patterns going on in it! I'll be curious to see how the second "egg" turns out the further you get into the rock.  The first one is going to be made into a whole bunch of long, skinny cabs, I suppose, in order to work around the green stripes. I am excited about the second one as well. Slabbing these is quite a cliff hanger. 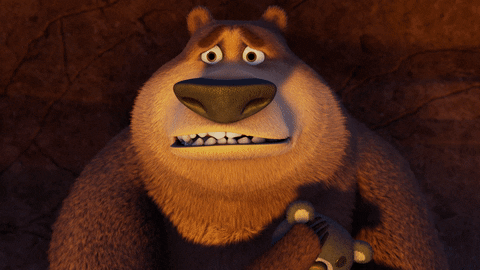
|
|
|
Post by catmandewe on Oct 3, 2021 20:34:44 GMT -5
Oh I would love to slab some of those just for the fun of it!
|
|
|
Post by holajonathan on Oct 4, 2021 2:36:51 GMT -5
Oh I would love to slab some of those just for the fun of it! If I get ahold of some more real big ones I'll trade you one or two for something special out of your secret stash of northwest porcelain jaspers. I get the sense you've been hounding rocks long enough to have tucked some away on par with these Mexican nodules. The two I am cutting now were the largest out of a 700 pound lot from Mexico. I have seen a little bigger, but not very often in the nodular imperial jasper.
|
|
|
Post by holajonathan on Oct 4, 2021 2:37:28 GMT -5
The first one is going to be made into a whole bunch of long, skinny cabs, I suppose, in order to work around the green stripes. I am excited about the second one as well. Slabbing these is quite a cliff hanger. 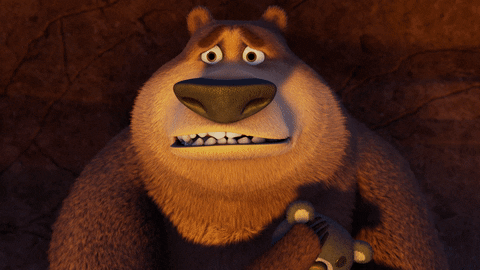 Exactly.
|
|
|
Post by Peruano on Oct 4, 2021 17:01:46 GMT -5
I'm not sure why you expect the blade to slide when it addresses a curved vs perpendicular face of the rock at the start of the cut. Yes. I know it can happen and the traditional way to to avoid deflection is to let the blade contact just a brief period then stop and pull back and let it come back again. However, it seems to me that if your sled (vice) speed of advancing toward the blade is slow enough your blade should make its own working groove without being pushed aside by any nonperpendicular surface. So . . . my question is. Are you using the slowest speed for your feed mechanism. I have a 14" HP with an MK303 blade that I use the slowest of three speed options on. I have an ancient 12" with a very old blade which you might expect to balk at a curve surface; and I have an old Covington 20" with a belt driven feed (no separate motor) and I have no problems feeding them a curved initial surface. I've always assumed that the brief cut of a notch and then restarting the cut would do it if I did (in point of fact I do this always when hand feeding my trim saw}. Does any of this make sense??
