rocknewb101
fully equipped rock polisher
 
Member since October 2022
Posts: 1,368
|
Post by rocknewb101 on Feb 20, 2023 9:51:30 GMT -5
I spent about 5-6 hours in the basement Sunday working on the below. I'm mostly happy with the dome shape, although I know the girdle (I think I'm using the correct terms here, but please correct me if I'm wrong) is all wonky and I see some chips and major scratching. My biggest struggle is getting all of the scratches out. I've watched videos, perused this site and I can't seem to find anywhere that really tells/shows me anything about getting scratches out - once I'm at the 600 wheel I don't think anything changes, but I'm afraid if I spend too much time on the 80 or 180 diamond I'll grind away the shape - should I be seeing scratches from stage to stage, or do I stay on each stage until scratches are gone???. Anyways, these two are courtesy of realrockhound who sent me some bags of slabs of excess sawed material - the first and second is one that already had the template drawn on it so I cut it and worked with it, the third was a thin slab of something mossy or plumy - I've chipped away a part accidently as it was quite thin, but the same with the scratches here... Thanks again realrockhound for sending these along - what fun I'm having learning!! 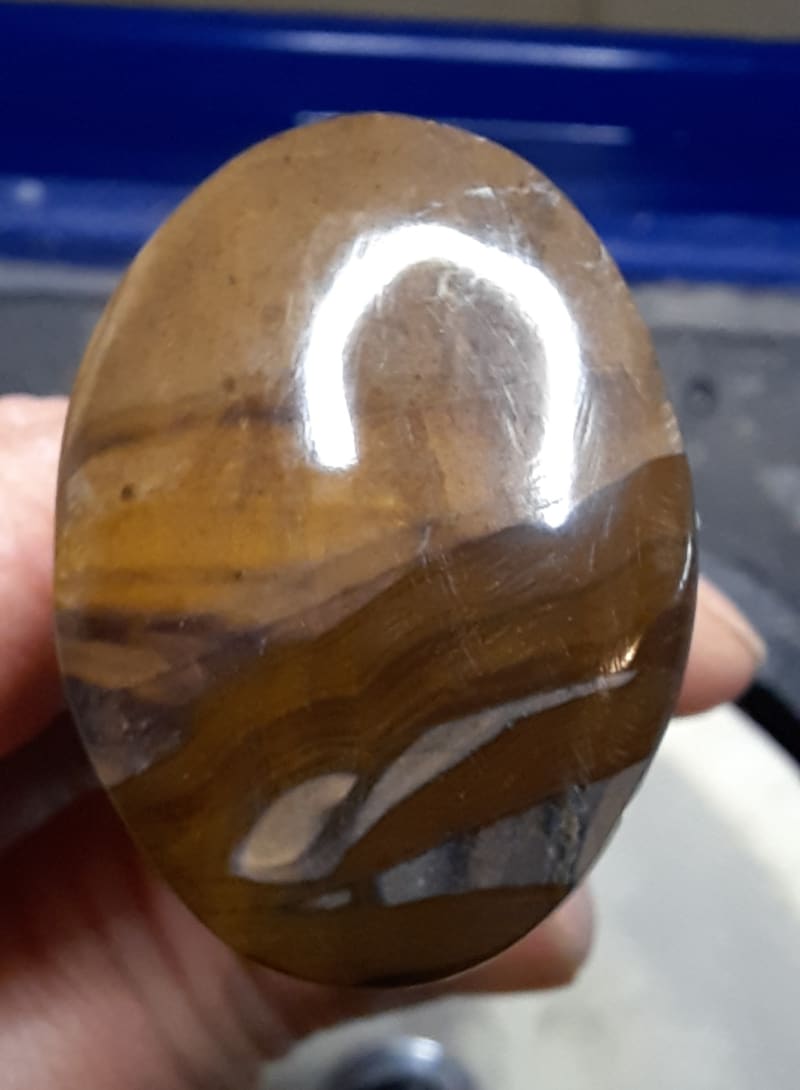 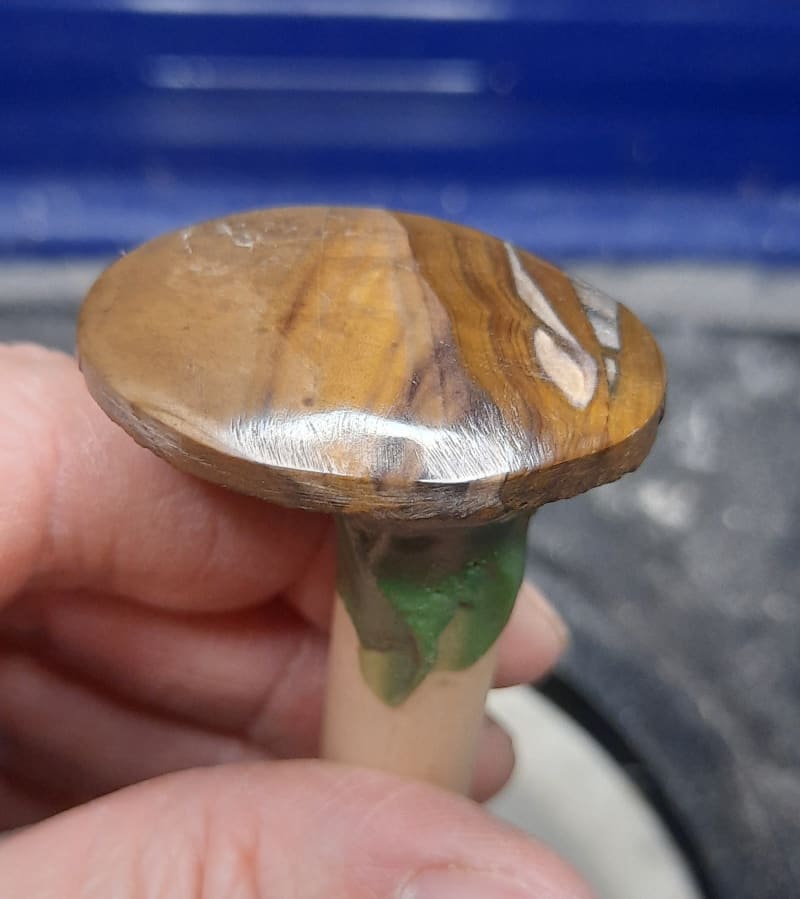 jasoninsd - I was going to message you separately for any guidance you can offer, but then thought maybe others starting out could benefit from the same info - When you worked on the slant cab, how long approx. on each wheel before you were happy with moving along? do I need to grind/smooth until no scratches show before moving on? Or maybe just need more time on a particular wheel? Thanks!!
|
|
dshanpnw
fully equipped rock polisher
 
Member since December 2020
Posts: 1,160
|
Post by dshanpnw on Feb 20, 2023 10:08:19 GMT -5
Really nice effort and nice cabs. I'm not the expert at all, but I do know about scratches and ruining the shapes trying to get them out. I don't go past the 280 wheel until I have all the scratches gone. Depending on the hardness or toughness of the stone I will stay on the 220 wheel until they are gone unless it is a softer stone and I know the 280 wheel will remove them. It definitely took me many many cabs and hours to figuring out how to get the scratches out. I'm just now getting better at it. Sometimes I get to the 3000 wheel only to go back to 220, it happens a lot. Also, sometimes softer stones can be very difficult for the reason you stated, you could lose the shape trying to get a dome. That happens to me quite often too. Light pressure on the 220 wheel is a good technique. Actually, light pressure when necessary is a good technique. Jason will guide you right.
