|
Post by jakesrocks on Nov 24, 2011 12:15:15 GMT -5
A couple months ago in one of the discussions about sphere machines, someone posted a link to a video with a running sphere machine. They had a very simple and interesting grit feed method. It was nothing more than an endless loop of small chain. Under the machine was a small container of grit and water. The chain looped around the sphere and hung in the grit bath container. The chain was pulled along by the turning sphere, and carried a grit rich slurry to the sphere. As I remember, there was a very slow water drip above the sphere. Once my machine is up and running, I'll give this a try.
Don
|
|
Steve
has rocks in the head
 
Member since June 2005
Posts: 506
|
Post by Steve on Nov 24, 2011 12:57:18 GMT -5
I use a slow spinning plastic bottle of grit (uses a small motor) that dumps a measured amount of grit twice each turn. Works fine for 60/90 and 220. Anything finer has to be appled by hand. I mix the finer grits in water in a catsup squeeze bottle and squirt it on.
|
|
|
Post by jakesrocks on Nov 24, 2011 13:05:46 GMT -5
For the springs that go between the motor mounts, most auto parts stores have a good selection of throttle return springs in various lengths and amount of tension. Also, the good old fashioned screen door springs would work. One door spring would probably supply enough length to be cut into the needed 3 springs. Still another possibility would be heavy duty spring loaded hinges between the base plate and motor mount plate. This would do away with the need for springs at the top of the machine. Most of these hinges have adjustable tension. I've been looking for a source for surplus hinges of this type. If I find them, I'll post a link.
|
|
|
Post by Dicky the Rockhunter on Nov 24, 2011 14:02:59 GMT -5
I have this sphere machine and wondered if looking would be any help. Also it is for sale , the owner wants $750 ( I think it is high ) to purchase it plus shipping    Really enjoy watching your progress. Dicky
|
|
Steve
has rocks in the head
 
Member since June 2005
Posts: 506
|
Post by Steve on Nov 24, 2011 17:24:48 GMT -5
If I can make a suggestion about your design: I think you need to figure out a way to protect and to drain your rails. Once they fill with rock snot, which will set up like concrete, your machine will no longer be adjustable. It may be enough to drill lots of holes. I don't think that any scheme you come up with to protect the rail will work, you will need to be able to drain and clean them. Rock snot and grit will manage to get into everything. Once a year I remove the motors from my machine and power wash it. Seems to be the only way to get rid of all the dried slurry with the imbedded unused grit. After the power wash is when I do my polish runs. I'm in the process of setting up a second machine to use just for prepolish with diamond and polish with either diamiond or polish (Tin Oxide or Cerium) on leather, depending on the type of stone. The design of my machine is similar to the ones posted by Dickey and Jason - just a different spring arrangement and grit feder. I use springs to push the plates from behind.
I put my capaciters in waterproof electrical boxes, which I mounted to the bottom of the machine. I put legs on the machine to lift it up enough for the boxes. The second machine, which I bought used (currently rebuilding) put the capacacters inside of PVC pipes mounted under the machine. These PVC pipes are the feet for the machine.
|
|
|
Post by jakesrocks on Nov 24, 2011 17:43:46 GMT -5
Steve, they make snap in protectors For the slots in those aluminum rails. I plan to cap the ends of them. Also have a waterproof box which will contain the capacitors and power switch. Water tight feed thru fittings will be used for both the wiring to the motors, and the power cord.
|
|
Steve
has rocks in the head
 
Member since June 2005
Posts: 506
|
Post by Steve on Nov 24, 2011 21:15:28 GMT -5
Nice.
|
|
juzwuz
has rocks in the head
 
Member since April 2010
Posts: 526
|
Post by juzwuz on Nov 25, 2011 1:08:19 GMT -5
Definitely like all the activity. I hope to see pictures of everybody's sphere machines soon. I usually start a lot of projects but only finish a few but thanks to y'all I think I'm getting real close. I find it helps to post progress reports especially when people are interested in them. Thanks! I did some quick soldering and wiring of three wire bundles and plugged everything in. Click on the picture to bring up the video. The machine is alive!  I need to get a waterproof project box of some sort and clean up the wiring to make it safe. I also like the chain and spring idea so I'll have to rummage around the junk pile and see what I have. I'm not planning on using any grit/slurry mixture...just diamond core drills and diamond polishing pads. Hopefully there won't be as much of a mess but I'm not too worried about the aluminum extrusion getting clogged up. The slots are fairly deep and if it gets to the point of blocking the t-nuts, I could tear down the machine for cleaning or just turn the extrusion over and use the other side. Justin
|
|
juzwuz
has rocks in the head
 
