|
Post by jakesrocks on Jan 9, 2013 12:26:59 GMT -5
Scott, the single head machine I'm planning to build is capable of cutting anything from marble to bowling ball sized spheres. It just depends on which size cup you use.
|
|
Deleted
Deleted Member
Member since January 1970
Posts: 0
|
Post by Deleted on Jan 16, 2013 20:23:39 GMT -5
yeah, thinking about it, I can visualize it.
Thanks Don!
|
|
Kenneth
off to a rocking start
Member since July 2013
Posts: 2
|
Post by Kenneth on Jul 13, 2013 1:17:42 GMT -5
So I've been silently following all your progress as an unregistered member, but I just have too many questions to remain silent any longer. Most of these questions may seem very basic, as I haven't even started building one of these yet.
1.) The grit cups. Seems like there is a lot of variation of styles here. Assuming I try the plumbing bell reducer method, with the chain lifting grit occasionally, my main question is - what goes inside the bell reducer? Nothing? Just the grit? I am a bit confused on this.
2.) As for cutting the preforms, what do you guys suggest? I was thinking about a vise and my skill saw with a masonry blade, or perhaps a cheap tile saw to make the cube.
3.) Anyone know of a good place to get grit at different sizes?
4.) I have three 120V 1.3A 72 RPM motors, do you think these will be sufficient for a decent machine?
|
|
|
Post by Rockoonz on Jul 13, 2013 9:34:50 GMT -5
Grit cups- If you will be using grit and not diamond cups the most logical way I've seen it done is a local guy who puts short lengths of black pipe nipples cut in half on his bell fittings so as they wear down he can replace them for less cost.
Preforms- If we're talking less than maybe inch and a half spheres a tile saw by itself may be OK. Larger and you'll need a slab saw for the cubes.
Grit- Don't know where you live exactly, but the club we're members of in Portland buys grit from a local industrial supply house by the 500 or 600 lb barrel for coarse, and pallets of bags for finer grits. If you tumble as well and you're in it for the long haul you should bing search abrasives in your area. Other RTH members will probably have ideas for smaller quantities online.
Gearmotors-72 RPM is a bit slow, but will probably work if you're patient. The grit just rolls between the bell reducers and the stone to work it down to a sphere.
|
|
Kenneth
off to a rocking start
Member since July 2013
Posts: 2
|
Post by Kenneth on Jul 13, 2013 11:43:47 GMT -5
Thanks, rockoonz. It's good to get this cleared up.
I have a bunch of hole saws and core bits left over from masonry work, most of them look about like this (http://www.toolskitchen.com/1-1-2-dry-diamond-core-drill-bits-for-granite-eng.-stone-hole-saws.html?gclid=CK-o5a30rLgCFcFj7AodTkkAQw). What are your thoughts on using those as cups?
I was also thinking about attempting to make a preform with the hole saw, essentially cutting out a cylinder and then cutting another cylinder sideways out of that one - I think I'd end up with a roughly spherical object.
I'll try the hole saw method and see how it goes for the preforms.
|
|
|
Post by Rockoonz on Jul 14, 2013 0:10:17 GMT -5
I have seen demos of making preforms with hole saws. If you have the drill setup it's a good way to do it. If you use core drills for cups it will work, there's one on page 11 of this thread. Plated drills will have a short life if they work at all, sintered drills last a long time.
|
|
|
Post by jakesrocks on Jul 14, 2013 0:27:10 GMT -5
WOO HOO. Found belts for my little machine. Gonna get it cleaned up and rewire it. I'll be cutting little spheres soon.
|
|
Deleted
Deleted Member
Member since January 1970
Posts: 0
|
Post by Deleted on Jul 14, 2013 14:59:57 GMT -5
Kenneth The hole saws I use are the segmented type. One type claims that each hole saw can drill over 200ea 3" deep holes. My machine uses three! I suspect that for 4-5" spheres I'll be rough grinding into eternity! I also have large sintered diamond segments I will soon weld onto larger cups..
|
|
makkybrown
off to a rocking start
Member since October 2013
Posts: 1
|
Post by makkybrown on Oct 23, 2013 4:31:23 GMT -5
Hello all, Just joined the forum after reading this thread. I'm about to build a sphere maker myself. Probably three heads but I am wondering if all three heads need to be powered. Could one be fixed and the other two turn in opposite direction?, thoughts appreciated. Cheers Andrew
|
|
|
Post by jakesrocks on Oct 23, 2013 8:11:12 GMT -5
As long as the third head can rotate, I don't see any reason why you couldn't get away with 2 powered heads. You'll just have to keep an eye on the unpowered head to make sure it is rotating. All 3 heads will need to be adjustable and spring assisted though.
|
|
|
Post by Rockoonz on Oct 23, 2013 23:35:57 GMT -5
I think a fixed or freewheeling head would tend to keep the random movement you need from happening.