|
|
gunsil
spending too much on rocks

Member since January 2023
Posts: 345
|
Post by gunsil on Feb 20, 2023 10:23:00 GMT -5
Yup, that's definitely old Biggs picture jasper. I use a different grit set up myself since I have both an expando drum machine and a Titan. I go from my 120 sintered hard wheel to 220 belt then a 400 belt before going to the Titan and progressing from 600 to 14,000. I need to see all hard wheel scratches gone by the 400 before I get to the 600, you're correct that 600 and up do little scratch removal. If using a typical modern set up where you go from 280 to 600 any hard wheel scratches must be gone when done on the 280. Your girdles look dang good to me although I don't often use them, just rounding the side up from the flat bottom. As a jeweler I find it easy to set with or without a girdle, and small stones aren't usually girdled.
|
|
rocknewb101
fully equipped rock polisher
 
Member since October 2022
Posts: 1,368
|
Post by rocknewb101 on Feb 20, 2023 10:42:20 GMT -5
Really nice effort and nice cabs. I'm not the expert at all, but I do know about scratches and ruining the shapes trying to get them out. I don't go past the 280 wheel until I have all the scratches gone. Depending on the hardness or toughness of the stone I will stay on the 220 wheel until they are gone unless it is a softer stone and I know the 280 wheel will remove them. It definitely took me many many cabs and hours to figuring out how to get the scratches out. I'm just now getting better at it. Sometimes I get to the 3000 wheel only to go back to 220, it happens a lot. Also, sometimes softer stones can be very difficult for the reason you stated, you could lose the shape trying to get a dome. That happens to me quite often too. Light pressure on the 220 wheel is a good technique. Actually, light pressure when necessary is a good technique. Jason will guide you right. dshanpnw - this is very helpful! Thank you! I have the 80 and 180 diamond wheel, then jumps to 325 smoothing - thinking I might add a 280 diamond to get a little finer sanding. I was probably grinding too hard too, so I'll lighten up my touch. Thank you!!! (Can't wait to get home from work now lol)...
|
|
rocknewb101
fully equipped rock polisher
 
Member since October 2022
Posts: 1,368
|
Post by rocknewb101 on Feb 20, 2023 10:44:45 GMT -5
Yup, that's definitely old Biggs picture jasper. I use a different grit set up myself since I have both an expando drum machine and a Titan. I go from my 120 sintered hard wheel to 220 belt then a 400 belt before going to the Titan and progressing from 600 to 14,000. I need to see all hard wheel scratches gone by the 400 before I get to the 600, you're correct that 600 and up do little scratch removal. If using a typical modern set up where you go from 280 to 600 any hard wheel scratches must be gone when done on the 280. Your girdles look dang good to me although I don't often use them, just rounding the side up from the flat bottom. As a jeweler I find it easy to set with or without a girdle, and small stones aren't usually girdled. Thanks so much gunsil! I appreciate your knowledge! Knowing that I need to work more on the lower wheels is very helpful! I think I'll definitely purchase one step higher than the 180 to help with that. Thanks again!