|
|
|
Post by holajonathan on Oct 4, 2021 23:43:35 GMT -5
I'm not sure why you expect the blade to slide when it addresses a curved vs perpendicular face of the rock at the start of the cut. Yes. I know it can happen and the traditional way to to avoid deflection is to let the blade contact just a brief period then stop and pull back and let it come back again. However, it seems to me that if your sled (vice) speed of advancing toward the blade is slow enough your blade should make its own working groove without being pushed aside by any nonperpendicular surface. So . . . my question is. Are you using the slowest speed for your feed mechanism. I have a 14" HP with an MK303 blade that I use the slowest of three speed options on. I have an ancient 12" with a very old blade which you might expect to balk at a curve surface; and I have an old Covington 20" with a belt driven feed (no separate motor) and I have no problems feeding them a curved initial surface. I've always assumed that the brief cut of a notch and then restarting the cut would do it if I did (in point of fact I do this always when hand feeding my trim saw}. Does any of this make sense?? Yes, it all makes sense. My slab saws use a motor to turn the feed screw so there is just one speed -- about 3/16" per minute. I believe that this is roughly equivalent to the slow speed on saws with belt drive feeds with three pulley slots. If there was a way to adjust the speed I would love to know, as I get impatient slabbing large chunks of obsidian that could definitely be fed faster if I had the option. I agree with your logic -- a slow feed speed will allow the blade to straighten itself out rather quickly since the blade core is stiff steel. Centrifugal force comes into play as well to help the blade self-center despite initial deflection. Ideally, the blade will self-center within the first 1/4" or so of the cut. The diamonds on the sides of the blade are what allow the blade to grind its way back to a centered position. If the centering does not happen quickly enough, the blade can no longer self center once the blade has cut to a depth greater than the height of the diamond segment. Blade that have diamond segments significantly wider thn the core of the blade do allow for some additional centering of the blade, but the MK diamond blades I use have steel cores that are only slightly narrower than the cutting edge, so pretty much a self centering must occur before the blade has advanced into the rock beyond the diamond segment or rim. So that's the theory, but here's my experience. When I use a wide kerf blade, like a 0.110" kerf on a 14" saw, I can run the rock into the blade at pretty much any angle and it cuts just fine, exactly as you have described. Because I hate cleaning saw oil and a wide kerf eats up a lot of rock, I have been using MK Diamond blades with a 0.065" kerf. The blades make very clean cuts and last a long time, but they are not nearly as stiff as wider blades, and I believe that the core is only 0.01" narrower than the rim. Nevertheless, everything still works as you have described UNLESS something is out of adjustment on the carriage or feed mechanism. After I cut with my brand new slab saw for about 50 hours, many things related to the carriage and feed mechanism needed tightening. I consider this normal break in maintenance. Unfortunately, HP does not offer a manual or any specific advice about what to adjust or when to do it, and as a first-time slab saw owner, I was not aware of all of the points of adjustment. The first thing that needed adjusting was the gap between the carriage bearings and the rails. If the bearings are not kept very snug (but not too snug) to the rails, the carriage can be pushed up and to the side slightly when the rock comes into contact with the blade at an oblique angle. That amplifies the initial deflection, making it much harder for the blade to recover and self center. That is exactly what happened to me within the first few months of me owning my 14" saw. I was trying to cut at an oblique angle and the blade did not auto-center quickly enough. As the autofeed advanced, it continued to deflect the blade until the blade was pushed into the metal "shelf" that runs from behind the blade to the front of the saw. Eventually, the advancing rock severely warped the blade, which was pinned between the rock and the steel inside the saw. I ruined a $200 blade. I also had to replace the v-belt and the drive pulley on the motor, which had becomes glazed over from spinning against a stalled belt. I am lucky that I did not burn up the motor as was extremely hot as well, although the the motor's thermal protection circuit was never tripped. I don't want to turn this into a novel, so I will just briefly say that I recently had a similar problem before making adjustments to the drive screw bearings and the split nut mechanism to keep everything very tight. I didn't ruin a blade this time, but I was experiencing other problems when trying to cut at an oblique angle. When everything is tight and properly adjusted my saws cut perfectly smooth, even thickness slabs every time. The angle that the blade hits the rock does not seem to matter much. But given my expensive learning experience, and the fact that I am not constantly inspecting the carriage / bearing / drive screw / split nut tightness, I am now gun shy about cutting outside of the 80-100 degree or so range. My expensive, blade-destroying learning experience was with a huge chunk of polish flint. The rock was right at the limit of what my 14" saw can cut, and chert is a very hard rock. Harder than most agates and jaspers, with the exception of things like Montana and Brazilian agates, which are also fairly pure chalcedony.