Lee
|
|
|
Post by 1dave on Nov 5, 2013 13:30:42 GMT -5
I have seen demos of making preforms with hole saws. If you have the drill setup it's a good way to do it. If you use core drills for cups it will work, there's one on page 11 of this thread. Plated drills will have a short life if they work at all, sintered drills last a long time. I think the drill press photo was on page 10, but has been removed from Photobucket.
|
|
|
Post by Rockoonz on Nov 5, 2013 21:46:50 GMT -5
I have seen demos of making preforms with hole saws. If you have the drill setup it's a good way to do it. If you use core drills for cups it will work, there's one on page 11 of this thread. Plated drills will have a short life if they work at all, sintered drills last a long time. I think the drill press photo was on page 10, but has been removed from Photobucket. I was referring to the photo near the top of page 11 that shows sintered core drills being used on a sphere machine. Lee
|
|
|
Post by 1dave on Nov 6, 2013 7:13:07 GMT -5
Ah so! Thanks Lee!!! Yes, that is helpful.
|
|
alan
starting to spend too much on rocks

Member since December 2013
Posts: 111
|
Post by alan on Dec 17, 2013 14:05:16 GMT -5
Can someone provide an alternative source for the 105.7 RPM motors?
|
|
Deleted
Deleted Member
Member since January 1970
Posts: 0
|
Post by Deleted on Dec 17, 2013 14:31:19 GMT -5
Can someone provide an alternative source for the 105.7 RPM motors? In a word, no. The new Highland Park buys them all from surplus center. I have even considered going to china to a small container load. keep in mind the precision of 105.7RPM is not required. a 100RPM motor will work just a bit slower. 120RPM works too, as does 170 (but I consider that too fast for rough grind) If you find a source, please post it here.
