jamesp
Cave Dweller
Member since October 2012
Posts: 36,612
|
Post by jamesp on Jun 24, 2018 8:29:59 GMT -5
Wife did the compositions, I did the whiskey and yellow/red from Polish vases. I did the shaping in the almost dark this morning. Got a bunch of cool pendants out of this heavy Polish $5. Very strange vase, blower was doing some technique not familiar  From a while back out of coarse tumble  Wife's compositions and my vase work a couple days ago. Mine are better. 
|
|
|
Post by fernwood on Jun 24, 2018 8:47:00 GMT -5
Cool vase.
|
|
jamesp
Cave Dweller
Member since October 2012
Posts: 36,612
|
Post by jamesp on Jun 24, 2018 9:09:00 GMT -5
My favorite glass is certain vases, certain brands and an occasional beauty like that one. One glass blower uses virgin glass, the other recycle. The scraps from the virgin are way easier to work with.
|
|
jamesp
Cave Dweller
Member since October 2012
Posts: 36,612
|
Post by jamesp on Jun 24, 2018 9:16:21 GMT -5
World's most fancy tumbling media. Fine for glass and soft stones, sorta ineffective on agate. Been contacting wholesale bead houses looking for discontinued bead stock. No shortage of kiln and tumbling fodder out there. This company had 614 pounds of these furnace millefiori's. I bought 100 pounds. Cheap 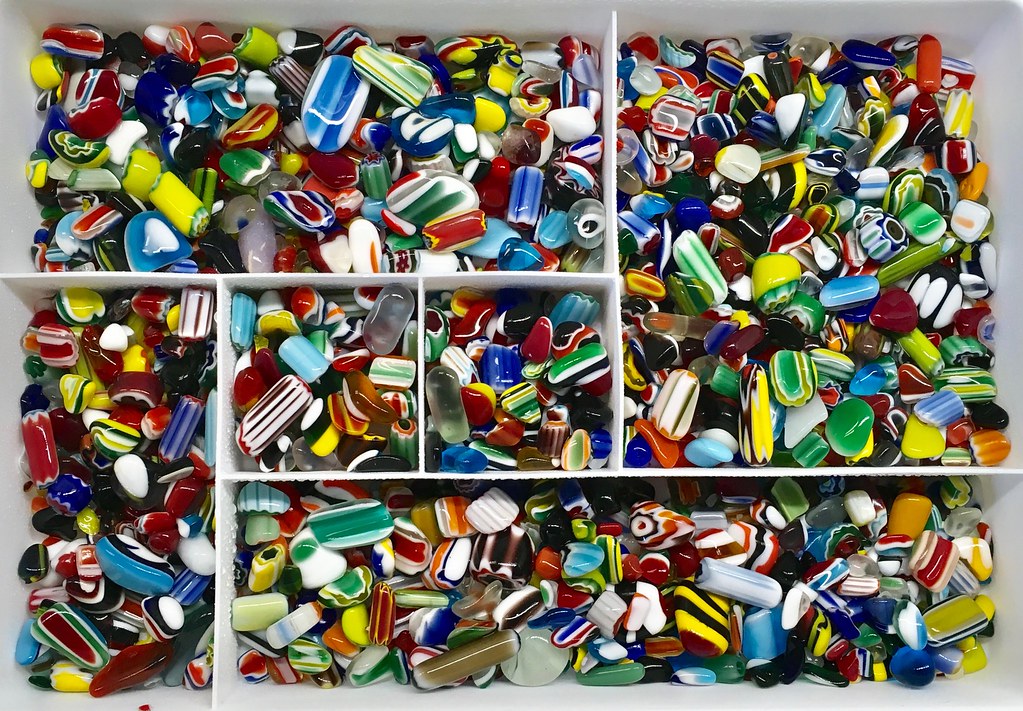
|
|
|
Post by hummingbirdstones on Jun 24, 2018 9:34:00 GMT -5
Bummer about the blasted bubbles. Keep experimenting with solutions until you find one. That knapping crowd is too good a prospect to just let it go without at least trying to find a way to eliminate the bubbles.