|
|
|
Post by jasoninsd on Feb 20, 2023 12:06:31 GMT -5
Hey Peta! Thanks for the tag!  Here's some tough love. You do NOT need a 280 hard disk or soft disk. How was that for tough? LOL It looks to me like those deep scratches are from the 80 grit disk. I know you're concerned about losing your shape if you go back to the hard disks...but you need to go back to the 180 and figure out how to use a "light" touch...so you're smoothing, rather than grinding. When it comes to the hard disks (or wheels) I believe there's two ways to use them: 1) Grinding - which is used to remove large quantities (relatively speaking) of material and uses a heavier amount of pressure against the disk/wheel...and 2) Smoothing - which uses a VERY light touch against the disk/wheel and is used to help with the final shaping and remove "flat" spots. Before I move off the initial wheel (80 grit) I run the cab over the surface lightly to make sure I've smoothed it as much as possible before moving onto the second hard wheel (disk). If I've done that correctly, then all I need to do with the 180 disk is "smooth" out the surface trying to get the scratches out from the 80. One of your issues you're going to have is that you don't have foam backing on the sanding disks...if I remember correctly. Which means you're going to have to use very little pressure on the 325 and above...otherwise you're going to create flat spots as you go through the stages. If you had the foam backing, pressure could be increased as the foam allows the disk to compress and create a circular indent which allows the surface of the disk to conform to shape of the dome of the cab. There is no amount of linear "time" which can be assigned to the work required on each stage. I can't say it'll take 5 minutes, or 40 minutes. Well...in fairness, if you're spending 40 minutes on one stage, you need to go back a step as that's a bit too long in my opinion. LOL - Some material it might take me 10 minutes on a stage. It all boils down to how well I shaped my dome on the 80...and how smooth I got it on the 180 (220 in my case). The first "soft" is where you'll likely be spending the most of your time. This may very well take 20+ minutes! A couple things I'll point out. I don't see a girdle line. I know some people swear by NOT using a girdle line...but in my opinion for someone just starting out, it's invaluable. It gives you a visual "DO NOT CROSS" line when shaping your dome. And two...you're either not using enough magnification when looking at the stone after each step, or there's not enough light. Those "deep" scratches should have been very visible through an Optivisor...and you would have known not to progress past the 180...or 325. I work my girdle last...after the cab has been domed and worked all the way through the 3000. When I cut out my preforms, I always work the edges of the preform before I put them on dop...and before I start doming. I make sure the shape is exactly what I want coming off the 80 or 180 hard disks. IF I've gotten all the scratches from the 80 off with the 180, when it comes time to work the girdle, I know I don't have to go back to the 180 and potentially mess up the girdle where it meets the dome. I can see on yours, there's deep scratches from the 80 on the girdle...which means you're going to alter the shape of the cab trying to get those scratches out with the 180. Please don't get discouraged. It's an absolute learning process. From the looks of it, you've got the right idea for grinding the shape of the dome...and some people struggle with that! IF it were me...I'd probably get the foam pads to back the sanding disks. I believe you can use a heat gun (or hair dryer on high) to heat up the surface of the pads to get the glue to release from the backing plate. IF you can get those to release, you can save those pads. You may have to get some spray adhesive to reapply them, but I think it's worth the effort as it's going to be SO much easier working with the foam backed sanding disks.
|
|
|
Post by rockjunquie on Feb 20, 2023 12:13:16 GMT -5
Great effort. That's how you learn, so don't get too disappointed. I definitely see 80 grit scratches. I can see that you are afraid to mess up your girdle. All understandable.
DO NOT EVER leave a wheel until ALL the scratches from the last wheel are gone. I go from 80 > 220 hard > 220 soft then the regular soft wheels. But, you are using a flat lap, right? It may be different. I don't remember. But, yeah- just stay on the wheel until the scratches are gone then move on. Wipe the cab, hold it at eye level near a good light. When the cab dries, you will see the scratches. Scratches from the previous wheel will look different.
|
|
|
Post by rockjunquie on Feb 20, 2023 12:14:00 GMT -5
jasoninsd I didn't see your post. I was writing- you were posting. 
|
|
realrockhound
Cave Dweller
Chucking leaverite at tweekers
Member since June 2020
Posts: 4,498
Member is Online
|
Post by realrockhound on Feb 20, 2023 12:26:07 GMT -5
Blue Biggs (you can see a lil in between the brown) and the second if I remember correctly is a type of graveyard. Take your time, and be patient with that Biggs, it’ll turn out very nice.