Member since April 2010
Posts: 526
|
Post by juzwuz on Nov 25, 2011 1:22:33 GMT -5
I need another project like i need another hole in the head but everytime you post an update here i end up going through the whole thread and i think i have convinced myself to build one of these. I am also a bit of a pack rat and scrounger so i think i already have most everything to build one of these except the gear motors. Time to start digging through my piles of stuff and putting together a parts list. Thanks for your continued updates here, i am inspired. Sampson Order those gear motors from surplus center and start building! I've been inspired by your cool pictures of the B.C. countryside (and your hunt for gold). My wife has family in Victoria and Vancouver but the only scenery we usually see is on the ferry trip to and from the island.
|
|
juzwuz
has rocks in the head
 
Member since April 2010
Posts: 526
|
Post by juzwuz on Nov 25, 2011 1:25:22 GMT -5
Hey Guys - I have to apologize, I told you I'd get pictures of my machine, however I spaced! - Tonight I was going through some CD's of photo's and came across these 3 of my machine. I'll try and get better detailed pics of the machine for you as well.    Jason, Thanks for the pictures! I'm going to scrounge around for some springs and chains. I also like the little adjustable stop/wingnut at the base of the motor plate. Justin
|
|
|
Post by jakesrocks on Nov 25, 2011 10:59:17 GMT -5
Justin, just for safety sake why don't you get some heat shrink tubing and cover the area of your wires from the plug down past the heavy insulation on your wires ?
I have a large box of wires in various colors in my shed, so I'll stick with color coding all the way through. Everything will be covered with heat shrink, from the motors to the power box. I'm using 16 gauge stranded wires, which will be much more flexible.
My rails and hardware are supposed to arrive today, and the motors early next week.
|
|
sampson
starting to spend too much on rocks

Member since April 2011
Posts: 222
|
Post by sampson on Nov 25, 2011 11:36:11 GMT -5
Order those gear motors from surplus center and start building! I've been inspired by your cool pictures of the B.C. countryside (and your hunt for gold). My wife has family in Victoria and Vancouver but the only scenery we usually see is on the ferry trip to and from the island. Glad you liked my pics Justin. I was unsure about them shipping to Canada and the associated fees so i did some looking around for suppliers north of the border and all i can find for comparable motors are priced in the $300 to $600 range, too damned expensive. I decided to send a mail to the surplus center to see what the shipping and duties will be but they will be closed all weekend for Thanksgiving so i don't expect a reply 'till monday. Hopefully they aren't too expensive to ship up here but as long as it isn't outrageous i am pretty sure i will be placing my order on Monday once they reply. I tend to accumulate some great rocks that are too large for my tumblers and even if i break them down i end up having waaay too much material so this project will be a great use for some of the stuff i find. I'll be sure to post here when i get building. Sampson
|
|
|
Post by jakesrocks on Nov 25, 2011 12:16:23 GMT -5
Hey Justin, what is the number on your male Molex connectors ? We don't have an electronics supply place within 100 miles of here, but I've found them online. There are 2 or 3 different sizes of 4 pin connectors.
Don
|
|
juzwuz
has rocks in the head
 
Member since April 2010
Posts: 526
|
Post by juzwuz on Nov 25, 2011 18:20:31 GMT -5
|
|
|
Post by jakesrocks on Nov 25, 2011 19:21:52 GMT -5
Thanks Justin, but I ordered 3 sets of male and female connectors a couple hours ago. I'll just cut the old connectors off the motors and start with new stuff. Don
|
|
juzwuz
has rocks in the head
 
Member since April 2010
Posts: 526
|
Post by juzwuz on Nov 25, 2011 20:29:01 GMT -5
Are there any good tutorials on cutting a sphere preform? I think some people cut a cube, then the corners off, then all the edges (26 cuts?). Other people use a diamond core drill with 5 or 6 cuts? How round should the preform be before it can be put into the machine?
|
|
|
Post by jakesrocks on Nov 25, 2011 20:48:32 GMT -5
26 cuts, then grind the preform as round as you can on a grinding wheel is the old standard.
|
|
rockhound97058
freely admits to licking rocks
 