|
|
|
Post by rockpickerforever on Jun 24, 2018 10:10:08 GMT -5
problems: hard glass that has already seen 2200F which decreases flow, increases viscosity shards stacked are air catcher/trappers solutions: yep, longer hold at highest temp(done, using 30 minutes), but an hour would be a good move. Higher temp, since this is recycle and has seen 2200F, increase from 1500F to 1575 maybe 1600. You may boil it at those temps = many more bubbles smaller pieces thinner slab OK Jean, I could open the kiln at max temp and stir the glass. Yes changes pattern but can assist bubbles coming to top. I have opened it at 1200F baking eye moisture and scorching hand/arm in seconds, best wear protection. 1500F certainly wear protection Possibly re-melt, that particular color rich slab would probably have serious color mix at re-melt and turn into big brown patty turd. Some knappers use 'abo' techniques. (Aboriginal) and don't use a jig, like Native man used. They would be OK with the bubbles. So, sounds like the biggest problem is in choosing the glass. Bits that have seen higher temps are "harder," if you will, and won't let air bubbles escape. Some people's solution was to open the kiln while hot and stir. They emphasized wearing protection to prevent bodily harm. (Careful! Burns are painful, but will heal over time. You don't get a new set of eyeballs.) If the bubbles are not too numerous, others drilled them out and then remelted. Then you run into issues with color mixing and making turd patties. Better to avoid air bubbles in the first place, then have to try to fix them later. You mentioned working with virgin glass. Is it possible when melting a block to use all glass that has seen the same temp? Start on an even playing field, all things the same? Of course there is probably no way to tell which glass is virgin, unless it is sourced from certain blowers that use it exclusively. Would this severely limit your color selections? Agree that the knappers are too big of a possible client group to walk away from. If anyone can solve this dilemma, it is you, James!
|
|
|
Post by MsAli on Jun 24, 2018 10:44:04 GMT -5
Love that vase Did you show them what Stan did? Bubbles are a very hard to get rid of in glass
|
|
jamesp
Cave Dweller
Member since October 2012
Posts: 36,612
|
Post by jamesp on Jun 24, 2018 11:24:52 GMT -5
Bummer about the blasted bubbles. Keep experimenting with solutions until you find one. That knapping crowd is too good a prospect to just let it go without at least trying to find a way to eliminate the bubbles. I can tell I am teasing them  . Just because Stan can knap that glass w/bubbles does not mean the others will attempt. They know Stan can knap a slab of rubber. That rascal is good at it. He did break the end inch off on one of the spears due to a bubble though.
|
|
jamesp
Cave Dweller
Member since October 2012
Posts: 36,612
|
Post by jamesp on Jun 24, 2018 11:30:25 GMT -5
problems: hard glass that has already seen 2200F which decreases flow, increases viscosity shards stacked are air catcher/trappers solutions: yep, longer hold at highest temp(done, using 30 minutes), but an hour would be a good move. Higher temp, since this is recycle and has seen 2200F, increase from 1500F to 1575 maybe 1600. You may boil it at those temps = many more bubbles smaller pieces thinner slab OK Jean, I could open the kiln at max temp and stir the glass. Yes changes pattern but can assist bubbles coming to top. I have opened it at 1200F baking eye moisture and scorching hand/arm in seconds, best wear protection. 1500F certainly wear protection Possibly re-melt, that particular color rich slab would probably have serious color mix at re-melt and turn into big brown patty turd. Some knappers use 'abo' techniques. (Aboriginal) and don't use a jig, like Native man used. They would be OK with the bubbles. So, sounds like the biggest problem is in choosing the glass. Bits that have seen higher temps are "harder," if you will, and won't let air bubbles escape. Some people's solution was to open the kiln while hot and stir. They emphasized wearing protection to prevent bodily harm. (Careful! Burns are painful, but will heal over time. You don't get a new set of eyeballs.) If the bubbles are not too numerous, others drilled them out and then remelted. Then you run into issues with color mixing and making turd patties. Better to avoid air bubbles in the first place, then have to try to fix them later. You mentioned working with virgin glass. Is it possible when melting a block to use all glass that has seen the same temp? Start on an even playing field, all things the same? Of course there is probably no way to tell which glass is virgin, unless it is sourced from certain blowers that use it exclusively. Would this severely limit your color selections? Agree that the knappers are too big of a possible client group to walk away from. If anyone can solve this dilemma, it is you, James! Best bet - bump the temp up a bit. But the most probable solution is to hold maximum heat longer to give the bubbles time to rise. That does cost money humping it at 7000 watts. Very few internal bubbles on the melt plate above, but there are surface bubbles which is a step forward.