|
|
rocknewb101
fully equipped rock polisher
 
Member since October 2022
Posts: 1,368
|
Post by rocknewb101 on Feb 20, 2023 12:35:04 GMT -5
Hey Peta! Thanks for the tag!  Here's some tough love. You do NOT need a 280 hard disk or soft disk. How was that for tough? LOL It looks to me like those deep scratches are from the 80 grit disk. I know you're concerned about losing your shape if you go back to the hard disks...but you need to go back to the 180 and figure out how to use a "light" touch...so you're smoothing, rather than grinding. When it comes to the hard disks (or wheels) I believe there's two ways to use them: 1) Grinding - which is used to remove large quantities (relatively speaking) of material and uses a heavier amount of pressure against the disk/wheel...and 2) Smoothing - which uses a VERY light touch against the disk/wheel and is used to help with the final shaping and remove "flat" spots. Before I move off the initial wheel (80 grit) I run the cab over the surface lightly to make sure I've smoothed it as much as possible before moving onto the second hard wheel (disk). If I've done that correctly, then all I need to do with the 180 disk is "smooth" out the surface trying to get the scratches out from the 80. One of your issues you're going to have is that you don't have foam backing on the sanding disks...if I remember correctly. Which means you're going to have to use very little pressure on the 325 and above...otherwise you're going to create flat spots as you go through the stages. If you had the foam backing, pressure could be increased as the foam allows the disk to compress and create a circular indent which allows the surface of the disk to conform to shape of the dome of the cab. There is no amount of linear "time" which can be assigned to the work required on each stage. I can't say it'll take 5 minutes, or 40 minutes. Well...in fairness, if you're spending 40 minutes on one stage, you need to go back a step as that's a bit too long in my opinion. LOL - Some material it might take me 10 minutes on a stage. It all boils down to how well I shaped my dome on the 80...and how smooth I got it on the 180 (220 in my case). The first "soft" is where you'll likely be spending the most of your time. This may very well take 20+ minutes! A couple things I'll point out. I don't see a girdle line. I know some people swear by NOT using a girdle line...but in my opinion for someone just starting out, it's invaluable. It gives you a visual "DO NOT CROSS" line when shaping your dome. And two...you're either not using enough magnification when looking at the stone after each step, or there's not enough light. Those "deep" scratches should have been very visible through an Optivisor...and you would have known not to progress past the 180...or 325. I work my girdle last...after the cab has been domed and worked all the way through the 3000. When I cut out my preforms, I always work the edges of the preform before I put them on dop...and before I start doming. I make sure the shape is exactly what I want coming off the 80 or 180 hard disks. IF I've gotten all the scratches from the 80 off with the 180, when it comes time to work the girdle, I know I don't have to go back to the 180 and potentially mess up the girdle where it meets the dome. I can see on yours, there's deep scratches from the 80 on the girdle...which means you're going to alter the shape of the cab trying to get those scratches out with the 180. Please don't get discouraged. It's an absolute learning process. From the looks of it, you've got the right idea for grinding the shape of the dome...and some people struggle with that! IF it were me...I'd probably get the foam pads to back the sanding disks. I believe you can use a heat gun (or hair dryer on high) to heat up the surface of the pads to get the glue to release from the backing plate. IF you can get those to release, you can save those pads. You may have to get some spray adhesive to reapply them, but I think it's worth the effort as it's going to be SO much easier working with the foam backed sanding disks. Thank you!!! jasoninsd I love your kind of tough love lol! Point taken with regard to the 280 disc - I'd really rather not spend more money lol. You're correct, no foam backing - although they did send me a free backing plate and foam backer that I'm using on my final polishing step. I had wondered if I was using too much pressure - that's great advise and I will lighten my touch. Ahhh - the girdle line - that must be the marker line that goes around the girdle edge - I have seen that on others and wondered about it, then neglected to add it. I will do so on the next I try. I have been using both my magnifying light and optiviewer, but honestly I just wasn't sure where the scratches got removed so I did see them when moving forward to the next disc, but thought they'd get lesser and lesser. Now I know not to move from 180 until they are smoothed out - totally makes sense! Considering my last two "tries" I'm pretty pleased with the dome on this - had watched a video before starting where the guy showed how to accomplish this - was quite helpful. My birthday is coming up so I think I'll ask the hubs for $$ to get the foam backers, and maybe new discs if I mess them up removing them. Thanks so much for your wise input! It really has helped and I cant wait to go home and try again
|
|
rocknewb101
fully equipped rock polisher
 
Member since October 2022
Posts: 1,368
|
Post by rocknewb101 on Feb 20, 2023 12:38:18 GMT -5
Great effort. That's how you learn, so don't get too disappointed. I definitely see 80 grit scratches. I can see that you are afraid to mess up your girdle. All understandable.