|
|
|
Post by holajonathan on Oct 4, 2021 23:47:33 GMT -5
I'm not sure why you expect the blade to slide when it addresses a curved vs perpendicular face of the rock at the start of the cut. Yes. I know it can happen and the traditional way to to avoid deflection is to let the blade contact just a brief period then stop and pull back and let it come back again. However, it seems to me that if your sled (vice) speed of advancing toward the blade is slow enough your blade should make its own working groove without being pushed aside by any nonperpendicular surface. So . . . my question is. Are you using the slowest speed for your feed mechanism. I have a 14" HP with an MK303 blade that I use the slowest of three speed options on. I have an ancient 12" with a very old blade which you might expect to balk at a curve surface; and I have an old Covington 20" with a belt driven feed (no separate motor) and I have no problems feeding them a curved initial surface. I've always assumed that the brief cut of a notch and then restarting the cut would do it if I did (in point of fact I do this always when hand feeding my trim saw}. Does any of this make sense?? Yes, it all makes sense. My slab saws use a motor to turn the feed screw so there is just one speed -- about 3/16" per minute. I believe that this is roughly equivalent to the slow speed on saws with belt drive feeds with three pulley slots. If there was a way to adjust the speed I would love to know, as I get impatient slabbing large chunks of obsidian that could definitely be fed faster if I had the option. I agree with your logic -- a slow feed speed will allow the blade to straighten itself out rather quickly since the blade core is stiff steel. Centrifugal force comes into play as well to help the blade self-center despite initial deflection. Ideally, the blade will self-center within the first 1/4" or so of the cut. The diamonds on the sides of the blade are what allow the blade to grind its way back to a centered position. If the centering does not happen quickly enough, the blade can no longer self center once the blade has cut to a depth greater than the height of the diamond segment. Blade that have diamond segments significantly wider thn the core of the blade do allow for some additional centering of the blade, but the MK diamond blades I use have steel cores that are only slightly narrower than the cutting edge, so pretty much a self centering must occur before the blade has advanced into the rock beyond the diamond segment or rim. So that's the theory, but here's my experience. When I use a wide kerf blade, like a 0.110" kerf on a 14" saw, I can run the rock into the blade at pretty much any angle and it cuts just fine, exactly as you have described. Because I hate cleaning saw oil and a wide kerf eats up a lot of rock, I have been using MK Diamond blades with a 0.065" kerf. The blades make very clean cuts and last a long time, but they are not nearly as stiff as wider blades, and I believe that the core is only 0.01" narrower than the rim. Nevertheless, everything still works as you have described UNLESS something is out of adjustment on the carriage or feed mechanism. After I cut with my brand new slab saw for about 50 hours, many things related to the carriage and feed mechanism needed tightening. I consider this normal break in maintenance. Unfortunately, HP does not offer a manual or any specific advice about what to adjust or when to do it, and as a first-time slab saw owner, I was not aware of all of the points of adjustment. The first thing that needed adjusting was the gap between the carriage bearings and the rails. If the bearings are not kept very snug (but not too snug) to the rails, the carriage can be pushed up and to the side slightly when the rock comes into contact with the blade at an oblique angle. That amplifies the initial deflection, making it much harder for the blade to recover and self center. That is exactly what happened to me within the first few months of me owning my 14" saw. I was trying to cut at an oblique angle and the blade did not auto-center quickly enough. As the autofeed advanced, it continued to deflect the blade until the blade was pushed into the metal "shelf" that runs from behind the blade to the front of the saw. Eventually, the advancing rock severely warped the blade, which was pinned between the rock and the steel inside the saw. I ruined a $200 blade. I also had to replace the v-belt and the drive pulley on the motor, which had becomes glazed over from spinning against a stalled belt. I am lucky that I did not burn up the motor as was extremely hot as well, although the the motor's thermal protection circuit was never tripped. I don't want to turn this into a novel, so I will just briefly say that I recently had a similar problem before making adjustments to the drive screw bearings and the split nut mechanism to keep everything very tight. I didn't ruin a blade this time, but I was experiencing other problems when trying to cut at an oblique angle. When everything is tight and properly adjusted my saws cut perfectly smooth, even thickness slabs every time. The angle that the blade hits the rock does not seem to matter much. But given my expensive learning experience, and the fact that I am not constantly inspecting the carriage / bearing / drive screw / split nut tightness, I am now gun shy about cutting outside of the 80-100 degree or so range. My expensive, blade-destroying learning experience was with a huge chunk of polish flint. The rock was right at the limit of what my 14" saw can cut, and chert is a very hard rock. Harder than most agates and jaspers, with the exception of things like Montana and Brazilian agates, which are also fairly pure chalcedony. To your other point, I have not tried briefly cutting the notch and resetting, although as you mention, I do not frequently with trim saws, especially since I have been using a 6" x 0.014" MK trim saw blade which has no stiffness whatsoever. The thin trim saw blade takes a bit of coddling and patience, but it makes extremely precise and clean cuts, allowing me to squeeze and extra cab out of slabs of high grade or expensive material.
|
|