Thundereggs - Oregons Official State Rock!
Member since January 2006
Posts: 760
|
Post by rockhound97058 on Nov 26, 2011 0:46:59 GMT -5
Justin - some time ago I started building a page on my website for the steps for cutting blanks - However I ran out of steam and had other issues to deal with so the page got shoved to the backburner - You can take a look at it just to see the pictures I have loaded at www.oregonthundereggs.com/spheremaking.html - The only photo I do not have loaded is the cube in the "jig" for cutting corners. As Don said though - cut a as perfect as you can 6 sided "cube". Using the jig set it up and cut the 4 corners creating a 8 sided octogon. Then rotate this 90 degree's and cut the 8 corners. Then rotate 180 degree's and cut the remaining 8 corners until you have stone with 26 cuts. You can place this directly into the sphere machine and run a slightly oversized cup and grind the corners - however this takes a long time and really beats the machine. So we use a 4" grinder with a dry cutting "turbo cup" to hand grind the corners. Once you start grinding the sphere in the machine - you want the sphere to move in many directions. One thing you do NOT want is the sphere to spin in one direction. In soft stones the cups with actually cut a groove into the stone. It takes time to get used to the machine, 60/90 is pretty forgiving - I can actually walk away from my machine for a hour or so and leave it going... 220 gets a bit more attention and 600 and polish is hands on for the duration of the grind lol.
|
|
rockhound97058
freely admits to licking rocks
 