DO NOT EVER leave a wheel until ALL the scratches from the last wheel are gone. I go from 80 > 220 hard > 220 soft then the regular soft wheels. But, you are using a flat lap, right? It may be different. I don't remember. But, yeah- just stay on the wheel until the scratches are gone then move on. Wipe the cab, hold it at eye level near a good light. When the cab dries, you will see the scratches. Scratches from the previous wheel will look different. Thank you rockjunquie! Also extremely helpful. Did I mention how much I love this forum? I am using a slant lap - have 80 > 180 (both diamond wheels) > then 325 smoothing >600 >1200 >3000 > 14000 polish > 40000 polish. Maybe overkill, but I'd bought the diamond paste so figured I'd use it  I appreciate your help!
|
|
rocknewb101
fully equipped rock polisher
 
Member since October 2022
Posts: 1,368
|
Post by rocknewb101 on Feb 20, 2023 12:40:11 GMT -5
Blue Biggs (you can see a lil in between the brown) and the second if I remember correctly is a type of graveyard. Take your time, and be patient with that Biggs, it’ll turn out very nice. Thanks realrockhound! I'm going to revisit it. May not be perfectly shaped when done, but am determined to use what I now know and fix it.  I bought a template and have about 10-12 nice pieces to play with!!
|
|
|
Post by jasoninsd on Feb 20, 2023 17:15:07 GMT -5
Hey Peta! Thanks for the tag!  Here's some tough love. You do NOT need a 280 hard disk or soft disk. How was that for tough? LOL It looks to me like those deep scratches are from the 80 grit disk. I know you're concerned about losing your shape if you go back to the hard disks...but you need to go back to the 180 and figure out how to use a "light" touch...so you're smoothing, rather than grinding. When it comes to the hard disks (or wheels) I believe there's two ways to use them: 1) Grinding - which is used to remove large quantities (relatively speaking) of material and uses a heavier amount of pressure against the disk/wheel...and 2) Smoothing - which uses a VERY light touch against the disk/wheel and is used to help with the final shaping and remove "flat" spots. Before I move off the initial wheel (80 grit) I run the cab over the surface lightly to make sure I've smoothed it as much as possible before moving onto the second hard wheel (disk). If I've done that correctly, then all I need to do with the 180 disk is "smooth" out the surface trying to get the scratches out from the 80. One of your issues you're going to have is that you don't have foam backing on the sanding disks...if I remember correctly. Which means you're going to have to use very little pressure on the 325 and above...otherwise you're going to create flat spots as you go through the stages. If you had the foam backing, pressure could be increased as the foam allows the disk to compress and create a circular indent which allows the surface of the disk to conform to shape of the dome of the cab. There is no amount of linear "time" which can be assigned to the work required on each stage. I can't say it'll take 5 minutes, or 40 minutes. Well...in fairness, if you're spending 40 minutes on one stage, you need to go back a step as that's a bit too long in my opinion. LOL - Some material it might take me 10 minutes on a stage. It all boils down to how well I shaped my dome on the 80...and how smooth I got it on the 180 (220 in my case). The first "soft" is where you'll likely be spending the most of your time. This may very well take 20+ minutes! A couple things I'll point out. I don't see a girdle line. I know some people swear by NOT using a girdle line...but in my opinion for someone just starting out, it's invaluable. It gives you a visual "DO NOT CROSS" line when shaping your dome. And two...you're either not using enough magnification when looking at the stone after each step, or there's not enough light. Those "deep" scratches should have been very visible through an Optivisor...and you would have known not to progress past the 180...or 325. I work my girdle last...after the cab has been domed and worked all the way through the 3000. When I cut out my preforms, I always work the edges of the preform before I put them on dop...and before I start doming. I make sure the shape is exactly what I want coming off the 80 or 180 hard disks. IF I've gotten all the scratches from the 80 off with the 180, when it comes time to work the girdle, I know I don't have to go back to the 180 and potentially mess up the girdle where it meets the dome. I can see on yours, there's deep scratches from the 80 on the girdle...which means you're going to alter the shape of the cab trying to get those scratches out with the 