|
|
jamesp
Cave Dweller
Member since October 2012
Posts: 36,612
|
Post by jamesp on Jun 24, 2018 11:35:59 GMT -5
Love that vase Did you show them what Stan did? Bubbles are a very hard to get rid of in glass Unique vase eh Allison ? It melt blobbed well. It was thick which presents tumbling issues. Yea the bubbles are a common problem in all sorts of glass work. Oh yes, showed them what Stan the Man can do to the ole glass. He has been in the knapping rodeo a long time.
|
|
jamesp
Cave Dweller
Member since October 2012
Posts: 36,612
|
Post by jamesp on Jun 24, 2018 11:39:37 GMT -5
Converted saw to water. Using rubber strip to grab 4 bricks at a time. Love it, no more stinky greasy saw oil. Saw will have to be sprayed down with fogger oil though. Opening saw whilst running - just not right. It's only water. 
|
|
|
Post by MsAli on Jun 24, 2018 12:30:00 GMT -5
Converted saw to water. Using rubber strip to grab 4 bricks at a time. Love it, no more stinky greasy saw oil. Saw will have to be sprayed down with fogger oil though. Opening saw whilst running - just not right. It's only water.  One hell of a operation you've got going
|
|
jamesp
Cave Dweller
Member since October 2012
Posts: 36,612
|
Post by jamesp on Jun 24, 2018 13:00:04 GMT -5
Converted saw to water. Using rubber strip to grab 4 bricks at a time. Love it, no more stinky greasy saw oil. Saw will have to be sprayed down with fogger oil though. Opening saw whilst running - just not right. It's only water.  One hell of a operation you've got going That saw has been sitting around doing little of nothing. It has seen many a rock over the years. It was bored and wanted a job to do. The clean out was a monster, must have had close to 15 gallons of rock mud in it. she is smiling now.
|
|
|
Post by MsAli on Jun 24, 2018 13:55:08 GMT -5
Poor rocks not feeling the love
|
|
|
Post by hummingbirdstones on Jun 24, 2018 19:36:48 GMT -5
Best bet - bump the temp up a bit. But the most probable solution is to hold maximum heat longer to give the bubbles time to rise. That does cost money humping it at 7000 watts. Very few internal bubbles on the melt plate above, but there are surface bubbles which is a step forward. I understand about the cost, but if you can almost eliminate bubbles or eliminate them entirely and the knappers will pay top dollar for the bricks, you've got it covered and then some. The question I guess is it worth the cost of experimentation even if it doesn't pan out?
|
|
jamesp
Cave Dweller
Member since October 2012
Posts: 36,612
|
Post by jamesp on Jun 24, 2018 22:36:37 GMT -5
Poor rocks not feeling the love Lol, they have been neglected on many occasions. I must say the glass is a more consistent material. Aside from bubbles. Opening the tumbler to few failures is a rush. Rocks on the other hand....
|
|
jamesp
Cave Dweller
Member since October 2012
Posts: 36,612
|
Post by jamesp on Jun 24, 2018 23:07:35 GMT -5
Best bet - bump the temp up a bit. But the most probable solution is to hold maximum heat longer to give the bubbles time to rise. That does cost money humping it at 7000 watts. Very few internal bubbles on the melt plate above, but there are surface bubbles which is a step forward. I understand about the cost, but if you can almost eliminate bubbles or eliminate them entirely and the knappers will pay top dollar for the bricks, you've got it covered and then some. The question I guess is it worth the cost of experimentation even if it doesn't pan out? Lots of pretty glass to melt here but not a lot of melting technique has been required. Lame in the technique department. Hat's off to glass hobbyist that start from scratch. Did some studying. Reading, it says up to 4 days at high heat for 4 inch thick glass. A day for 2 inch thick. Solution to that is simply do melt slabs at 1/4 to 3/8 inch thick and stay away from bricks. Book says 2 to 3 hours for such slabs and that is no cost issue at all. So the next slab will get the 2 hour hold. The bricks require a more prep. Like crushing glass to size. Then sawing slabs. Slabs are easier with less prep required. Either brick or slab has many techniques for different effects. With all those scraps it has been easy to make pretty glass without creative technique. The big kiln can do 4 shelves when doing slabs. 4 - 18 inch slabs is a lot of glass.