Thundereggs - Oregons Official State Rock!
Member since January 2006
Posts: 760
|
Post by rockhound97058 on Nov 26, 2011 19:24:54 GMT -5
Here's more pictures of my sphere machine. Maybe it'll give you guys some idea's on your designs.  This is my water drip tank. Piece of pvc with a cap - needle valve screwed into the pvc cap - with soft copper line down a few inches and then used clear plastic line down to the sphere 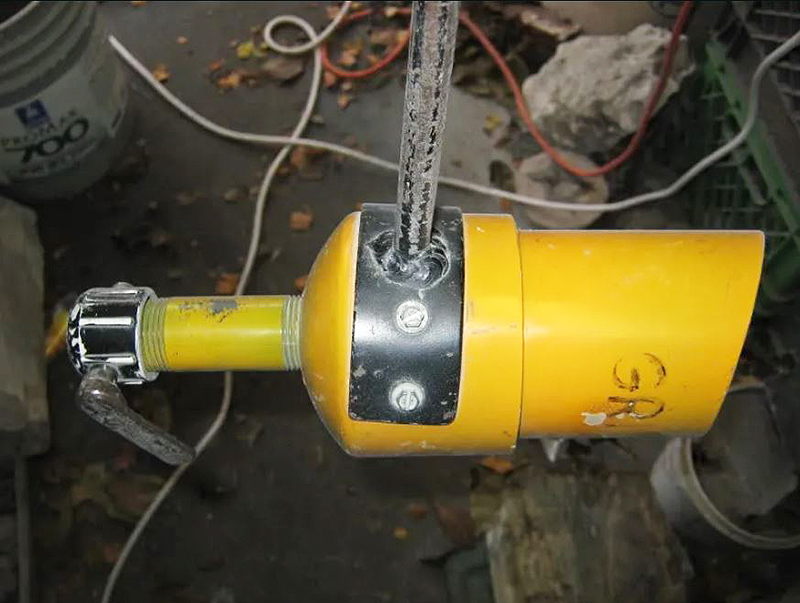 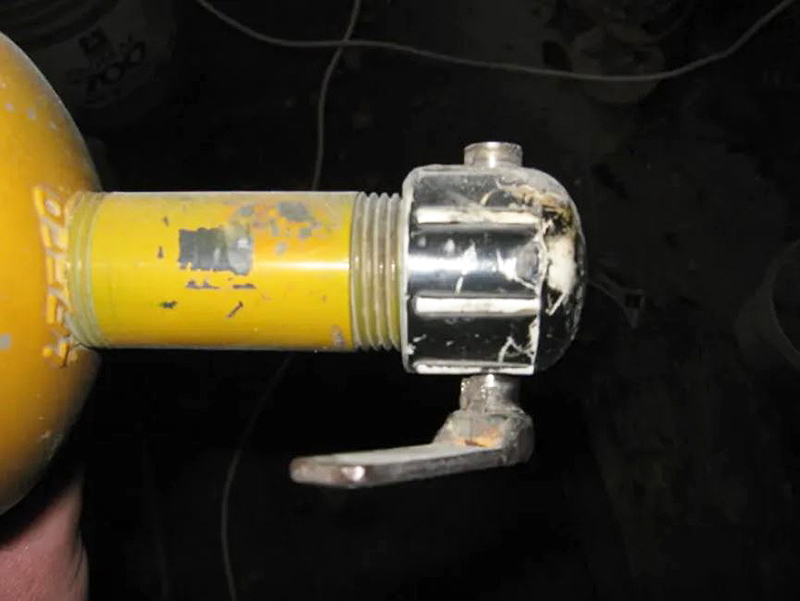 Grit feeder - This is gravity feed. pvc pipe with another cap. The cap has a nipple extension with a small cap. The small cap is drilled with a small aluminum tube with a welded handle. 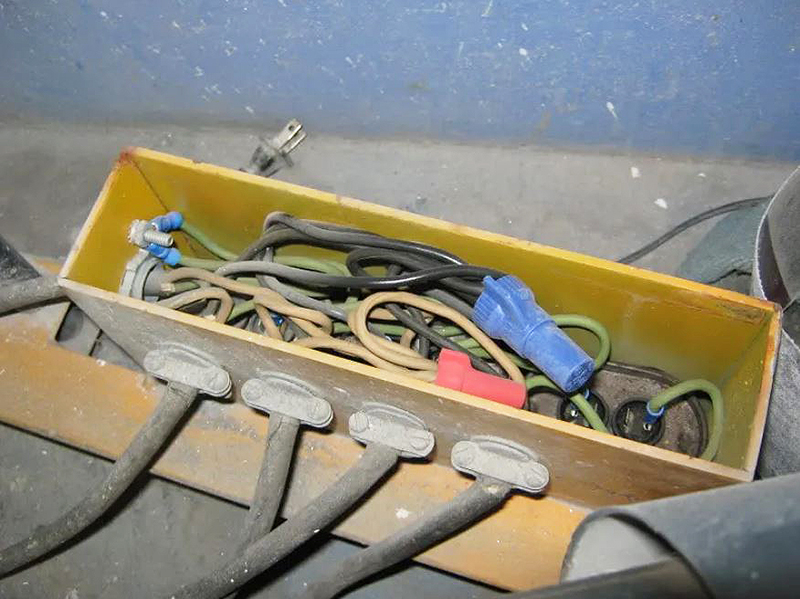 Steel box - welded to the machine frame - which houses the capacitors. My machine also has a 110v dual plug in wired on the side to allow an optional light to be mounted on the machine 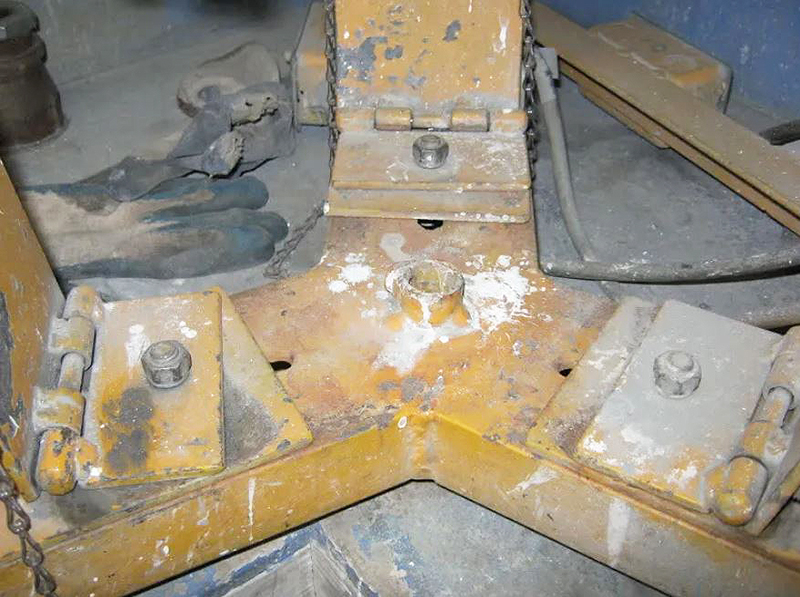 This shows the center of the machine - All 3 legs are at equal angles and has a pipe welded into the center to allow a plate to be attached for grit collection. 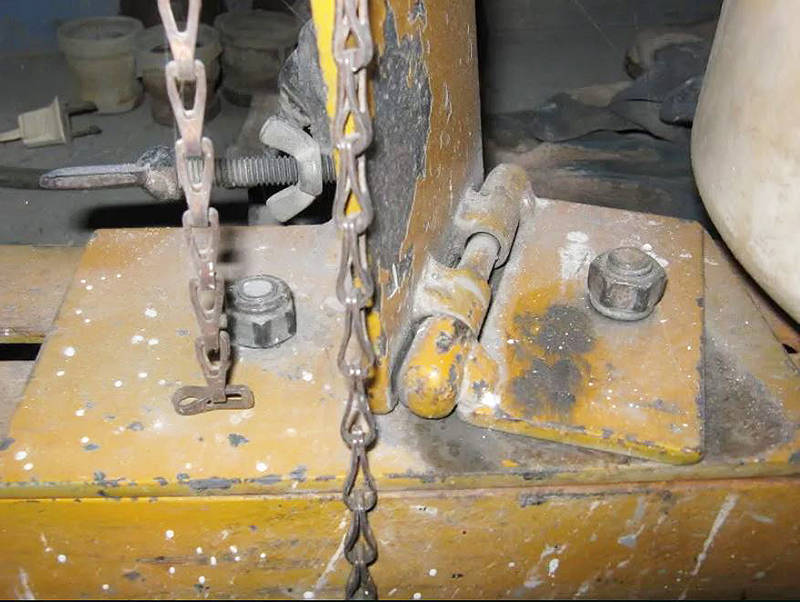 This shows my uprights that the motors are attached too. The nut on the left loosens and slides the entire motor back and forth to adjust for different sphere sizes. The nut on the right can be loosened and allows the uprights to pivot. 