|
|
TomS
off to a rocking start
Member since October 2013
Posts: 13
|
Post by TomS on Dec 18, 2013 10:48:47 GMT -5
So, I finally got around to building my sphere machine. I also purchased the same plans. I was not able to get the same motors as you guys did, but found some gear motors at American Science and Surplus. They are 130RPM intermittent duty motors. So I needed to provide some kind of cooling to keep them running. I tested several methods and they all seem to fail in thermal shutdown, even when I was blowing so much air over them that they weren't even getting hot anymore. I finally figured out where the thermal switch was on the motors. That switch was just beneath the white tape covering the coil. I carefully removed the tape and raised the switch to above the coil. This way the switch stay cooler and if the motors really get hot, the will go through thermal shutdown. So, for the frame I made it out of spare acrylic pieces I had laying around. I have a laser cutter, so using the acrylic was the choice for me. The base is made from 3/8" acrylic, the motor frames were made from 7/16" acrylic, and the fan frame is made from 1/4" acrylic. I still have some wiring work to clean up, but anxious to get it up and running. The shaft on these motors is 5/16". I initially made an adapter from a coupler nut and made some wooden cups from 5/8" dowel. I quickly found out that the coupler nuts were not consistently drilled out state and made a very unusable swing in the rotation of the end of the shaft. I ended up drilling out 1" oak dowel , as centered as I could get. put velcro on the end and cut out the center of some different grits of diamond grinding pads. That seems to work great. I'm making some smaller ones for the marbles I'm making as well as I'll get an adapter to use a 3" polishing pad adapter for larger spheres. 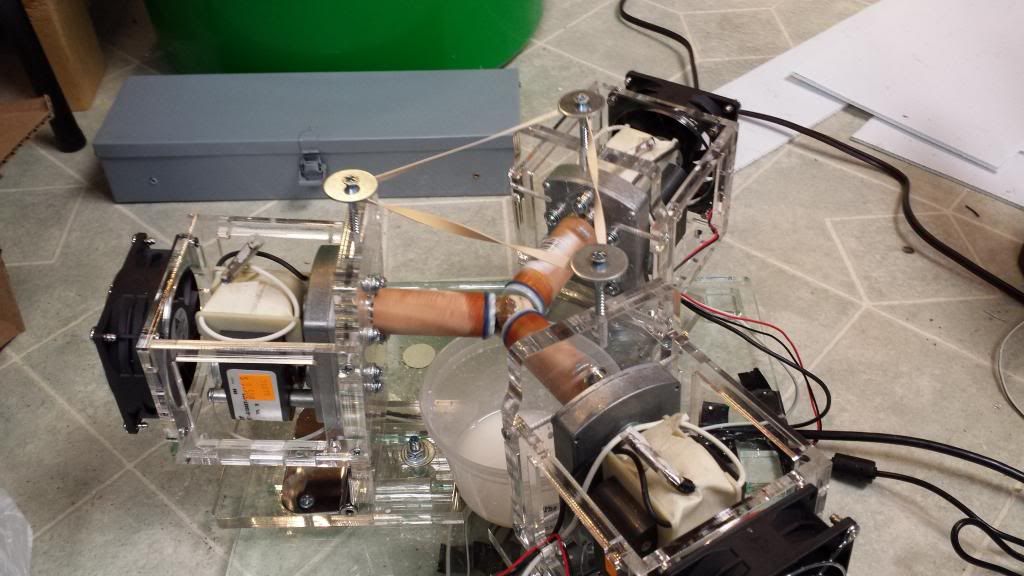 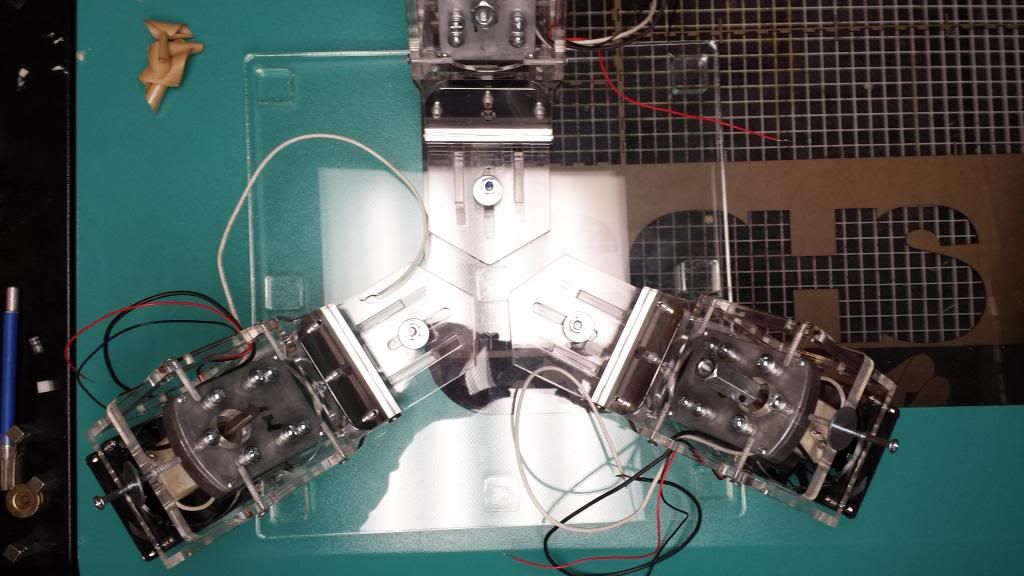 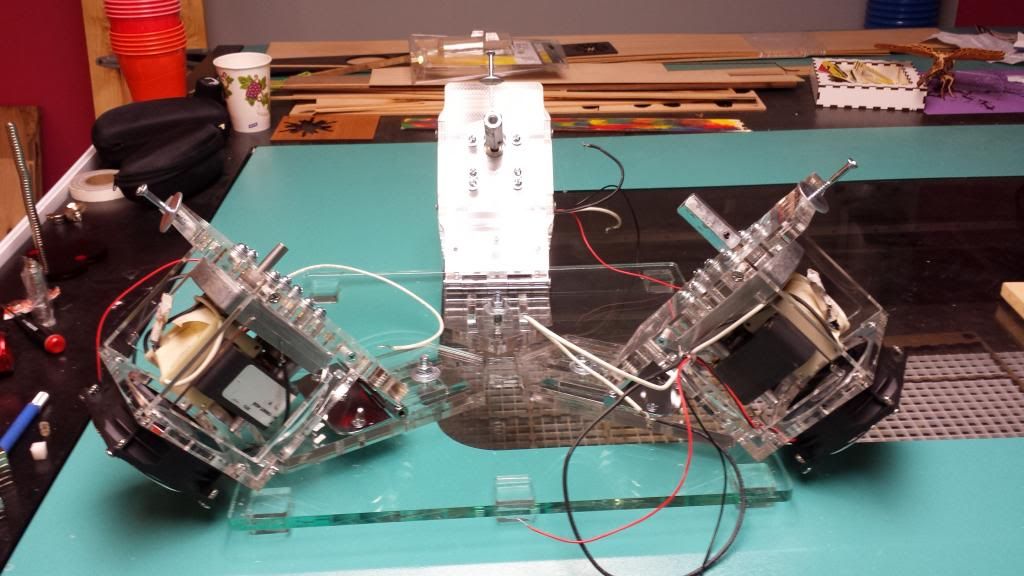 I also designed and made a marble mill using his plans as a starting point. 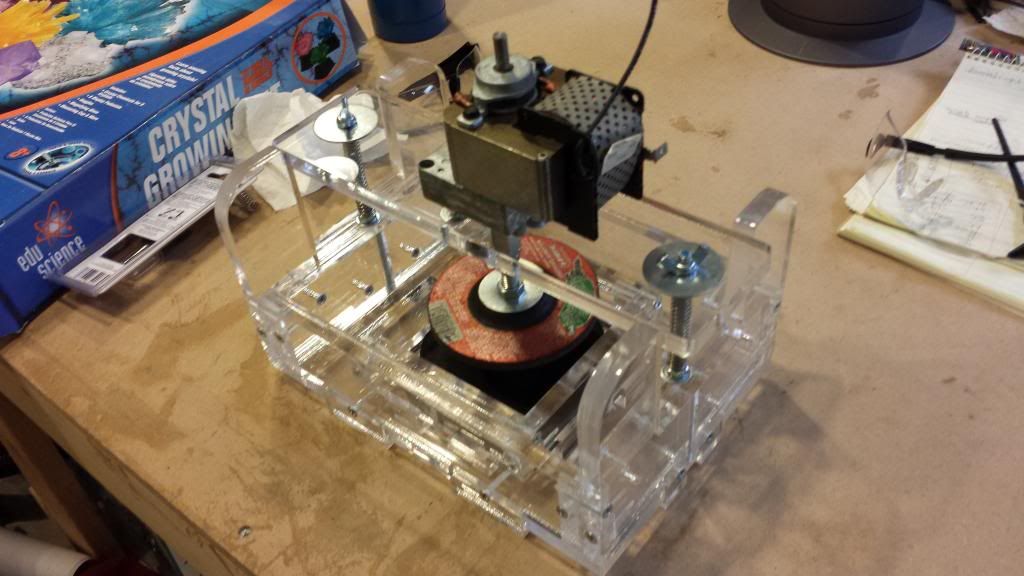
|
|
GeorgeStoneStore
starting to spend too much on rocks

Member since November 2011
Posts: 168
|
Post by GeorgeStoneStore on Dec 18, 2013 12:03:59 GMT -5
professional work! like it!
|
|
quartz
Cave Dweller
breakin' rocks in the hot sun
Member since February 2010
Posts: 3,359
|
Post by quartz on Dec 18, 2013 12:14:57 GMT -5
Very nicely done machines. All that "spare" acrylic you have used makes these look like something out of M.I.T., not only a class construction act, but the visual too. We like the wood puzzle dragonfly in ctr. pic. Enjoy watching dragonflies on the place, have one like yours flying in the shop too. Larry
|
|
juzwuz
has rocks in the head
 
Member since April 2010
Posts: 526
|
Post by juzwuz on Dec 18, 2013 15:17:07 GMT -5
Nice looking machines! Be sure to post pictures of the marbles and spheres you make. I just found a gear motor in my pile of parts which should work nicely for a bead/marble mill. I'm not sure when I'll get to it though. How much laser wattage do you have and cutting dimensions?
|
|