|
|
jamesp
Cave Dweller
Member since October 2012
Posts: 36,612
|
Post by jamesp on Jun 25, 2018 17:23:12 GMT -5
Some Wimmins made comments about having to ask my wife about forever color combinations/coordinations. Check out my color picks(all by myself) for a classic teal/pink/brown/white mix. Us mens can see too and we are not all color blind.(looking for at-a-boys) Teal and cotton candy frit glued in too. The 'birds nest' creates stretch as the shard pile implodes making cool flow patterns. Quick and easy to do, no mold needed.   This was my first 'bird's nest' done a couple of days ago(out of man colors  ) Might be my favorite pattern due to stretch and larger features for pendants. Ready for lapper shaping.  This is the bottom shelf melt. A big one. Note it is sectioned off by color. There will be a bit of color overlap at interfaces.  And then added more mass to the teal/pink melt. Should be a full 16 inch slab on both shelves at 1/4 to 5/16 inch thick. Increased hold time at slump and at high heat to allow bubbles to rise. 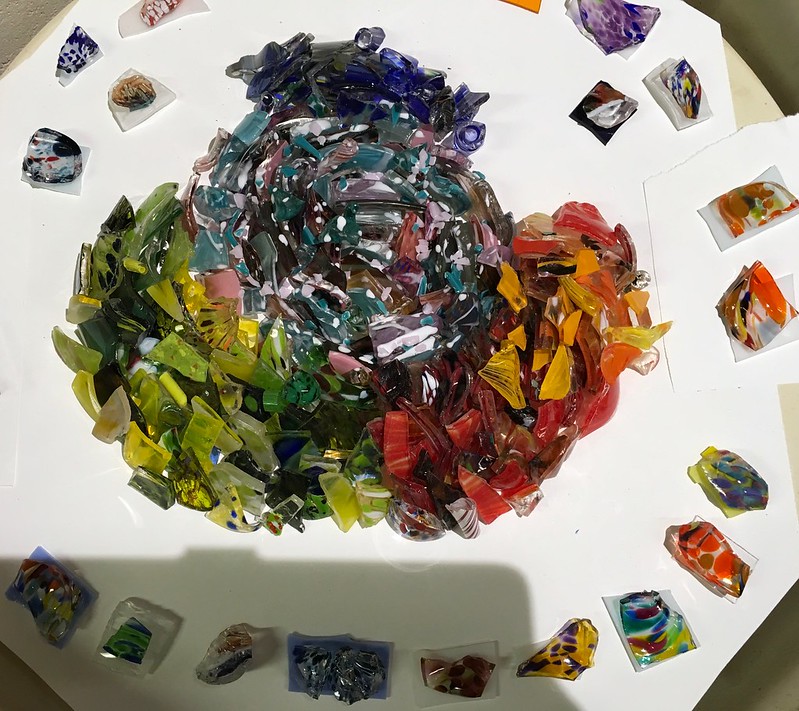
|
|
|
Post by MsAli on Jun 25, 2018 17:31:07 GMT -5
Some Wimmins made comments about having to ask my wife about forever color combinations/coordinations. Check out my color picks(all by myself) for a classic teal/pink/brown/white mix. Us mens can see too and we are not all color blind.(looking for at-a-boys) Teal and cotton candy frit glued in too. The 'birds nest' creates stretch as the shard pile implodes making cool flow patterns. Quick and easy to do, no mold needed.   This was my first 'bird's nest' done a couple of days ago(out of man colors  ) Might be my favorite pattern due to stretch and larger features for pendants. Ready for lapper shaping.  THOSE PASTELS ARE SPOT ON PERFECT!! Good boy!!
|
|
jamesp
Cave Dweller
Member since October 2012
Posts: 36,612
|
Post by jamesp on Jun 25, 2018 17:34:54 GMT -5
|
|