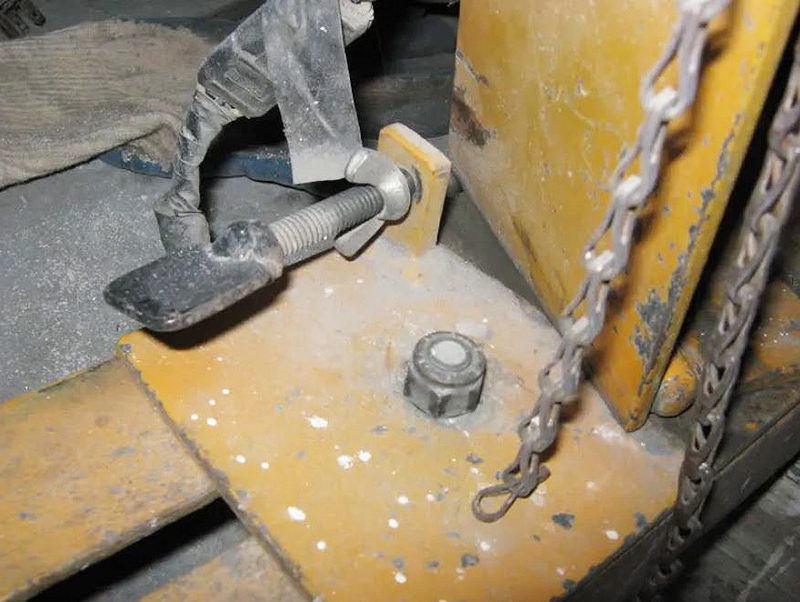 This show the welded tab with thumb-screw. This allows pressure to be placed at the bottom of the uprights. The next machine I build will have two of these. One on each side (this is the way Richardson's machines are). Any rate - thought this might help! Jason
|
|
sampson
starting to spend too much on rocks

Member since April 2011
Posts: 222
|
Post by sampson on Nov 28, 2011 17:49:06 GMT -5
I got a reply from the surplus Center today about shipping costs and just placed my order. Shipping for the three motors cost more than the cost of one of them but it is by far still the cheapest place i can find to get motors with these specs shipped to me. I'm not sure if there will be duty fees at the border but i'm pretty sure they will want to collect some provincial sales tax from me when they get here. The shipping quote said 7 to 10 days until arrival so hopefully there aren't any holdups at the border. I'll be sure to post my build as i go.
I also collected some nice material this weekend that i think will look good as spheres so now i can't wait to get this project built.
Sampson
|
|