180. Please don't get discouraged. It's an absolute learning process. From the looks of it, you've got the right idea for grinding the shape of the dome...and some people struggle with that! IF it were me...I'd probably get the foam pads to back the sanding disks. I believe you can use a heat gun (or hair dryer on high) to heat up the surface of the pads to get the glue to release from the backing plate. IF you can get those to release, you can save those pads. You may have to get some spray adhesive to reapply them, but I think it's worth the effort as it's going to be SO much easier working with the foam backed sanding disks. Thank you!!! jasoninsd I love your kind of tough love lol! Point taken with regard to the 280 disc - I'd really rather not spend more money lol. You're correct, no foam backing - although they did send me a free backing plate and foam backer that I'm using on my final polishing step. I had wondered if I was using too much pressure - that's great advise and I will lighten my touch. Ahhh - the girdle line - that must be the marker line that goes around the girdle edge - I have seen that on others and wondered about it, then neglected to add it. I will do so on the next I try. I have been using both my magnifying light and optiviewer, but honestly I just wasn't sure where the scratches got removed so I did see them when moving forward to the next disc, but thought they'd get lesser and lesser. Now I know not to move from 180 until they are smoothed out - totally makes sense! Considering my last two "tries" I'm pretty pleased with the dome on this - had watched a video before starting where the guy showed how to accomplish this - was quite helpful. My birthday is coming up so I think I'll ask the hubs for $$ to get the foam backers, and maybe new discs if I mess them up removing them. Thanks so much for your wise input! It really has helped and I cant wait to go home and try again With regards to pressure...just think of a sculptor who is starting with a block of material. To remove large chunks of material, you need more pressure...but when you start getting toward the final shape of the piece, you don't want to remove as much material...so a lighter touch will smooth out the rough spots. There's a time and place for both of them. Seeing the scratches and flat spots (divots) takes some experience as well. Drying off the cab shows the scratches like what you left on yours. Having the cab slightly wet can show the divots because of the way a light will reflect distorted in those spots. I'll get the piece slightly wet, then move it around to see the reflection in my lightbulb and see how the reflection reacts. That tells me if I am slightly off on the dome (or majorly off! LOL). I make sure to dry the piece off after every step to inspect for scratches. And like rockjunquie said, there WILL be scratches visible as you're going through the process...but as time goes on, you'll be able to tell what scratches were left from the wheel you were just working on. One way to check is to allow the disk to run over the cab in the same direction rather than using a circular movement. Check the surface of the cab. If the "scratches" are in the same direction the disk was traveling in, then you know it was THAT wheel that left the scratches and not the previous wheel (disk). Truthfully, sometimes I don't check the surface for scratches after certain wheels. I can tell/see how much material is being removed and know enough of the surface was removed that there was no way there was scratches from the previous wheel. That really does come with time and experience. You really do have every reason to be pleased with where you're at. It's difficult to figure all this out without a "hands-on" teacher right there (trust me, I know! LOL). I absolutely believe you will get this down. It's just a ton of little things you're trying to figure out or remember right off the bat! 
|
|
|
Post by pghram on Feb 20, 2023 17:32:39 GMT -5
rocknewb101,
I use a flat lap (Ameritool) and I do things a little differently. I rarely use the 80 grit hard lap for doming any longer. It took me forever to remove the 80 grit scratches. I constantly had to go back to earlier laps to remove them and repeat the progression (which is a PITA on a flat lap). So now, I do my doming w/ the 180 grit hard lap. It takes longer to get the dome, but it actually saves me time later not have to remove 80 grit scratches. I then move to either a 220 soft lap or 325 hard lap. If I still have scratches in the center, I use the 325 hard lap. Either way I then use soft laps 220, 325, 00, 1200, 3000. I then go to diamond paste on leather 14K & 50K if needed).
Peace, Rich
|
|
|
Post by hummingbirdstones on Feb 20, 2023 22:02:00 GMT -5
rocknewb101, take your time you'll get it. One thing I didn't see mentioned is that you need to break in the metal diamond laps a little (just like you would on wheels of a cabbing machiine) to knock down some of the diamonds that stick up higher than the others. A real hard agate (brazilian, etc.) just run over the whole surface of the lap for a while (5-10 minutes) will take down those higher diamonds and make the lap surface more uniform. I have a feeling that a lot of your deeper scratches are from the higher diamonds and pressing too hard. Jason spelled it out really well, but any time your working on diamond laps, your motto should be "let the diamonds due the work". Put just enough pressure on your stone so it's not jittering on the lap, especially when you're breaking in new ones. The smoothing discs aren't as aggressive as the metal discs since the diamond is embedded in a resin, so you don't have to be so delicate on those, but you still want to let the diamond do the work and not bare down on them too much. Besides, you'll tire your fingers and hands out if you do that. One other thing I wanted to mention is that I noticed on the back edges of that Biggs that they're chipped up pretty good. When you take it off that dop, make sure you run those edges lightly on the 180 grit to bevel it a bit. If you leave them like that, they can chip off more and make you unhappy. I actually always run the edges of the back of cab and bevel it before I dop it, just to be safe. Just remember that the more you practice, the better you'll get and the more muscle memory you'll develop. It wil get easier, I promise!
|
|
|
Post by jasoninsd on Feb 21, 2023 8:10:04 GMT -5
hummingbirdstones - Robin, that's some great advice! I know we've talked about my "heavy handed" pressure on the wheels...but I want to get it done and I've got crap to do...so it still hasn't eased up! LOL - Also thanks for mentioning about breaking in the disks! 
|
|
rocknewb101
fully equipped rock polisher
 
Member since October 2022
Posts: 1,368
|
Post by rocknewb101 on Feb 21, 2023 8:20:18 GMT -5
jasoninsd pghram hummingbirdstones - thank you all so very much! Each piece of advise is extremely helpful!! I went back down last night and started to work on the Biggs, but got a little nervous and really want to practice on another (lesser) piece first because i really like the Biggs and don't want to mess it up further - should have set that one aside in the beginning, but got ambitious  One other thing I was thinking about last night as I was rounding out my shapes, getting them ready for practice was speed - my machine has like 6 speeds. I'm pretty sure when I'm trying to take off a lot of material I want the higher speeds, but wondered - when I'm trying to smooth out and get rid of scratches, should I be on a lower speed? Seems less aggressive the slower the wheel turns and would make sense - tried it a bit on the girdle edge (before I put my girdle line) to see about scratches there and seemed to work? Thanks again - you all rock! (pun intended)
|
|
|
Post by jasoninsd on Feb 21, 2023 8:26:17 GMT -5
I'll see what others say...but I had mine on full blast when I was on the slant cabber. I have since learned that for the polish, fastest isn't always bestest! LOL (Since diamond paste is run without water to cool it down, too fast can superheat the rocks causing fractures!)
|
|
|
Post by rockjunquie on Feb 21, 2023 8:49:37 GMT -5
too fast can superheat the rocks causing fractures!) Don't I friggin' know it!!
|
|
rocknewb101
fully equipped rock polisher
 
Member since October 2022
Posts: 1,368
|
Post by rocknewb101 on Feb 21, 2023 8:50:41 GMT -5
I'll see what others say...but I had mine on full blast when I was on the slant cabber. I have since learned that for the polish, fastest isn't always bestest! LOL (Since diamond paste is run without water to cool it down, too fast can superheat the rocks causing fractures!) Good to know! Thank you!!
|
|